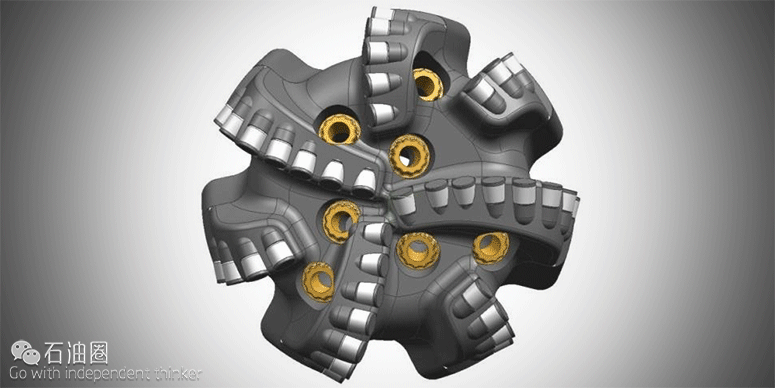
哈里伯顿MegaForce钻头融合了先进的SelectCutter钻头设计理念, 采用了超高效的切削齿平衡布局、高级抗磨蚀胎体材料和改良过的水力学设计。基于哈里伯顿特有的用户操作界面设计流程(DatCISM),MegaForce整体设计工作由ADESM产品线的专家完成。该钻头满足客户对于特殊井况优质钻头的需求,同时具有钻进尺寸更长、ROP(钻进速率)更高的优点。
MegaForce钻头的胎体设计独特,钻头更加耐用,能够长时间保持高ROP,实现钻进尺寸最大化。钻头胎体材料采用钨合金,使其自身的磨蚀损伤显著降低。同时压力平衡设计确保了钻进过程中钻头的稳定性。另外,MegaForce钻头还结合了微型喷嘴设计,钻井过程中流体流动更合理。钻头尺寸的降低也大大增强了导向钻井作业的可控性。
由于采用了SelectCutter技术,MegaForce钻头的切削齿更加锋利、耐用,钻井性能异常强悍,能够维持高ROP、长时间作业。现场实际应用表明,MegaForce的多级力学平衡设计和双切削齿结构使其在超过1000ft钻进范围内都可保持ROP高于20ft/hr,远远超过了同类产品。
技术难题1石油圈原创www.oilsns.com
钻头胎体磨蚀会导致水力效率降低、钻头使用寿命缩短,而钻井过程中通常需要高磨蚀的钻井液来移除钻井碎屑,这无疑会加速钻头胎体的磨损,影响钻头使用。
解决方案
钨合金材质的胎体能够显著提高钻头强度和抗磨蚀能力,提高钻头在高压、高速流体下的作业能力,保持钻头在坚硬地层和高磨蚀地层的钻进能力。
技术难题2
钻头在地层转换带钻进时会发生受力不均匀的现象,使得切削齿更易损坏,降低钻井效率。
解决方案石油圈原创www.oilsns.com
多级力平衡设计能显著改善由于地层不均匀造成的钻头受力不平衡问题,所以MegaForce钻头更加稳定、耐用,切削齿布局更加合理,钻井效率更高。
技术难题3
长水平井和水平分支井钻井过程中经常会遇到坚硬、高磨蚀岩层,这对钻头的导向性能有着极高的要求。
解决方案
MegaForce钻头的尺寸降低了将近14%,使得其在复杂轨迹钻进过程中作业效率提高,此外钻头的微型喷孔优化了钻头水力压力,钻屑清除效率更高,钻头磨损更小。
技术难题4
坚硬地层/高磨蚀地层的钻井作业中钻头的磨损非常剧烈,同时ROP也会降低。此外,地层转换带情况非常复杂,钻头会受到各种作用力影响,极易损坏。
解决方案石油圈原创www.oilsns.com
MegaForce钻头结合了SelectCutter PDC钻头的切削齿,在降低磨损的同时钻进效果更好,整体磨蚀损耗降低40%。
坐标:科威特
在科威特有一口井眼尺寸16in的井中,钻进过程需经过砂岩、石灰岩层。开发商急需寻求一种能够用于坚硬/磨蚀性地层钻井的钻头。根据现场实际情况,哈里伯顿为其量身定制了能够承受高磨蚀、高扭矩作业的MegaForce钻头。
最终,该客户完钻深度几乎为预期的两倍,工作效率大大提高。
通过使用MegaForce钻头,该客户完成了1197ft的钻井计划,平均ROP为32.4ft/h,创下了该油田高ROP下的最长钻进尺寸记录。与常规作业相比,平均ROP提高了62%,钻进尺寸提高了11%,共节约31%的作业时间。石油圈原创www.oilsns.com
坐标:美国Williston 盆地,怀俄明州,Bakken页岩油田。
MegaForce钻头在该油田三口井的钻井作业中表现出了极佳的性能,并在后续的钻井作业中得到重用。
第一口井采用8-3/4in的MegaForce钻头,仅用时68.5小时即完成垂深为8617ft的钻井工作,平均ROP为125.8ft/hr,平均每天钻进2913ft,创造了该油田的ROP记录。钻井作业的前24小时钻进深度就达到了5536ft,在保持高ROP的同时还降低了单位钻井成本。
在第一口井取得巨大成功的基础上,第二口井同样采用了8-3/4in的MegaForce钻头,其表现甚至还要优于第一口井,用时66.5小时即完成了8389ft的钻进作业,前24小时钻进5600ft,平均ROP为126.2ft/hr,又一项钻井作业记录就这样轻松的诞生了。
第三口井为长水平分支井,采用6in的MegaForce进行作业,钻进距离4133ft,同样保持了高ROP和低成本,前24小时钻进2654ft,同样是该油田同类钻井作业的最快记录。
坐标:美国犹他州,落基山脉
在采用MegaForce之前,该地区油田开发商以某个采用最新技术、尺寸为7-7/8in的钻头为标准,为该地区钻井作业建立了一套“钻井考量标准”。但是在使用MegaForce钻头后,该标准明显不适用了。MegaForce将该地区的钻井效率显著提高, ROP平均提高20%,钻进尺寸提高31%,而且钻头的磨损程度也降到了历史最低。
坐标:东德克萨斯石油圈原创www.oilsns.com
在使用MegaForce钻头之前,该地区使用8-3/4in钻头的最佳纪录为:最大钻进尺寸827ft,平均ROP为20.6ft/hr。使用MegaForce之后,该地区的钻井效率明显提高,作业纪录也被轻松打破。钻进尺寸达到918ft,平均ROP 22.1ft/hr,分别提高了18%和25%。
坐标:Permian 盆地
开发商将MegaForce的钻井性能与该地区多口井的钻井纪录进行对比,以单次下钻作业为例,MegaForce的钻井效率为最高,通过多次钻井实际应用考察, MegaForce将钻进尺寸和ROP分别提高了12%和24%,提速效果显著。石油圈原创www.oilsns.com
小编手中还握有MegeForce钻头和Halliburton公司其他产品的更多资料哦,想获取?很简单:请将此文章分享至朋友圈,发送截图和邮箱地址至石油圈微信后台。小编会将资料打包奉上,发送至您的邮箱!还有机会与技术专家沟通交流哦~
来自/Halliburton 译者/张德凯 编辑/Leia
The Halliburton MegaForceTM bit features advanced SelectCutterTM PDC technology, ultra-efficient cutter layout force balancing, improved erosion resistant material and enhanced hydraulics. Designed for an operator’s specific application by one of our Application Design Evaluation (ADESM) service specialists using our industry-unique Design at the Customer Interface (DatCISM) Process, the result is a matrix bit with a combination of higher ROP and longer intervals drilled than any other bit.
Case Study1
A customer looked to Halliburton’s Drill Bits and Services for a solution to drilling through a hard and abrasive formation in Kuwait. Halliburton recommended the MegaForce Drill Bit with SelectCutter PDC tech?nology to provide a faster rate of penetration (ROP) with longer drilling intervals. This solution enabled the customer to drill almost double the planned footage.
The customer needed a robust drill bit for a vertical 16-in. hole section through sandstone and limestone. The customized bit needed to endure high abrasiveness and repel the high torque at the bottom.
The matrix body of MegaForce drill bit is designed to stay sharper longer, thereby providing more footage at higher ROPs. The bit’s Advanced Tungsten Carbide Matrix material reduces erosion and wear while the multi-level force balance increases bit stability during drilling. The Micro nozzles of MegaForce drill bit enhance hydraulics to improve fluid flow across the cutting structure. The reduced drill bit length of MegaForce drill bit increases directional control.
The MegaForce drill bit has an aggressive cutting structure due to the SelectCutter technology keeping the elements sharper for longer periods. This capability enabled more footage to be drilled at higher ROPs. The bit’s multi-level force-balancing technology, along with the optimized dual-row cutting structure, enabled an over 1,000-ft section to be drilled at a faster ROP than the field best of 20 ft/hr.
The MegaForce bit drilled 1,197 ft at an average ROP of 32.4 ft/hr and delivered the longest interval with the fastest ROP in the field. This perfor?mance provided an 11% improvement in footage drilled with a 62% increase in the ROP. The results provided the customer with a 31% time savings.
Case Study2
Hard-to-drill applications across the United States have long challenged the limits of drill bit performance, demanding impact and abrasion resistance, which typically means sacrificing penetration rate for durability. Difficult formations such as the Bakken shale are laden with transition zones and conglomerates and serve as the “proving grounds” for advancing bit technology, where the objective is always the same: drill an entire hole interval in a single run at optimal rate of penetration (ROP). Halliburton’s MegaForce bits incorporate new cutter, materials, and design technologies that generate a significantly higher standard of performance than is typically accepted for hard/ abrasive drilling. Featuring the SelectCutter PDC cutters, the industry’s most advanced PDC technology, the erosion-resistant MegaForce bit design integrates the key factors that contribute to longevity and faster ROP. When paired with Halliburton’s Design at the Customer Interface (DatCISM) process, the MegaForce bits deliver longer runs at faster penetration rates than ever before.
Hard/abrasive drilling accelerates cutter wear and reduces ROP, while transition drilling increases susceptibility to cutter impact damage due to the dynamic forces applied to the brittle diamond material.
- MegaForce bits incorporate SelectCutter PDC cutters, which remove significantly more rock with substantially less wear, exhibiting 40% greater abrasion resistance.
Erosion of the matrix material shortens bit life and alters hydraulic efficiency. An abrasive slurry at the bit face with the high flow rate typically needed for hole cleaning can initiate erosion in conventional matrix material, limiting bit performance.
- A proprietary tungsten carbide mix in the matrix drill bit material provides greater erosion resistance and strength, accommodating increased flow rates and pressures that otherwise would compromise material integrity and limit performance in hard/abrasive formations.
Transition drilling through different formations generates unbalanced force loading on bits, making cutters more susceptible to breakage and compromising drilling efficiency.
- Multi-level force balancing modifies the cutter placement, stabilizing the drill bit and providing even distribution of the durable cutting force during transitional drilling. The interface optimizes the depth of the cut on adjacent cutters, improving overall drilling efficiency.
Extreme horizontal well profiles and long lateral sections through hard/abrasive rock test the directional responsiveness of bit designs already exposed to the harshest formations.
- The bit-to-bend distance in a MegaForce bit has been reduced by 14% to extend fatigue life in the connection while “micro” nozzles optimize hydraulics to clear cuttings and minimize erosion.
Case Study3
Williston Basin:In three Bakken shale wells in Wyoming, MegaForce bits continue to improve ROP on subsequent installations. In the first well, an 8 3/4-inch MegaForcebit drilled the entire 8,617-foot vertical section in only 68.5 hours, producing an excellent ROP of 125.8 ft/hr, an operator record for the county. The bit drilled 5,536 feet in 24 hours and averaged 2,913 feet per day, providing the fastest ROP and lowest cost per foot among the offsets. A second well, also drilled with an 8 3/4-inch MegaForce bit, surpassed the results in the first well, drilling an 8,389-foot section to TD after only 66.5 hours. The bit drilled 5,600 feet in 24 hours with a ROP of 126.2 ft/hr, another operator record for the county. Finally, in a long lateral interval of a third well, a 6-inch MegaForce bit drilled 4,133 feet of the Three Forks formation at the fastest ROP and lowest cost per foot, including drilling 2,654 feet in 24 hours to establish a Williston Basin 24-hour Three Forks footage record.
US Rocky Mountains:A mountain well in Utah, the field benchmark performance of 7 7/8-in. bits, shown in red, was well-established, using what was then considered to be latest-generation technology. The introduction of MegaForce bit technology produced immediate performance improvements, with the MegaForce bit drilling 31% more footage at a 20% increase in ROP over the same section, and delivering a better dull grade than all previous designs.
East Texas: In Leon County, Texas, an 8 3/4-inch bit performance had topped out with a maximum footage of 827 feet at an average ROP of 20.6 ft/hr. MegaForce bits immediately exceeded that performance to establish new field benchmarks (shown in red), drilling 918 feet at 22.1 ft/hr for 18% greater footage and 25% faster ROP than the best offset.
Permian Basin:In the Permian Basin, where data from multiple wells is available for comparison, the MegaForce results(shown in red) exceed past field performance records in terms of average ROP and footage drilled in a single run. Over multiple runs, the enhanced MegaForce bits delivered as much as 12% greater footage and up to 24% faster ROP.
未经允许,不得转载本站任何文章: