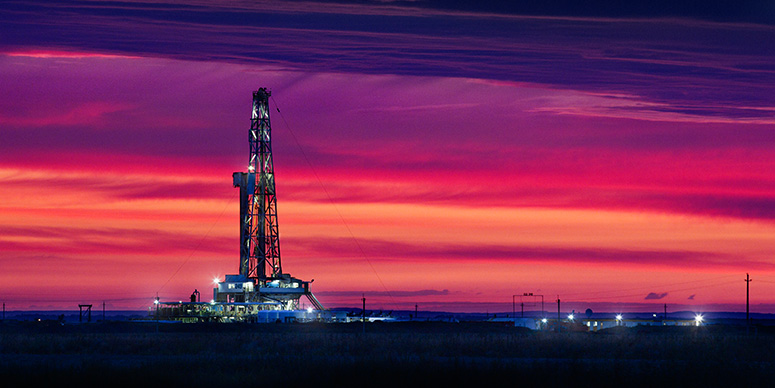
煤层气井的有效排水采气工艺一直是业界难题,传统型的潜油电泵和螺杆泵系统均具有一定的局限性,比如前者易受井液中固相颗粒影响而发生阻塞事故,后者的地面电机运转噪声较大,当作业井场距离住宅区较近时,常引起居民的不满。本文在分析潜油电泵和螺杆泵系统优缺点后,创新性地提出了电潜螺杆泵系统,耦合了潜油电机和螺杆泵,形成了诸多技术优势,让我们通过下文一起了解学习。石油圈原创www.oilsns.com
在过去的数十年间,相关学者研发出多种人工举升技术用来解决煤层气井排水采气难题。工艺的核心理念是降低静水压力,释放气体,增加产能。目前,电潜螺杆泵(以下简称ESPCP)的研究受到普遍关注,它利用电潜泵(以下简称ESP)的潜油电机直接驱动螺杆泵(以下简称PCP)举升液体,集合了无杆采油系统、井下电机驱动和螺杆泵的优点。
螺杆泵和潜油电机的结合使系统工作平稳安静,效率更高、使用寿命更长。用于排水采气井的ESPCP井下布署位置往往距离地面较近,当井场临近居民区或其他易受影响的区域时,该系统安静运行的特征优势便会凸显出来。
煤层气井排水采气工程向来是困扰业界的难题,这是由于煤层位置远低于地下水位,深度一般远超2000英尺。传统型的离心泵或油田ESP日最大排水量不会超过250桶。
为了解决这个难题,部分运营商超速运行离心泵,期间需要周期性启停离心泵避免过载现象发生。实际上,这样的操作模式不仅效率低下,并且会缩短泵和电机的使用寿命。此外,大多数离心泵在这种模式下流通通道会变窄,易导致阻塞事故。那么问题来了,究竟哪种离心泵才适用于这类低效煤层气井呢?答案就是ESPCP,它将ESP和PCP的技术优势完美地结合在一起,很好地解决了这个工程难题。石油圈原创www.oilsns.com
PCP系统石油圈原创www.oilsns.com
PCP是一种内啮合的密闭式泵,主要工作部件由具有双头螺旋空腔的衬套(定子)和在定子腔内与其啮合的单头螺旋螺杆(转子)组成。这样的结构设计使系统的容积流率正比于旋转速率,同时也正比于泵送液体所获得的低水平剪切力。
它的工作原理是靠空腔排油,即转子与定子间形成的一个个互不连通的封闭腔室,当转子转动时,封闭空腔沿轴线方向由吸入端向排出端方向运移。封闭腔在排出端消失,空腔内的原油也就随之由吸入端均匀地挤到排出端。
同时,又在吸入端重新形成新的低压空腔将原油吸入。这样,封闭空腔不断地形成、运移和消失,原油便不断地充满、挤压和排出,从而把井中的原油不断地吸入,通过油管举升到井口。系统内部流速低,容积保持不变,压力稳定,因而不会产生涡流和搅动。
由于转子啮合密封于定子腔内,使PCP在不同有效深度且低流速下的工作效率仍较高。此外,由于煤层气井井液中可能存在压裂砂、煤粉或其他较大的固体颗粒,PCP系统的低剪切速率更利于泵送井液。石油圈原创www.oilsns.com
PCP系统平稳、协调统一的工作特性使其在不同的含气量或流速下更具可操作性。此外,在低流速下高泵效也有利于降低系统运行功率需求。Franklin Electric公司最近研究发现,液面深度范围在900~1300英尺的气井中应用ESPCP系统时,系统所需功率可低至600~3000瓦,大大节约了作业成本。
然而,事物都具有两面性。PCP系统也具有一定的自身局限性,一般使用地面电机长驱动轴带动运转,这种模式容易引起诸多问题。电机运转噪声较大,当作业井场距离住宅区较近时,常引起居民的不满。此外,如果待治理气井为水平井,长驱动轴下井过程中需要衬套与轴承等机械构件的协调作用才能较好地贴合井轨迹,从而到达目的井段。这样的操作会磨损泵轴,增加了运营成本。
ESPCP系统石油圈原创www.oilsns.com
ESPCP的研制,耦合ESP的潜油电机和螺杆泵机构,成功弥补单一PCP短板的同时也带来了一些系统优势。比如说,无需搭配变速箱,消除了安全运行的隐患。螺杆泵对控制命令的反应速度变得更加快捷。原来的地面电机驱动时,扭矩需要通过长达几千英尺的驱动轴向井下传递,导致电机和泵的分钟转速(RPM)变化存在明显延迟;而当电机位于螺杆泵下端时,扭矩变化可即时地传递给泵,基本无延迟。石油圈原创www.oilsns.com
将电机布署在井下的另一个好处是可在螺杆泵上端安装一个高强度单向阀,防止电机停止运行后井液碎屑回落至螺杆泵内部。当电机再次启动后,只要螺杆泵和管柱选型能够承受一定的液体流速,沉淀在单向阀的碎屑就可在液流作用下带至地面。相对来说,传统的地面电机长轴驱动PCP,清除碎屑需要起出泵体才可完成,增加了运营成本和非生产性时间。
由于ESPCP系统运行平稳、可防止碎屑沉积以及潜油电机和螺杆泵紧密耦合等特性,使该系统可灵活控制气井井筒内的液面变化。地面控制柜通过电流信号控制井下潜油电机启停,安装在井下的液面传感器与控制柜联系在一起。由于ESPCP不需要安装长驱动轴,相对增加了油管输油尺寸并减轻了电机震动影响,这便于传感器安装且工作稳定、可靠性强。
ESPCP正常运转需要一套泵控制系统,其中包括变频器来控制电机转速和图形用户界面(以下简称GUI),安装调试人员和工作人员通过交互界面调控系统参数。
一家位于美国西北部的中型能源公司目前在低效煤层气井中已成功应用14套ESPCP系统,下入深度为3300英尺。这些井次之前应用的是ESP系统,井液中的砂砾、煤粉、石蜡和无机盐等固相颗粒不断沉积在泵和电机部件,导致ESP经常发生阻塞事故,频繁关停,影响正常生产。应用的第一套ESPCP系统正常运行了16个月,期间未出现阻塞停泵事故,同时煤层气产出速率增加了一倍,效果显著。石油圈原创www.oilsns.com
螺杆泵、电潜泵特点对比:
- 螺杆泵优缺点:可处理井液固相颗粒,可用于高气体含量井,适用于高压井况作业,工作效率高,排量较低;
- ESP系统优缺点:安装位置较浅,运行平稳安静,运行状态监控,适用于大斜度井和水平井;
- ESPCP:同时具备以上两种系统的优点。
总之,ESPCP结合了PCP和ESP的优点,其在复杂煤层气井况下的应用也得到了验证,在煤层气排水领域的应用前景是非常广阔的。
Different artificial lift technologies have been used for decades to dewater coalbed methane (CBM) wells to reduce hydrostatic pressure and release the gas for production. Among the newest is the electric submersible pump (ESP) using progressive cavity pump (PCP) technology, known as an ESPCP
Close coupling between a PCP and a submersible electric motor enable these units to run more quietly, pump more, and last longer. And because of their lower profile above ground, submersible pumps lend themselves to gas operations near residential areas and other locations where aesthetics and quiet operation are a priority.
Dewatering CBM wells can be difficult because coal seams typically lie far below the groundwater level, often at depths greater than 2,000 ft. Conventional centrifugal water-well pumps and standard oilfield ESPs struggle at typical flow rates of wells of 250 B/D or less.
To overcome this, some operators overspeed a centrifugal pump, which requires start and stop cycles to avoid overpumping. Such operation is inefficient and shortens pump and motor life. In addition, most centrifugal pumps that operate in this range tend to have small flow passages and become easily clogged. A different style of pump is required to operate these “low and slow” wells efficiently. The ESPCP, which combines the benefits of the ESP and the PCP, meets this need.
PCP Systems
A PCP transfers fluid by advancing it through a sequence of fixed-shaped, discrete cavities, as the rotor is turned. This leads to the volumetric flow rate being directly proportional to the rate of rotation, and to low levels of shearing being applied to the pumped fluid. The individual pump cavities are tapered toward their ends and overlap in the axial direction with neighboring cavities so at any given instant, multiple cavities are open and discharging fluid. This makes for smooth fluid flow, with no pulsing action.
Because the rotor is well sealed within the cavity walls, the pump is effective at low flow rates from significant depths. The pump’s lack of shearing action also makes it good for pumping fluids that contain fracturing sand, coal fines, or even large particles, typically present in CBM dewatering applications.
Also typical are varying levels of gas and varying flow rates, which the PCP’s smooth and uniform operation is able to handle more easily. Additionally, the high pump efficiency helps to keep the power requirements modest at low flow rates. Franklin Electric has found that power levels for its ESPCP systems can be as low as 600 W to 3 kW to maintain desired water levels at depths of 900 ft to 1,300 ft.
PCP systems have traditionally used aboveground motors with long drive shafts, but this can pose problems. The motors are noisy and if used near residential areas are often considered visually objectionable. If the well has a horizontal design, the drive shaft approach requires mechanical support such as bushings or bearings to negotiate the curve built into the well path. These will wear out, which increases operational costs.
Submersible PCP Systems
A better approach is to use a submersible PCP that directly couples the motor to the pump. There are several advantages to this tight coupling. No gearbox is involved, eliminating a source of reliability problems. The pump also responds more rapidly to changes initiated from the controls. With a topside motor, the torque transmitted through a shaft possibly thousands of feet long causes a lag between changes in motor revolutions per minute (RPM) and changes in pump RPM. By placing the motor downhole with the pump, a change in the pump can be instantaneously detected in the motor.
Another advantage is that placing the motor downhole enables a heavy-duty check valve to be set atop the unit to prevent debris from settling into the pump while it is turned off. As long as the PCP and pipe diameter selected enable a sufficient operating flow rate, sand that settles on the check valve will be driven upward to the surface when the motor starts again. On a traditional PCP driven by shaft from a surface motor, the pump must be pulled to dislodge the debris, thereby increasing operating cost and nonproductive time.
Because of smooth on/off pump operation, prevention of debris settling, and the close coupling of the motor and the pump, a very tight level of control of the water level in the well is possible. A control unit on the surface is connected electrically to the pump motor underground, and a downhole level sensor can be mounted in the well and connected to the control unit. Mounting this sensor is easier and can be done more reliably because of the reduced tubing size and reduced vibration that result from eliminating the drive shaft.
The ESPCP needs a pumping control system, which includes a variable frequency drive to control motor speed and a graphical user interface (GUI) through which installers and operators can adjust pumping parameters. The GUI is web-based and device independent, using common terminology. The interface screen is highly intuitive, allowing virtually every aspect of pump operation to be adjusted to achieve maximum efficiency and enabling critical production parameters, such as gas concentration, to be monitored.
Fourteen ESPCP systems are being used by a mid-sized energy company operating in the northwestern United States in low-producing CBM recovery wells down to depths of 3,300 ft. The systems replaced were ESPs that were subject to clogging and frequent shutdowns because of sand, coal fines, paraffin, and salt accumulating in the pump and motor. The first ESPCP installed has operated for 16 months without clogging and the rate of methane recovery from the well has doubled.
未经允许,不得转载本站任何文章: