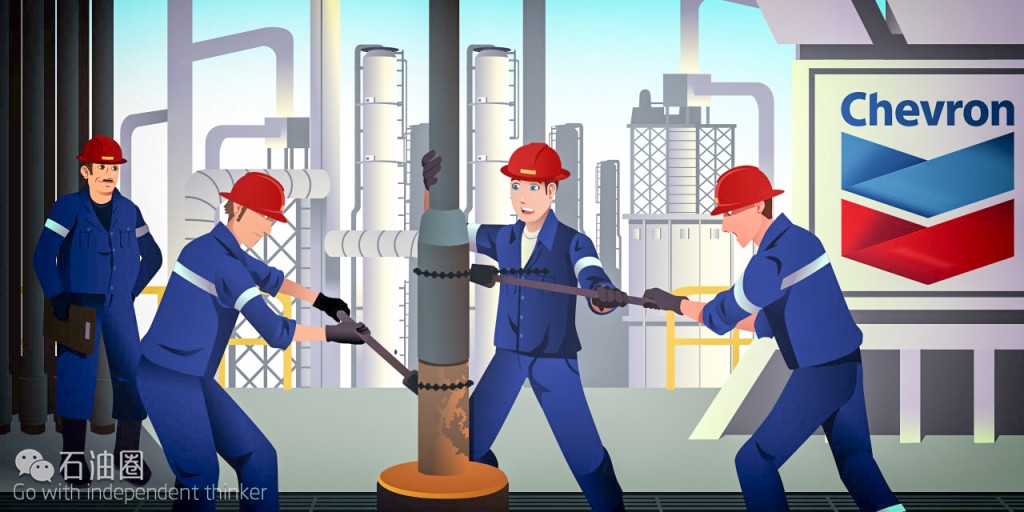
油价越低,人们就越轻视石油安全,而安全却是一切油气作业中的重中之重。雪佛龙应用其开发的OESM系统在油气安全领域取得了令人瞩目的成绩,这套系统到底有何神奇之处?雪佛龙的企业安全文化到底如何?接下来石油圈将会带您一探究竟~
雪佛龙Wes Lohec HSE主管指出,即使是最聪明、最称职、最勤勉的员工都会在他们的工作中犯错。“人无完人,所以现在的问题是:我们如何避免人为的错误引发一场大灾难”。不管是从个人还是从公司的角度出发,雪佛龙面临的挑战是在作业中严格遵守原则,即在每一项作业中,都严格按照其在过往作业中仔细研究出的方法和程序进行。雪佛龙意识到:他们的安全工作是永无止境的。
雪佛龙能够在油气领域安全作业得益于他们在做任何事情时都设有层层的安全保障。雪佛龙花费了20多年时间,设计并改善了一套有完整安全文化支持和环境管理的系统。雪佛龙把这套系统称为“卓越运营”系统。这一切都基于雪佛龙对于自己能够通过危机管理、阻止事故发生的信心。
对卓越运营的持续追求
由于雪佛龙业务众多,其工作地点遍布全球,要想建立一套持续且高效的安全文化并不是一件容易的事情。为了解决这些问题,雪佛龙开发出了一套卓越的运营管理系统(OEMS)。OEMS是雪佛龙管理整个公司作业安全、个人安全、环境问题、可靠性问题以及效率问题的一个系统性方法。OEMS的一个终极目标就是确保雪佛龙的员工和承包商的人身安全。
2015年不仅是雪佛龙总体表现最好的一年,而且也是他们发生事故最少的一年。他们在保证核心劳动力安全、作业安全和环境安全方面超额完成目标。雪佛龙雇员及其承包商在2015年创造了每200000个工时损失0.018工时的记录。他们同时创造了最少机械事故率的记录。在2015年,在雪佛龙全球内的77个作业区获得了零人身安全伤害奖,远远超过2014年的10个。2015年,42个作业区获得了雪佛龙作业安全零事故奖,而2014年只有36个作业区受此嘉奖。
卓越运营5大目标
雪佛兰的OEMS就作业安全管理、个人安全管理、健康管理、环境管理、可靠性和效率管理上提供了严格的方法。雪佛龙严格执行作业流程、标准以及监管要求以确保其合规性,积极识别和管理风险事件,确保有应急响应措施。要想提高整体安全表现,需要关注安全、健康、环保、可靠、高效这五个方面,这主要是为了创造一个无事故、无伤害的工作环境,减少主要工作环境的健康风险,识别并减少作业中的环境和安全风险,并使用业内最可靠和完备的设备进行作业,有效利用自然资源和资产。雪佛龙致力于将OE系统管理扩展到他们的承包商、供应链合作者以及作业区域所有人员,而不仅仅是雪佛龙公司的内部雇员。
在阻止人身伤害方面,雪佛龙达到了行业内领先水平。不过,雪佛龙仍然发生过人员死亡事故,这对他们来说是不能接受的。雪佛龙在安全上的关注取得了一定效果,但是他们丝毫不松懈。例如,在2015年前雪佛龙的员工和其承包商员工保持了公司历史上最长的无致命事故时间,即47.7亿工时。雪佛龙对每一起险情和死亡事故都彻底调查,这样他们可以了解其根源并从中学习经验。然后他们会在整个公司范围内分享这些经验教训并应用在他们的日常实践中,同时雪佛龙也与行业内的其他公司合作,改进作业流程,防止类似事故的发生。
在雪佛龙零事故的追求下,在2015年他们引入了一个严重伤害和死亡(SIF)指标,这个新规定要求他们加强对事故和险情的审查。Lohec说道,“当你开始关注一些重伤事故或者可能致死事故亦或严重操作安全事故时,你就开始发现系统中存在的种种弱点。或许我们只有一道保障措施来防止事情恶化。因此,我们正在努力的找出我们保障措施中的弱点并进行加强完善”。他引用了高空落物作为例子,一个安全网能够有效的减少伤害;虽然安全网并不能够阻止工人制造高空落物,但是它确实有效的防止了严重伤害。
除了学习应用SIF指标之外,雪佛龙在加州SAN Joaquin Valley业务区(SHVVY)使用验证和确认程序用以评估员工在工作中和在一些高风险活动中如电力系统工作和在操作起重设备的能力,并根据实际需要指导工人。
SJVBU也实行了人力绩效培训,通过评估和整合个人的潜能,为员工提供实用工具来减少潜在的错误发生。在2015年,通过这一系统,SJVBU培训了超过2300名工人,按照计划,明年还有1000名工人需要培训。
了解员工的一些容易犯错误的问题也可以有效的阻止事故发生。例如,雪佛龙上游公司欧洲分公司总经理Greta Lydecker了解到一名员工非常没有耐心,如果安排他做一些重复性的工作,他可能就会跳过工作中的一些步骤,这可能会引起一场事故。通过简单的把工作步骤写下,并检查他是否按照步骤完成,我们能够减少这类错误发生的风险。
应用最优方法和最好的技术防止事故发生
雪佛龙已经尝到了在确保安全作业中应用最优方法的甜头,下一步他们希望能够通过使用新技术来阻止事故发生。
雪佛龙运输公司(CSC)对OE的广泛使用创造了业内领先的安全和环保成果。在2014年和2015年两年内,CSC做到了零损失工时,CSC旗下的船只自2003年11月以来从来没有发生过原油泄露或者燃油泄露。这一切的基石是在2012年完成的避免重大事故专项研究。它对CSC的工作程序和政策进行了广泛的研究,以减少作业安全事故发生的可能性。根据这份报告衍生出一系列的避免船只发生灾难性事故的计划。作业中太过复杂的程序都被重新编写,而且更加透明、更加简单。海员的培训也更加的严格和标准化。2015年,CSC在苏格兰Glasgow开设了一个世界领先的海洋研究和开发中心,用来给公司的海员提供严格的训练,并且还在加利佛尼亚San Ramon、安哥拉卢旺达、印度孟买安装了航行模拟器。
同时,他们改进了新船的检查程序来确保新的设计能够减少事故的发生率。从造船厂接收新船的程序和检查更加严格,改变管理模式是减少风险的最佳方法,并对已有的规定进行修改完善。
雪佛龙管道公司总裁Al Williams表示,该系统就是卓越运营系统。它是在雪佛龙对程序安全、资产完整性和环境管理关注下的一个自然产物。
除此之外,CSC参与的几个国际组织如国际石油公司海洋论坛以及国际天然气油轮及码头运营商协会等为CSC提高其在全球范围内的油轮、LNG运输船、陆地终端以及海上支持船的安全和环境标准提供了大力支持。
雪佛龙上下都持续的评估并提高自己的安全作业保障能力。雪佛龙管道公司(CPL)风险管理项目有很多管理网络化运营管道的先进系统运运营在很多国际港口。
CPL是业内首先使用PortVision的公司之一,也是首先在管道控制中心使用24小时监控以及在管道风险管理系统中使用先进泄露检测摄像头和预测分析仪的公司之一。(PortVision是一种在事故发生前发现问题并阻止问题扩大的船只追踪系统。)
2015年雪佛龙管道公司因“持续的安全记录和良好的作业条件”受到了美国石油学会的杰出安全和环境奖奖励,获得了API杰出安全和环境奖。
自始至终正确的解决问题
雪佛龙在项目的整个周期,从计划、设计到建造、运营和停运,自始至终都以正确的方法处理问题。用以更换六个巨型焦炭塔,是可以将原油加热到493摄氏度的设备,该复杂EI Segundo炼化焦炭塔可靠性分析项目获得了由非营利性组织项目管理学会(PMI)颁发的年度最佳项目奖项,这一奖项是项目管理学会所颁发的最高奖项。
雪佛龙综合工程设备部副主管Frank Semancik讲到,“合理的计划,有效的合作保证了这个项目的顺利进行。对老旧焦炭塔的替换将有效的增加炼油厂的可靠性”。
在独特的安全文化背景下,来自世界不同区域的承包商完成了建造、运送、安装整套设备的任务,并在这一过程中实现了零事故。由于安装焦炭塔需要20英尺或者更高的高空作业,项目领导人采用了防坠措施,要求工人使用正常高空作业情况下的两倍数量的安全吊带。项目团队不断举行安全会议,并严防项目中的工具和材料从高空坠落。所以尽管有400人参与了在焦炭塔安装过程中的高空作业,但在整个项目过程中也没有出现跌落事故或者工时损失事故。
EI Segundo炼油厂同时也把对安全的关注扩展到了日常作业中。在2015年它不仅获得了卓越安全奖,而且获得了由美国燃料与石化制造商协会(AFPM)授予的全美最安全炼油厂称号。要取得这一称号需要满足以下五方面的严格标准:首先,企业必须在5年内没有员工或者承包商死亡,其次,企业没有超过4英尺高度的坠落事故,最后,企业在上个该年内没有员工或者承包商因工伤住院。
从EI Segundo炼油厂的焦炭塔更换项目以及它的日常作业中可以看出,保持作业的清晰性和一致性能够有效的阻止事故发生。雪佛龙位于全球的各个事业单位共同分享学习该安全安全运营范例。
在尼日利亚,承包商们往往来自世界各地,拥有着不同的安全文化背景。Meren油田的天然气储集压缩平台的上部甲板在韩国制造后,运送到尼日利亚海域。这个平台从其他八个海上生产平台接收天然气,并通过管道将天然气输送到陆地上的Escravos天然气处理厂。在整个项目过程中,项目负责人用“一个团队理念”提高了这支多样化安全队伍的协作力。在建造这个近四层高的平台的过程中,为了防止坠落和事故,项目组要求所有工作人员在工作区域内都必须装备全身安全吊带。Nigerdock是这个平台上多个组件的分包商,在2014年,Nigerdock在123万工时内没有发生过损失工时事故。
Lohec最后说:“我们必须要坚定的寻找我们安全措施中的弱点并进一步改善这些,这将会帮助我们真正的成为无死亡和无安全事故的石油公司”。
来自/Chevron 译者/曾旭洋 编辑/Wang Yue
Wes Lohec, Chevron’s vice president of Health, Environment and Safety, knows that even the smartest, most capable and most diligent employees will make mistakes during their careers. “Humans aren’t perfect, so the question is: How do we make sure that human error doesn’t lead to a significant incident?”
Our ability to deliver energy safely is focused on building several layers of safeguards into everything we do. We’ve spent more than 20 years designing and improving systems that support a strong culture of safety and environmental stewardship. We call this “operational excellence” (OE). At its foundation is the belief that we can prevent serious incidents by properly managing risk.
“Our challenge is to operate with discipline—to be relentless—in executing the best practices and procedures that have been carefully developed in each of our operations,” Lohec said.
Asia Excellence safety inspection
The Asia Excellence’s gas engineer, Sergejs Skripelevs (left) and Australasia business unit pilot and loading master Cameron Crampton inspect the flange of one of the ship’s liquid lines prior to connecting the loading arms.
Striving for operational excellence
It’s not easy to create and reinforce an effective safety culture given the complexity of our businesses and the diversity of our locations and global workforce. To meet these challenges, we developed the Operational Excellence Management System (OEMS), our companywide systematic approach to manage process safety. One of its end goals is to make sure that our employees and contractors go home safely every day.
In 2015, we had one of our best years in overall performance and our best year ever in preventing serious incidents.
We outperformed 2015 targets across all of our core workforce safety, process safety and environmental metrics. We set a record-low Days Away From Work Rate for our employee and contractor workforce, at 0.018 per 200,000 work-hours, which beat our 2014 rate. We also achieved a record low in motor vehicle incidents.
Preventing serious incidents
We have achieved industry-leading performance in preventing injuries. Nevertheless, we are still experiencing incidents that lead to fatalities, which is not acceptable to us. Our focus on safety works, but it’s an ongoing job. For example, our employee and contractor workforce achieved the longest period without a fatality in company history—477 million work-hours—prior to a fatality in 2015. Each incident and fatality is thoroughly investigated to understand the root causes and learn from them. We then share lessons learned throughout the company and apply them in our daily practices. We are also working with other companies in our industry to improve work processes to help us prevent serious incidents.
In 2015, in our quest for zero incidents, we introduced our Serious Injury and Fatality (SIF) metric, which requires us to intensify scrutiny of actual incidents as well as near misses. In addition to using SIF, our San Joaquin Valley business unit (SJVBU) uses a verification and validation program to assess workers’ competencies at job sites with high-risk activities, such as working on electrical systems. The SJVBU also has implemented Human Performance training, which provides workers with practical tools to reduce the potential for errors by evaluating and integrating personal tendencies. More than 2,300 workers were trained in 2015, and another 1,000 will be trained in 2016.
Workers in Kern River Field SJVBU
San Joaquin Valley business unit (SJVBU) workers standing in Kern River Field, Bakersfield, California. SJVBU uses a verification and validation program to assess workers’ competencies at job sites with high-risk activities.
Applying best practices and technology to prevent incidents
Safe operations result from applying best practices, looking inward to improve safety and using new technologies to prevent incidents.
Chevron Shipping Company’s (CSC) comprehensive commitment to OE has resulted in industry-leading safety and environmental performance. CSC had zero Days Away From Work incidents in 2014 and 2015, and its operated fleet hasn’t had a cargo or bunker spill since November 2003.
Asia Excellence LNG loading
(L to R) Second Officer Dalibor Matijasevic, Chief Officer Olegs Nesterenko and Third Officer Ashvinder Nanda listen as surveyor John Cameron verifies the volume of liquefied natural gas (LNG) loading on board Chevron’s Asia Excellence LNG carrier before the ship’s departure from Barrow Island.
This performance is the result of committed leadership and dedicated employees focused on achieving a common goal—zero incidents. Our Avoiding the Big Incident study completed in 2012 involved an analysis of CSC’s procedures and policies to reduce the possibility of a process safety incident and spawned projects to reduce the likelihood of a catastrophic ship-related incident. Complex procedures were rewritten to be simpler and clearer and review processes for new ships were updated to ensure that designs reduce the risk of incident. In 2015, CSC opened the Marine Learning and Development Center in Scotland to provide rigorous mariner training for the organization.
Chevron Pipe Line Company (CPL) is one of the first in the pipeline industry to adopt PortVision®—a vessel tracking system that helps identify and prevent problems before incidents occur—as well as round-the-clock monitoring in its Pipeline Control Center, advanced leak-detection camera technology and predictive analytics in its pipeline risk management program.
“This system is operational excellence in action,” said Al Williams, CPL president. “It’s a natural outgrowth of our focus on process safety, asset integrity, reliability and environmental stewardship.”
In 2015, CPL received the American Petroleum Institute Distinguished Safety and Environmental Award in the large operator category for a “consistent record of safety and environmentally sound operations.”
Getting results the right way from start to finish
For Chevron, getting results the right way happens throughout the life of a project.
One example is our complex El Segundo Refinery Coke Drum Reliability project to replace six massive coke drums—enormous containers that heat crude oil to 920 degrees Fahrenheit (493° C). The project was honored by the nonprofit Project Management Institute (PMI) with the 2015 PMI Project of the Year Award. The massive project was completed without a single lost-time injury. In 2015, the refinery also received the Distinguished Safety Award and was named the safest operating refinery in the United States by the American Fuel & Petrochemical Manufacturers Association.
El Segundo coke drums
In late January 2013, Chevron’s El Segundo Refinery coke drums arrive from Spain at California’s Port of Los Angeles and are transported two at a time over the course of three weeks via barge into the Redondo King Harbor Marina. The drums measure 100 feet in length and 28 feet in diameter and weigh approximately 400,000 pounds each.
The importance of operational clarity and consistency needed to prevent incidents is shared by all of our business units, many of which are in a different hemisphere. In Nigeria, contractors often speak different languages and come from different cultures of safety. As this business unit’s massive Meren gas gathering compression platform topside was built in South Korea and installed in Nigerian waters, project leaders reinforced a “one team” mentality to improve collaboration among a diverse workforce. Nigerdock, a subcontractor for multiple platform components, reported 1.23 million work-hours without a lost-time injury in 2014.
Workers in Nigeria
Contract workers for Nigerdock, a subcontractor for multiple components of the Meren gas gathering platform in Nigeria. Nigerdock reported 1.23 million work-hours without a lost-time injury in 2014.
未经允许,不得转载本站任何文章:
-
- 甲基橙
-
石油圈认证作者
- 毕业于中国石油大学(华东),化学工程与技术专业,长期聚焦国内外油气行业最新最有价值的行业动态,具有数十万字行业观察编译经验,如需获取油气行业分析相关资料,请联系甲基橙(QQ:1085652456;微信18202257875)