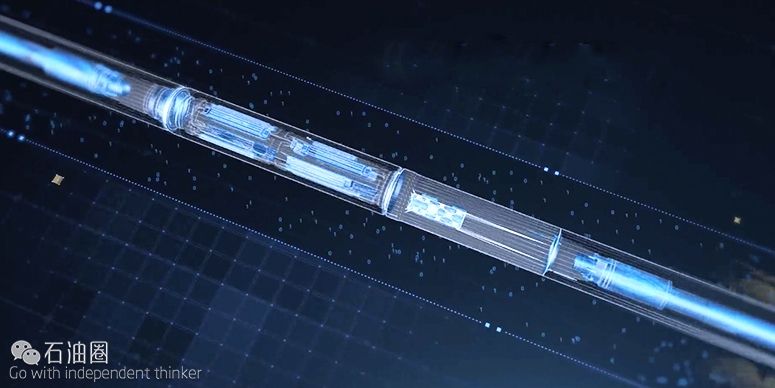
泥浆脉冲遥测(MPT)技术是油气上游领域实时数据传输的核心技术。随着钻井实时数据传输量的不断增加,对高可靠性、高速MPT(HSMPT)技术的需求在不断增长,目前全球很多地区都在使用该技术。然而,由于MPT技术应用环境及其要求的不断变化,现有HSMPT系统的可靠性受到了诸多挑战,例如实现海上现场服务工程师和远程技术支持人员之间的相互交流等。
贝克休斯的自动化HSMPT系统结合了先进的自动化和信号处理技术,同时提高了数据的传输速度和可靠性。目前,aXcelerate PLUS系统已成功应用在了许多超深水钻井环境,该系统一般装配在复杂的井下钻具(BHA)上,同时还提供多种LWD服务,可以带来优质的数据密度,而且不影响整体机械钻速(ROP)。出色的使用效果证明了自动化HSMPT系统具有打破技术局限性的能力,以安全、经济可行的方式完成钻井作业。
挑战逐渐升级石油圈原创www.oilsns.com
HSMPT最初只是为了满足地层评价(FE)的需要,以实现工作过程中实时数据传输的作用,后来HSMPT的使用逐渐扩展到极端井下环境,例如HP/HT井和高粘度钻井液环境,为钻井自动化、优化服务、井眼定位和随钻测压服务提供数据传输功能。
随着技术的进步,新的FE测量模块已被加到BHA中,同时将一些传统的FE测量模块从电缆测井转到了LWD上,因此更多的钻井优化数据需要进行实时传输。钻头技术和整个钻井过程的改进提高了平均ROP,因而需要更快的传输速度来保证数据密度一致。通常,HSMPT能够提供的井下过程相关信息对HSE合规性和降低技术风险至关重要,应用结果表明,这些改变很大程度上增加了钻井作业实时传输的数据量。
同时,钻井过程中出现的新问题使一般的MPT高传输速率变得复杂化,随着作业井深逐渐增加,泥浆液柱造成的MPT信号衰减越来越严重。在使用极具挑战性的泥浆体系(如高密度、高塑性粘度、高固相含量)的应用中,对传输速度要求更高。其他的钻井优化工具(如水力振荡器)在BHA中的添加也增加了HSMPT信道的噪声。
目前,MWD和FE工具已经变得比以前更可靠,并能承受更高级别的振动和粘/滑(VSS),在钻井过程中可接受的VSS等级也提高了。但这些高级别的VSS对解码性能产生了负面影响。此外,在现在应用越来越普遍的大位移井中,MPT已能兼容地面高扭矩和钻井VSS。
钻机、设备、泥浆和管柱变化将导致MPT所处的井下环境及地面状况产生变化,这些情形增加了系统的复杂性,这也对系统克服不同作业环境的差异提出了新的要求。
寻求解决方案石油圈原创www.oilsns.com
虽然10比特/秒(bps)或更高的HSMPT数据率在现场已使用了大约十年,但由于缺乏可靠性,对现存技术的问题需要进行全面分析。结论是通过使手动操作自动化,以及使用先进的信号处理技术可带来明显的改善效果。
新的HSMPT系统将自动化应用于每个现场操作步骤来简化操作,节省了时间并避免容易出错的步骤,如手动输入数据。当某个传输参数已配置在了一个系统上,此信息将被自动分发下去。此外,如流量、深度及其他现场作业中测量到的数据,将使用配置的传输参数进行保存。
简化版的HSMPT系统包含一个井下发射器(脉冲发生器)、泥浆信道和在工具表面侧边的接收器,通常有一个或多个压力传感器。引起MPT传输数据失真的主要来源是泥浆信道和其他可变的失真因素。为了减少失真、改善信号处理过程,该系统采用特别的信号序列来自动调整适应过滤器。
脉冲发生器定期向外发送序列,使地面系统做出调整以适应过滤器来改变信道状况。该过滤器的性能已经经过了测试,并按质量指标保存到了数据库,以便现场人员通过更好的决策来优化解码质量。改良的信号处理算法明显提高了自动化系统的成功率,提高了解码的质量和可靠性。
现场表现性能优异石油圈原创www.oilsns.com
新HSMPT系统在许多超深水钻探区的广泛应用中,获得100%的成功率,所有这些应用都需要大量的实时数据以做出准确的决策。该工具已在全球入井超过60多次,经受了超过5000小时的循环时间和3000多小时的纯钻时间考验,每次作业都能获得超过10bps的物理数据传输速率。该技术可以应用于油基和水基泥浆环境,井深最大8000米(26247英尺)。已成功应用于多种泥浆体系,例如有40趟入井泥浆的PV大于20厘泊(cP),有超过10趟入井泥浆的PV大于40厘泊(cP)。
新的HSMPT系统诸多成功应用案例中,典型之一是在英国北海的一次应用,当时使用的BHA是全球最长、最复杂的BHA之一。系统有能力可靠地传输更多的实时数据,帮助作业者在BHA中加入了多套钻井和LWD服务,提供更多实时参考数据。在一次油基泥浆PV为34cP极具挑战性的应用中,新系统能提供高达15bps的数据传输率。一趟钻完成4635米到6611米(15207英尺到21690英尺)的钻进,循环时间为184小时,确保了较高的工作效率。
增强的HSMPT可靠性和数据传输率,意味着该技术可应用于最复杂的钻井环境,包括超深水钻井以及泥浆条件要求苛刻的环境,这些情况以前都需要手工作业而且还有数据率降回10bps以下的潜在风险。
自动化和易用性扩大了HSMPT的使用范围,减少了技术支持中心和现场工程师不必要的工作量。使得现场服务工程师在钻井作业期间专注于为作业者提供更多的参考数据来提高效率与安全性,以降低总钻井成本。
来自/Baker Hughes 译者/白小明 编辑/Lemon
Mud pulse telemetry (MPT) is the core real-time data transmission technology in the upstream oil and gas industry. The need for reliable high-speed MPT (HSMPT) has grown as the amount of real-time data required while drilling has increased, and it is now used across many regions of the globe. Yet the changing requirements for MPT and the environment in which it must operate have raised complications that have threatened the reliability of existing HSMPT systems to the point where a very high level of user interaction from offshore field service engineers and remote operations support personnel is required.
A new automated HSMPT system from Baker Hughes combines higher automation levels and advanced signal processing to increase both speed and reliability of data transmission. The aXcelerate PLUS system has performed successfully in complex bottomhole assemblies (BHAs) in many ultradeepwater drilling environ- ments, with many LWD services and with outstanding data density and no reduction in ROP. The impressive results demonstrate the ability of an automated HSMPT to expand the technical limit for safe and economically viable drilling operations.
Growing challenges
Initially seen as the real-time data transmission provider for all required formation evaluation (FE) information, HSMPT usage has expanded to provide the enabling data transmission for drilling automation and optimi- zation services and advanced wellbore positioning and pressure-while-drilling services in extreme downhole conditions such as HP/HT wells and high-viscosity drill- ing mud environments. New FE measurements have been incorporated into BHAs. Some traditional FE measurements have moved from wireline to LWD, and additional drilling optimization data are now transmit- ted in real time. Improvements in bit technology and overall drilling procedures have increased average ROP, requiring additional transmission speed to maintain the same data density per meter drilled. Often, the full com- plement of downhole processes that can be provided by HSMPT is critical for HSE compliance and for technical risk reductions. These changes have signifcantly raised the amount of real-time data required while drilling.
At the same time, additional challenges have emerged that complicate MPT in general and high- transmission speeds in particular. As wells are drilled deeper, the mud column that attenuates the MPT signal increases. More challenging mud systems with high density, high plastic viscosity (PV) or high solids content are used in applications that demand a high transmission speed. Additional drilling optimization tools (e.g., agitators) have been added to BHAs and create superimposed noise to the HSMPT channel.
As drilling, MWD and FE tools have become more reli- able and able to withstand higher levels of vibration and stick/slip (VSS), acceptable VSS levels during drilling have risen. These high VSS levels negatively affect decoding performance. Additionally, extended-reach applications, which are now much more com- mon than previous- ly, experience high surface torque and drilling VSS that compromises MPT.
Strong variations in rigs, equipment, mud and piping lead to changing environments for the MPT system downhole as well as at surface. This situ- ation increases the complexity of the required system to overcome the difference in operating environments.
The reliability issues that often result from the chang- ing requirements and more challenging environments in which HSMPT must function have elevated required user interaction levels, frequently forcing feld engineers to redirect their focus from delivering answers to main- taining highly complex tools.
Finding a solution
Although HSMPT data rates of 10 bits per second (bps) or more have been recorded in the feld for about a decade, lack of reliability forced a thorough analysis of existing problems. The conclusion was that signifcant improvement can be achieved through the automation of manual processes and advanced signal processing.
The new HSMPT system applies automation in every feld operation to simplify operations, save time and elim- inate error-prone tasks such as manually reentering data. When a transmission parameter already is confgured in one system, this information is automatically distributed. Additionally, conditional data such as fow rate, depths and other information measured are gathered during feld operations and saved with the transmission parameters.
The simplifed HSMPT system consists of a downhole transmitter (the pulser), the mud channel and the receiver on the surface side, which usually has one or more pressure transducers. The main distortion sources for MPT data transmission are the mud channel and additional variable distortions. To reduce distortion and improve signal processing, special signal sequences automatically adjust adaptive flters. The pulser sends out the sequences regularly, enabling the surface system to tune the adaptive flters for changing channel con- ditions. The flter performance is tested and saved into a database with quality indicators, which enable feld personnel to optimize decoding quality through better decision-making (Figure 1). Enhanced signal process- ing algorithms on the surface signifcantly increase the success rate of the automated system and improve the decoding quality and reliability.
Successful feld performance
The new HSMPT system has enjoyed 100% success rates in many ultradeepwater drilling regions in a wide range of applications, all of which require a signifcant amount of real-time data to enable accurate decision-making. The technology has been used in more than 60 runs, with more than 5,000 circulating hours and more than 3,000 drilling hours. Physical data rates higher than 10 bps were reliably achieved while drilling in every job. The technology was deployed in both oil-based and water-based mud environments with measured depth of up to 8,000 m (26,247 ft). Different mud systems were used, with PV higher than 20 centipoise (cP) in 40 runs and higher than 40 cP in 10 runs.
Among successful applications of the new HSMPT sys- tem was its deployment in one of the longest and most sophisticated BHAs worldwide, in the North Sea. The system’s ability to reliably transmit more real-time data enabled the operator to deploy a BHA incorporating numerous drilling and LWD services to provide more answers in real time (Figure 2). The new system pro- vided up to 15 bps data rate in a challenging oil-based mud system with a PV of 34 cP. The drilled section, from 4,635 m to 6,611 m (15,207 ft to 21,690 ft) measured depth, was drilled in one run with 184 circulating hours.
Increasing HSMPT data rates and reliability means that the technology can now be run in complex drilling environments—including ultradeepwater wells and rigs with demanding mud conditions—that previously required significant manual effort and a potential fall- back to data rates below 10 bps. Automation and ease of use expand operating limits for HSMPT activities and reduce unnecessary workloads from technical support centers and field engineers. Allowing field service engineers to concentrate on delivering more answers to the operator improves efficiency and safety while drilling and reduces overall drilling cost.
未经允许,不得转载本站任何文章:
-
- Demons
-
石油圈认证作者
- 毕业于中国石油大学(北京),化学工程与技术硕士,长期聚焦国内外石油行业前沿技术装备信息,具有数十万字技术文献翻译经验。如需获取更多技术资料,请联系Demons(QQ2582825239;微信15810965891)