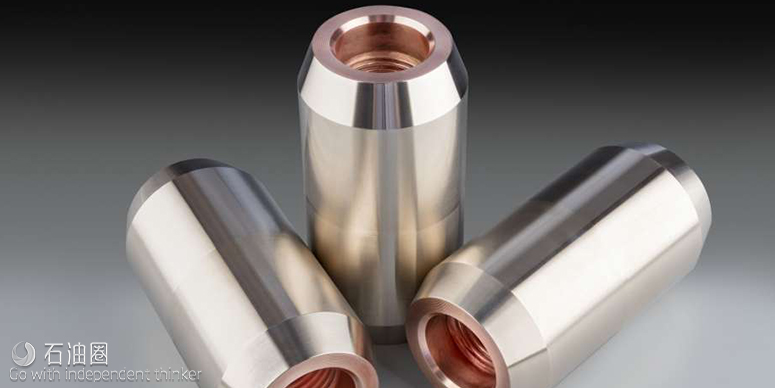
Materion公司推出的新型联轴器可大幅提高抽油杆采油作业的效率。
编译:惊蛰
在非常规深井开采中,若抽油杆在下冲程期间发生弯曲,抽油杆联轴器会与生产油管的内壁发生摩擦,这种弯曲与侧向载荷给有杆泵采油作业带来了巨大挑战。例如,某口井以每分钟六冲程抽油,每天循环8640次,抽油杆上任意一点相当于每天运动了23英里。如果能够消除抽油杆与生产油管之间存在的潜在接触风险,开发商将有机会来降低采油系统中的摩擦阻力与载荷,提高开采效率。纵观历史,油管泄露与联轴器故障几乎占到抽油机井故障的50%,而这些泄漏的根本原因往往是联轴器造成的油管磨损。
标准金属喷涂联轴器拥有硬镍涂层,可对钢制生产油管造成严重磨损。虽然标准T型联轴器没有涂层,也不像金属喷涂联轴器那么硬,但金属面之间的摩擦也会造成油管磨损。此外,T型联轴器也更容易腐蚀。为了减轻这些影响以及相关的油管磨损,Materion公司开发出一种新型低摩阻、高强度的铜合金。ToughMet合金是一种由铜、镍、锡制成的超耐用铜合金。该产品对钢制生产油管具备天然的抗磨损性,且拥有高冲击强度与更好的耐腐蚀性,可减少抽油杆上的整体摩阻。
最初,ToughMet抽油杆联轴器在斜井中证明了自己的优异性能,其有效率明显优于同类产品。Hess公司是Bakken地区最大的油气公司之一,将该联轴器应用到斜井段后,其平均故障间隔时间延长了两倍。因此,该公司决定将该联轴器纳入到其标准生产作业中。Discovery公司是一家油气公司,在Permian区块拥有1000多口井,由于抽油杆对管柱造成的磨损,其中一些大斜度井每隔60到90天就会出现故障。在引入ToughMet联轴器后,该公司表示某井连续作业了385天以上,没有发生任何故障。显而易见,通过使用这种降低摩阻与磨损的联轴器,开发商可避免频繁的修井作业,有效地提高生产效率。
目前已确认,使用这种新型联轴器不仅可以降低斜井的修井成本,而且可带来一系列意想不到的其它收获。除了降低油管故障率之外,八家不同的油气公司纷纷将目光投向了井动态状况的改善。现如今,这八家公司在11口井中全部应用ToughMet联轴器,以研究与量化通过减少井内摩阻,所获得的全部效益。将这些井在应用ToughMet联轴器前后(不进行其他设计变更)的动态数据进行对比分析,可以得到以下现象与预测:1、88%的井将实现原油产量的增加;2、93%的井将实现井下冲程的增加。
由于抽油杆的拉伸、收缩与偏转,井下冲程通常比地面测量的冲程短得多。降低抽油杆上的摩擦阻力,可以使抽油杆柱以更快速度、更平稳地移动,并转化为更长的井下冲程。获得更长的泵活塞冲程则可改善压缩效果,使油井的作业能力达到最大。
- 87%的油井将实现泵上方的液位下降。降低液位是必要的,这表明抽油效率很高。
- 81%的油井将实现泵充满度的提高。如果泵充满液体,作业将更有效,若能实现该目标,可降低电力消耗。
- 98%的油井将实现变速箱载荷的降低。变速箱载荷直接关系到有杆泵井作业所需的功率要求,变速箱驱动光杆,并提供扭矩,以转动平衡锤。
- 95%的油井将实现光杆峰值负荷的降低。光杆承受了下部所有抽油杆的重量、流体的重量以及设备往复运动时产生的惯性效应,抽油杆上的摩擦阻力增加了光杆上的负荷。
- 93%的油井将实现系统效率的提升。更高的系统效率意味着,油井可利用更少的功率来采出更多的流体,作业成本与该数值息息相关。
上述数据说明,ToughMet联轴器不仅可以减少油管磨损,而且还能减少抽油杆上的摩擦阻力。当抽油杆更加平稳地运动时,油井就能够避免井下冲程的缩短,从而更高效的采出液体。得益于更稳定的示功图以及更低的变速箱与光杆负荷,该联轴器可延长地面设备与抽油杆的使用寿命。减少摩擦阻力也将提高油井的作业效率,并降低作业相关的动力消耗。
迄今为止,在Bakken与Permian区块,已有28家开发商将ToughMet联轴器应用于900余口井。结果表明,除了降低设备故障率,避免昂贵的修井作业外,ToughMet联轴器对油井动态也具有显著影响。凭借优化的抽油杆运动、更长的井下冲程、更高的泵充满度、更高的流体产量,每口井的作业效率实现了大幅提升。此外,新型联轴器材料也降低了变速箱与光杆的负荷,从而延长了地面设备的使用寿命。
将标准T型或金属喷涂抽油杆联轴器更换为这种铜合金联轴器,可实现以下目标(平均):
- 原油产量平均增长21%;
- 井下冲程平均增加23%;
- 光杆峰值负荷平均下降16%;
- 光杆交变应力平均降低16%;
- 变速箱负荷平均下降16%;
- 泵上方的液位平均下降28%;
- 系统效率平均提高37%。
For English, Please click here (展开/收缩)
The deviation and side loading in deep, unconventional wells presents challenges for sucker rod pumping when rods flex during the down stroke of the pumping unit and sucker rod couplings wear into the inner wall of the production tubing. For example, a well pumping at six strokes per minute will cycle 8640 times per day and any given point on the sucker rod string can travel up to 23 miles per day. With so much potential contact between the sucker rod string and production tubing, there is plenty of opportunity to reduce frictional drag and loading on the system. Tubing leaks and coupling failures have historically accounted for nearly half of the failures in rod pump wells, with the root cause of these leaks frequently identified as coupling on tubing wear.
A standard spray metal coupling is abrasive to steel production tubing with its hard-nickel coating. While standard T couplings are not coated nor as hard as spray metal couplings, tubing wear occurs by a steel-on-steel galling mechanism. T couplings are also more susceptible to corrosion. In an effort to alleviate these effects and associated tubing wear, Materion developed a new low friction, high strength copper alloy. The ToughMet® alloy is a highly durable, spinodal bronze made of copper, nickel and tin. Naturally anti-galling to steel production tubing, it features high impact strength, offers improved corrosion resistance and can reduce overall friction on the sucker rod string.
ToughMet sucker rod couplings were initially successfully qualified in deviated wells with higher than average rates of failure. Hess, one of the largest producers in the Bakken, more than tripled its mean time between failures after introducing the couplings to deviated sections of their wells and went on to include the couplings in its standard production practice. Discovery Natural Resources LLC, an oil and gas company operating more than 1000 wells in the Permian Basin, owned some extremely deviated wells that were experiencing failures every 60 to 90 days, as a result of rod-on-tubing wear. After introducing ToughMet couplings, the company reported one well running for more than 385 days without failure. Clearly, these operators were able to eliminate frequent workovers and effectively improve their production efficiencies by utilizing a sucker rod coupling that actively mitigates coupling-on-tubing wear.
However, it has now been established that there is a range of unanticipated and significant added benefits of using the new couplings, beyond simply a reduction in workover costs for deviated wells. Identifying well performance benefits in addition to reduced tubing failures was of great interest to eight different operators. Between these eight different operators, 11 wells are currently running entire sucker rod strings of ToughMet couplings to investigate and quantify the full range of benefits observed by reducing frictional drag in the well. After analyzing their data, the following observations and predictions can be made on behalf of wells modified to run entire sucker rod strings of ToughMet couplings, where no other design alterations are made:
- 88% of wells will experience an increase in oil production.
- 93% of wells will experience increased downhole stroke.
Downhole stroke is usually much shorter than the stroke length measured at the surface because rods stretch, contract and deflect. Lowering frictional drag on the sucker rod string allows it to travel more smoothly and with more velocity, translating into greater downhole stroke. Capturing more pump stroke improves compression and allows the well to operate at maximum capacity.
- 87% of wells will experience decreased fluid level above the pump. Decreasing the fluid level is desirable and indicates efficient sucker rod pumping.
- 81% of wells will experience improved pump fillage. Operation is more efficient if the pump is filled with fluid. If so, lower electrical power usage will result.
- 98% of wells will experience gearbox load reduction. Loading on the gearbox is directly related to power requirements necessary to operate a well on rod pump. The gearbox drives the polished rod and provides the torque to rotate the counterweights.
- 95% of wells will experience peak polished rod load reduction. The polished rod holds the entire weight of the sucker rod string below, the weight of the fluid and the added inertial effects as the unit reciprocates. Frictional drag on the sucker rod string increases the load on the polished rod.
- 93% of wells will experience improved system efficiency. Higher system efficiency indicates the well is using less power for more fluid production and the costs of operation are directly related to this metric.
The data supports the hypothesis that ToughMet couplings not only reduce tubing wear, but also minimize frictional drag on the sucker rod string. When the sucker rod string can travel more smoothly, wells are able to capture lost downhole stroke and return more efficient fluid production. The couplings may serve to extend the life of surface equipment and sucker rods as indicated by smoother pump cards and reduced loads on the gearbox and polished rod. Minimizing frictional drag will also likely improve a well’s operating efficiency and offer power savings associated with it.
To date, 28 operators have installed ToughMet couplings in more than 900 wells between the Bakken and Permian Basin. The case studies demonstrate that, besides reducing failure rates and avoiding costly workovers, ToughMet couplings have a measureable effect on a well’s performance. Each well is operating more efficiently with improved sucker rod string movement, greater downhole stroke, increased pump fillage and accelerated fluid production. In addition, simply switching coupling materials has resulted in decreased loads on the gearbox and polished rod, which suggests that surface equipment life can also be extended.
Switching sucker rod couplings from standard T or spray metal to the copper alloy couplings achieved the following (on average):”
- Oil production increased 21% on average
- Downhole stroke increased 23% on average
- Pump fillage increased 9% on average
- Peak polished rod load decreased 16% on average
- Decreased alternating stress on the polished rod by 16% on average
- Gearbox loading decreased 16% on average
- Fluid level above the pump reduced by 28% on average
- System efficiency increased by 37% on average
未经允许,不得转载本站任何文章: