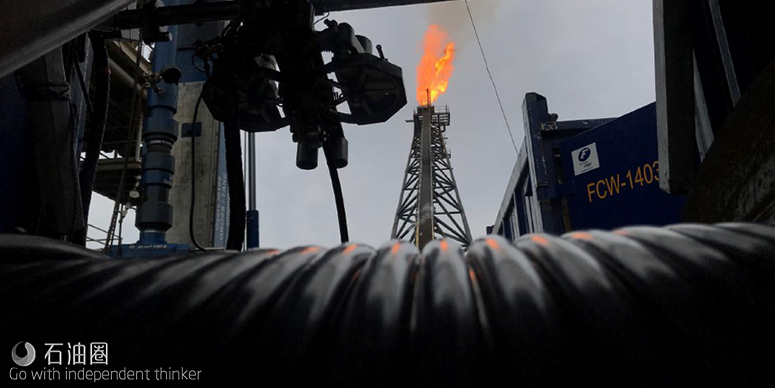
Expro公司推出的轻型连续油管作业灵活度更高,同时保持了高强度,在应用中为开发商解决了大问题。
编译:惊蛰
传统连续油管的一个优点是它能提供高排量循环,但是它体积大且笨重,部署起来很费时。连续油管作业可能会带来大量的装配与起重作业,带来高成本,同时需要很多的作业人员,存在潜在的HSE风险,占地面积大。
Expro公司的CoilHose轻型井循环系统通过使用小直径软管,成为连续油管与井下牵引器的替代方案,可最大限度地降低油气产量损失与修井成本。
该技术融合了连续油管与电缆的优点,利用软管取代了目前应用的传统钢管,彻底改变了连续油管行业。它开创性地将电缆的时效优势,与连续油管的泵送能力相结合。该系统的卷装占地面积相对较小,可提供无需钻机的轻量级循环服务,给予油气公司可快速部署的新选择。与海上和陆地的传统连续油管服务相比,节省了时间与成本。
系统优势
- 比传统连续油管更具经济性;
- 快速部署(3至4小时),人员需求更少;
- 更小的占地面积,移动与装配更灵活;
- 任何场地都可部署。
应用特点
- 比传统连续油管更具经济性;
- 更小的占地面积,更少的人员需求;
- 快速部署(3至4小时),人员需求更少;
- CoilHose装置也可以运行电缆与钢丝绳(一体式)。
案例分析:创新型修井技术降低成本
目标与背景:英国北海一家大型油气公司联系了Expro公司,因为其海底油田的产量持续下降。作业团队分析出该公司油井产量下降的原因有很多,包括:筛管腐蚀、筛管变形、地层坍塌与筛管堵塞。由于该井配置了井下压力计,不能排除储层压力下降的可能性。
经过分析,可能性最大的问题是筛管堵塞。返出的砂子很干净,但钻至储层的下部地层时,却发生了漏失。为解决该问题,作业中泵入了堵漏材料。在下筛管前,仅进行了最基本的循环洗井。作业人员认为,可能还残留一些堵漏材料,这可能会堵塞筛管,导致油井的产量随着时间的推移而下降。
因此,需要清洗筛管。这可以通过泵入清洗液,溶解造成堵塞的残留物来完成。开发商希望尽快恢复生产,但通常需要半潜式钻井平台上使用连续油管进行修井作业,所需的动员时间太长。这就催生了一种新方法。
Expro公司的卓越技术帮助该开发商实现了作业目标。Expro利用轻型修井船下入0.75寸的Coilhose,提供了定制化的解决方案。外径19.6毫米的CoilHose能够承受高达50000psi的内压,可将清洗液泵入至筛管,最大作业深度为9300英尺(2834米)。
这是全球首次在轻型修井船上,利用CoilHose进行无立管作业,其作业深度也创下了9300英尺的记录,远远超过迄今为止的最大深度2000英尺。
相比于以往应用的常规技术,客户所能获得的价值更高:比标准修井作业的成本降低了30%;1月份可利用修井船进行修井作业,若采用传统修井方法,由于天气恶劣,估计很难执行该作业。
For English, Please click here (展开/收缩)
One of the benefits of conventional coiled tubing is that it delivers high rate circulation but it can be heavy, bulky and time consuming to plan and mobilise. The process can involve significant rig-up and lifting, considerable costs, a high number of personnel, potential HSE exposure and a relatively heavy and large footprint.
Expro’s CoilHose Light Well Circulation System minimises the loss of hydrocarbon production and lowers the overall cost of intervention by providing an alternative to the use of coiled tubing and downhole tractors by using a small diameter hose.
It merges the best qualities of both coiled tubing and wireline and broadly changes the coil tubing industry by substituting hose for the conventional steel pipe currently used. It uniquely integrates the benefits of wireline and time efficiency with coiled tubing pumping capabilities. The system enables rigless light circulation services from a package with a relatively small footprint and offers oil and gas operators an alternative that can be rapidly deployed, saving both time and costs compared to the traditional coiled tubing services both onshore and offshore.
System benefits
- More cost effective than traditional coiled tubing
- Rapid deployment (3-4 hours) and lower personnel requirements
- Smaller footprint with mobile and flexible set-up
- Can be deployed almost universally
Benefits
- Cost effective compared to traditional coiled tubing
- Smaller footprint and lower personnel requirements
- Rapid deployment (3-4 hours) and lower personnel requirements
- CoilHose unit can also run Wireline and Slickline (all in one)
Case study: Expro delivers an innovative approach to well intervention
Objectives and background
- Expro was contacted by a significant producer on a subsea field in the UK North Sea, who had a decline in production
- The subsurface team had a number of reasons for the decline in production of their well including eroded screens, collapsed screens, formation collapse and screen plugging. As the well had a downhole gauge, reservoir pressure decline could not be ruled out
- The most likely problem appeared to be screen plugging. The sand was very clean, but they experienced losses when drilling into the formation just below the reservoir sand. This was remedied by pumping LCM and the clean up before running the screens was also very basic. It was considered likely that some plugging material was remaining, and that this could plug the screens giving a production decline over time
- The sand screens needed to be cleaned, and this could be done by pumping a cleaning fluid across them to dissolve the residue that was blocking them. They wanted the production back quickly, but the normal method of using a semisubmersible drilling rig with coiled tubing to carry out this intervention work was going to take too long to mobilise. This resulted in a new approach
Expro Excellence
- Expro delivered a bespoke solution to the client’s problems by running the ¾” Coilhose from a Light Well Intervention Vessel. The 19,5mm OD CoilHose is capable of withstanding 50.000psi internal pressure and was used to place the cleaning fluid across the screens at a max depth of 9300 ft (2834mtr)
- A world first in utilising the CoilHose in a riserless operation from a LWIV, and also a record depth of 9300 ft, far exceeding the 2000 ft that was the max depth to that date
Value to the client
- Intervention was performed at around 30% reduction of the standard cost
- Intervention performed from a vessel in January, which could have been a problem due to rough weather if utilising traditional methods of intervention
未经允许,不得转载本站任何文章: