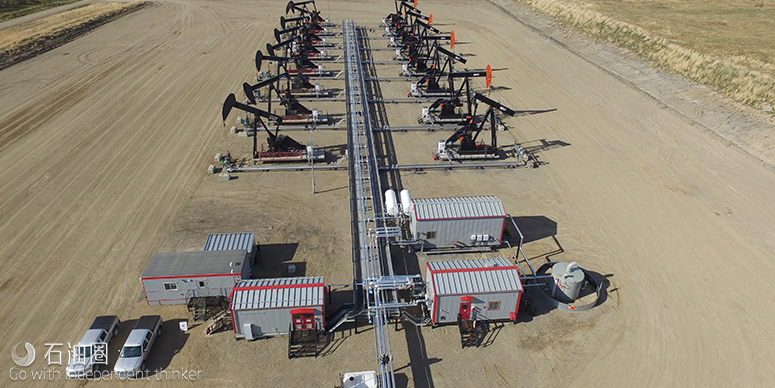
有效的分析可以帮助优化油气设备性能,并准确预测故障!
编译 | 惊蛰
如今,石油和天然气行业也像其他许多行业一样,逐渐开始采用数据驱动的思维模式,是什么推动了这种转变呢?
油气价格的下滑给开发商带来了巨大压力,他们尽了最大努力削减成本,并最大限度地利用现有老化资产。但是,当前开采作业操作比以往任何时候都复杂,当操作人员无法回答有关设备完整性和应用性能的关键问题时,优化油气设备运转就是一项不可能完成的任务。例如:我们是否准备好应对持续的市场变化?为什么油气设备会失效?设备的失效频率如何?
为了充分实现数字油田的价值,油气开发商正在寻求实施新的物联网(IoT)技术,并将设备、设施和系统连接,整合数据。但最关键的是,开发商需要将所有数据转化为油气开采运营的智能方案。
分析工作涉及多个来源的大量数据,一般首先将数据收集并将其转化为有用信息,然后以利用价值更高、操作可行性更强的形式将这些信息呈现给操作人员。
要实现这一目标,需要在开发油田中实现无缝数据连接与分析。实际操作中,分析的最基本工作是为数据提供背景和性能预测,这其中包括来自人工举升系统的井行为和性能趋势,还包括来自地面处理滑橇、远程井口监测系统、井下、油藏的实时性能数据。此外,分析还可以帮助开发商调查设备与开采异常情况并解决相应问题。
油气开发商要实现分析技术的高效应用,首先需要了解分析的几个层次,以及各自的复杂程度和优势。
描述性和诊断性分析是油气开发商的起点。在最基本的层面上,这些数据可以通知作业人员作业的执行情况以及设备的运营条件。如果发生故障,此类分析可以帮助技术人员快速诊断运转问题,帮助将适合的工作人员派遣至对应的地方,并使用合理的工具来解决问题。
预测分析是当今许多开发商的目标。通过这些分析,开发商可以查找数据中的已知条件和关系,在其基础上可以表明设备状况或设备即将发生故障,进而及时解决。开发商可以使用预测分析来识别故障早期痕迹,防止发生恶劣问题,或者为即将发生的设备故障提前完成操作和维护准备工作,从而为减少代价高昂的停机时间。
从某个角度来讲,预测分析并不是绝对的。在某些情况下,它们是根据各种特定故障的概率而配置的。例如,生产团队可以将失败概率阈值设置为80%。如果分析软件在此阈值附近检测到故障,则将触发警报,并且通知开发商故障即将发生且需要维护服务。
规范分析是最复杂的设备维护分析技术,也是大多数石油和天然气开发商的最终目标。该分析方法建立在预测分析的基础上,不仅可以预测设备故障,还可以根据历史故障数据和趋势推荐纠正措施。工作人员可以使用分析系统建议的操作来纠正运营问题,并实时优化设备性能。当与增强现实等技术配合使用时,操作或维护人员可以通过数字指令进行操作,以修复故障设备或更改操作参数,改善油气开采过程性能。
在最高级别的分析中,开发商可以在单个仪表板上查看整个操作过程。这可以提供实时、动态的KPI与目标,列出实现业务目标所需操作的优先级列表。此外,还可以将设备的当前性能与历史数据进行比较。作业人员可深入了解每个井场,查看井场性能,并进一步根据泵设备性能进行钻井作业。
例如,螺杆泵控制分析可以根据井下信息来获得井下状况,并确定设备是否以最佳方式运行,是否需要干预作业。柱塞分析从现场收集数据,并显示设备性能变化的时间线,这会直接影响关键决策的制定,例如是否应增加作业压力。气举分析可以帮助操作人员了解是否注入气体过量,并确定适当的油气注入比例。
在加拿大西部油藏中,ARC Resources拥有多个勘探项目,进行常规石油和天然气的开发和生产。在其中规模最大的井场之一,该公司希望优化控制操作,并获取有价值的生产信息,以支持关键决策制定,排除设备故障,提高作业效率。
该公司的优化团队使用了罗克韦尔自动化ConnectedProduction解决方案,成功减弱了蜡的积聚,并减少了井中化学品注入。
通过作业背景信息分析,该解决方案帮助ARC Resources获得了生产预见性,从而简化了设备的故障排除流程。利用该系统的分析结果,开发商可以优化整个油井的生命周期,更好地应对潜在的系统和设备问题。自实施分析以来,ARC Resources每口井每年的运营成本都降低了约3万美元。随后,该公司计划将其作为优化战略的关键部分。
通过进行油田环境分析,可以帮助开发商跟踪设备性能趋势变化,快速识别和响应影响开采、设备正常运行时间的事件,并主动采取措施防止停机问题发生,减少开发商的生产损失。当这些分析工作与业务系统相结合时,开发商可以根据市场变化和业务需求快速调整生产。
相比于以往,分析工作部署从未如此简单。开发商所需要的分析工作基础已经建立,新技术可以将数据的强大潜能直接交付给工作人员,并为他们提供有效背景分析。
For English, Please click here (展开/收缩)
Analytics can help optimize oil and gas equipment performance and predict failures
Today, the oil and gas industry, like many others, is embracing a data-driven mindset – what’s driving the shift?
The downturn in oil and gas prices put pressure on producers to cut costs and maximize use of their existing, aging operating assets. But with operations more complex than ever, optimizing oil and gas equipment can be an impossible task when you are unable to answer critical questions about health and performance, such as: Are we prepared to react to ongoing market changes? Why did a piece of equipment fail? How long until it fails again?
Hoping to capitalize on the promise of the digital oilfield, oil and gas producers are seeking to implement new IoT technologies, and connect their equipment, devices and systems, and integrate their data. Most critically though, producers are looking for ways to transform all that data into operational intelligence.
Analytics involve monitoring large amounts of data from multiple sources, collecting and contextualizing that data into information, and then presenting that information to your workers in the form of useful, actionable insights.
This requires seamless connectivity across your oilfield. The most basic job of analytics is to provide context to data. This could include well behavior and performance trends from artificial lift systems or can also include real-time performance from surface processing skids, remote wellhead-monitoring systems or insights into downhole and reservoir conditions. Furthermore, analytics can help users investigate anomalies and troubleshoot issues.
Oil and gas companies that want to create a roadmap for deploying analytics should first understand the four analytics categories, as well as their complexities and benefits.
- Descriptive and diagnostic analytics are the starting point for oil and gas producers. At the most basic level, this data informs workers how things are performing and the conditions in which they’re operating. If a failure occurs, these analytics can help technicians quickly diagnose the problem, and help make sure they send the right person to the right place, with the right tools to resolve the problem.
- Predictive analytics are the target goal for many producers today. These analytics look for known conditions and relationships within the data that indicate a device or piece of equipment is approaching failure. Producers can use this to identify and prevent equipment failures before they happen or prepare operations and maintenance for an impending equipment failure, providing a tremendous opportunity to reduce costly downtime. Note: predictive analytics won’t always be absolute. Sometimes, they are configured around the probability of various failures. For example, a production team could set a threshold for a failure probability of 80 percent. If the software detects a failure probability at this threshold, it will trigger an alarm condition and can notify users that a failure is impending and requires service.
- Prescriptive analytics are the most complex analytical techniques for equipment maintenance and the ultimate goal for most oil and gas producers. Prescriptive analytics build upon predictive analytics to not only anticipate equipment failure, but also recommend corrective action based on historical failure data and trends. Workers can use the recommended actions to correct issues and optimize performance of assets in real-time. When paired with techniques like augmented reality, operators or maintenance personnel can be guided through a set of digital instructions to repair a failed piece of equipment or change operational parameters to improve process performance.
At the highest analytics level, users can view their entire operations on a single dashboard. This provides real-time, dynamic KPI’s versus targets, and a prioritized list of required actions to meet business goals. In addition, current performance can be compared to past performance. Operators can drill deep into each site, viewing well-pad performance, and drilling even further into a well or pump’s performance.
Rod-pump control analytics, for example, can use downhole card information to provide insights into the downhole conditions and identify if equipment is running optimally and if intervention is required. Plunger-lift analytics are retrieved from the field and displayed as a timeline of well-performance indication and influence key operator decisions, such as if pressure should be increased. Gas-lift analytics can help operators to know if they’re over injecting gas and identify the proper ratio of oil and gas injection.
In the vast oil reserves of Western Canada, ARC Resources has multiple assets deployed for the exploration, development and production of conventional oil and natural gas. At one of their large multi-well pad sites, the company wanted to optimize control operations and gain access to valuable production information to support business decision-making and equipment troubleshooting.
The company’s optimization team deployed a Rockwell Automation ConnectedProduction solution using analytics software to mitigate wax build up and reduce chemical injection on their wells.
The analytics solution helped ARC Resources gain production visibility with contextualized information for simplified equipment troubleshooting. The system helps guide operators through the entire well optimization lifecycle and helps operators better respond to potential system and equipment issues. Since implementing analytics, ARC Resources has reduced operational costs by approximately $30k a year per well, and plans to include this as a key part of their optimization strategy.
Tap into the Potential of the Digital Oilfield
Analytics in a connected oilfield environment can help you track performance trends, quickly identify and react to events affecting production and equipment uptime, and proactively take actions to prevent downtime and lost production. When these analytics are combined with business systems, producers can quickly adjust production in response to market changes and business needs.
It has never been easier to deploy analytics. The foundation you need in place is well established and new technologies can put the power of your data directly into the hands of the workers who need it and contextualize it for them.
未经允许,不得转载本站任何文章: