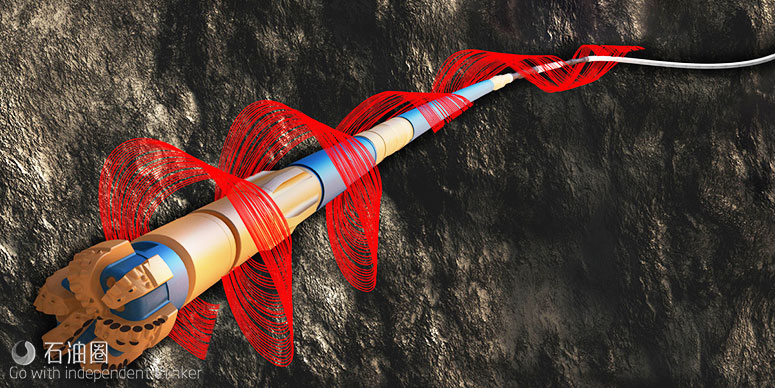
在北美页岩区块,有多种解决方案可供作业公司选择来提高业绩,但最好的方法之一是使用井下数据进行钻井优化。
来自 | E&P
编译 | 白小明 影子
即使油价持续缓慢复苏,行业仍然需要提高钻井效率,特别是在非常规页岩油气开发过程中,建井的经济性已经帮助企业实现了盈利。在北美页岩区块,有多种解决方案可供作业公司选择来提高业绩,但最好的方法之一是使用井下数据进行钻井优化。国民油井华高公司(NOV)一直在使用一项优化服务,收集和分析来自存储式BlackBox测井工具的高质量井下数据,提高北美页岩及其他地方的钻井效率。
BlackBox工具使用传感器获取井下事件和参数数据,如钻井时的粘滑效应、压力、钻压传递、横向振动和反扭矩。根据操作人员的需要,工具可以安装在近钻头短节、钻头、底部钻具组合(BHA)和/或钻柱内。钻井动力学工程师利用工具在井下记录的数据进行工作后分析。这种方法让工程师也获得了地面数据,当把地面数据与获得的井下数据相结合时,可以全面了解井下发生的情况。根据这些信息,操作人员通常可以确定钻井操作、BHA和钻柱配置如何影响其作业性能和可靠性。
将地面和井下数据相结合的综合性方法,使操作人员能够更有效地为BHA选择组件,并更好地设计整个BHA。工作人员利用NOV的专有算法运行作业数据,可以识别有害振动,同时评估地层岩性特征,可向钻井人员提示任何给定井段可能存在的潜在风险。工作人员还可通过测量额外的动态行为(如扭矩和摩阻、机械比能和螺旋屈曲)来强化分析,从而加深对井下钻井环境的全面了解。实时远程监控通过全天候24小时提供专业技术支持和更新钻机工况,完善了服务的价值。
二叠纪盆地案例研究
一家二叠纪盆地的独立作业公司找到NOV,希望使其钻井效率尽可能保持最佳。公司决定在3口井下入BlackBox设备,以确定这些井是否取得了最大钻井效率和ROP,同时确定降低钻井性能的不利因素。NOV发现邻井整个钻柱的粘滑效应是重点问题,因此他们推荐使用一款防粘滑软件SoftSpeed II来解决问题,它利用自动减振功能来减小扭向振动和粘滑振动。
作业公司使用该软件后,获得了巨大的效益,他们仅使用两只12 1/4-in钻头就钻完了余下井段。与邻井的4只钻头相比,节省了2趟钻,而且之前最好的井也用了3只钻头。此外,从新井起出的钻头仍处于良好状态,而以前老井起出的钻头已损坏。尽管作业公司以前就认为他们获得了最佳的ROP,但在使用推荐的软件分析BlackBox数据后,他们决定调整钻井参数,从而使钻井效率有了大幅提高。邻井用88.5 h(小时,下同)纯钻时间钻完1,504 m井段,ROP为17 m/h(单位米/小时,下同),而新井使用调整后的参数,钻1,773 m井段仅使用约52.5 h,ROP为33.8 m/h。新钻井参数为作业公司节省了36 h纯钻时间,相比邻井ROP提高了98%。
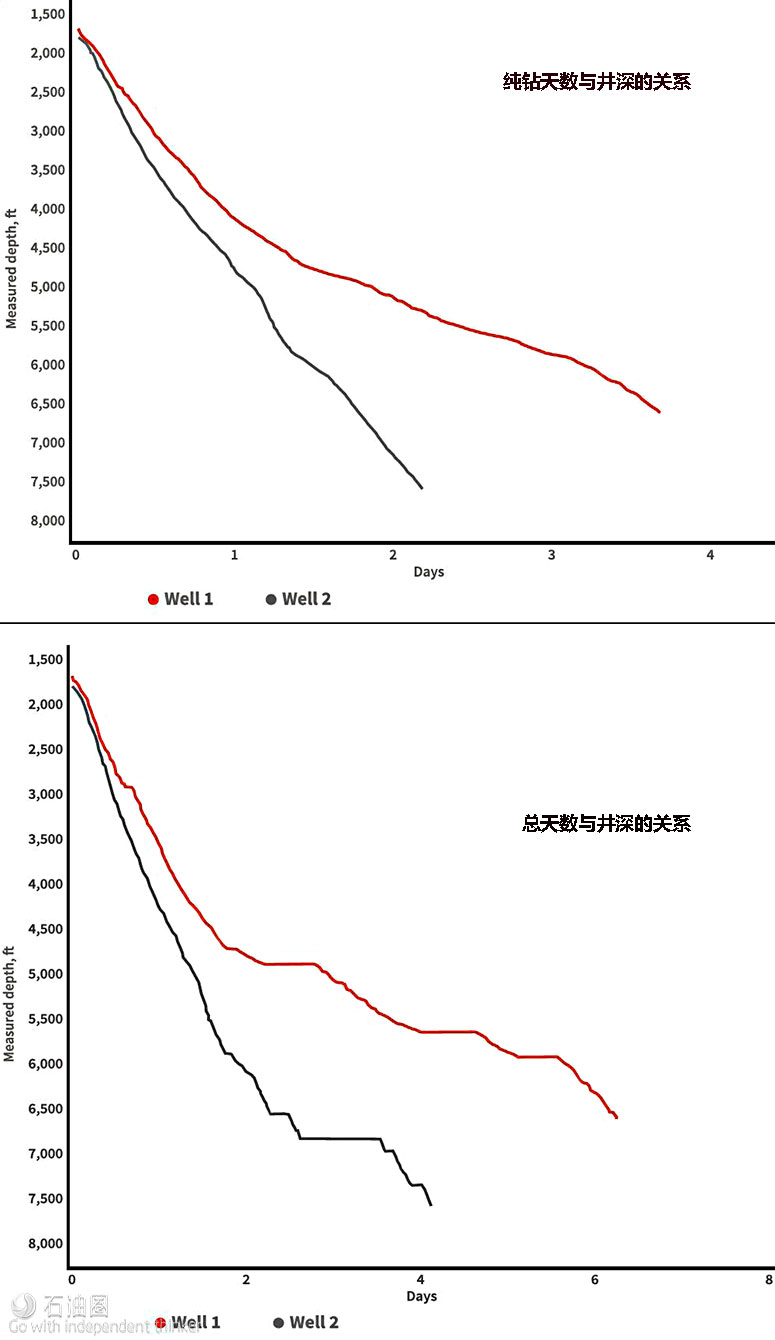
这些图分别显示了纯钻天数和总天数与井深的关系,纯钻时间显示了提高ROP带来的效益,总时间显示了节省2趟钻带来的效益。(来源:NOV)
俄克拉荷马州案例研究
一家俄克拉荷马州的独立作业公司在几口页岩井中遇到了扭转振动问题,钻头处的能量损失降低了ROP,而且钻完该井段需要花费很长时间。公司最初决定使用SoftSpeed II软件来减小或消除振动,他们在3口井的12 1/4-in井段下入了系统尝试提高ROP和钻井效率。在公司的邻井中,振动造成ROP降低导致钻井周期延迟成本高昂,作业公司使用158 h才钻完2,498 m井段。使用SoftSpeed II系统后,他们在100 h内就钻完了长于2,549 m的井段。ROP从约15.5 m/h提高到25 m/h。
在其中一口井,公司决定下入BlackBox工具来记录钻头的扭转振动情况,以验证SoftSpeed II系统能够降低振动,能够使能量更高效地从顶驱传递到钻头。BlackBox工具记录的井下转速与SoftSpeed II系统计算的估计BHA转速非常接近,验证了系统模型的正确性。当感应到粘滑效应时,在地面可以看到很大的扭矩波动,BlackBox工具收集的井下数据证实井下转速波动很大。当SoftSpeed II服务被激活后,地面转速波动平衡了沿钻柱向上传递的扭转能量,从而阻止了能量的反射,这种能量可能是造成粘滑的动力。
最终,地面扭矩波动和井下转速波动几乎立即减小。通过BlackBox工具获得的钻井数据,帮助NOV向作业公司证实SoftSpeed II服务确实减轻了钻头的扭转振动,并使钻头可以工作更长的时间再起出。BlackBox数据已被用于识别限制性能的因素,并在其他几个项目中验证了其他NOV技术的解决方案,包括Fluid Hammer提效钻井工具。
结论
随着钻井作业量的增加,页岩项目将继续变得更加重要,与此同时,页岩项目需要持续关注作业效率的提高。针对每家作业公司的独特需求而量身定制的钻井软件和优化服务,可以确保解决方案经济高效地解决特定挑战。未来钻井公司将拥有更智能的井下数据,帮助他们持续优化BHA设计和钻井设计,继而推动行业不断发展。
您也有让人挠头的难题需要解决,或是优质技术想要找应用市场吗?如果有的话,欢迎联系小编微信或邮箱,也许能找到一剂良药。
二丫:022-65771089;zhanglingyu@cnoocraiborn.com
For English, Please click here (展开/收缩)
Even as oil pricing continues its slow recovery, the need remains for improved drilling efficiency, particularly in unconventional shale developments in which well economics have now made profitability a reality. Operators looking to drive performance improvements in North American shale plays have a variety of solutions to choose from, but one of the best methods is drilling optimization using downhole data. National Oilwell Varco (NOV) has been using an optimization service—built around collecting and analyzing high-quality downhole data from BlackBox memory mode logging tools—to enable more efficient drilling in North American shale and beyond.
BlackBox tools use sensors to capture data on downhole events and parameters such as stick/slip, pressure, weight transfer, lateral vibration and torque reactions while drilling. The tool can be placed in a near-bit carrier sub, drillbit, bottomhole assembly (BHA) and/ or drillstring depending on the needs of the operator running the tool. The tool records data while downhole for post-run analysis by a drilling dynamics engineer. The benefit of this method is the engineer also has acquired surface data that—when combined with the downhole data obtained during the run—provide a comprehensive overview of what is occurring downhole. From this information, the operator can typically determine how drilling practices, BHA and drillstring configurations are affecting performance and reliability in its operation.
The integrated approach of bringing together surface and downhole data allows operators to more effectively choose components for their BHA and to design the full assembly better. Running the obtained post-run data through NOV’s proprietary algorithms identifies harmful vibration while evaluating the unique characteristics of formation lithology, which reveals to the driller that there could be a potential risk of dysfunction in any given section. This analysis is bolstered by measuring additional dynamic behaviors—such as torque and drag, mechanical- specific energy and helical buckling—to drive total understanding of the downhole drilling environment. Real-time remote monitoring rounds out the value of the service offering by providing technical expertise and updated rig conditions 24/7.
Permian Basin case study
NOV was approached by an independent operator working in the Permian Basin that wanted to verify it was drilling as efficiently as possible. The operator decided to run BlackBox units downhole on three wells to determine if the wells were, in fact, achieving maximum efficiency and ROP while identifying any performance-reducing drilling dysfunctions. NOV identified full-string stick/slip as an area of concern in the offset wells, leading to the recommendation of SoftSpeed II—a stick/slip prevention software that uses automated vibration dampening to mitigate torsional vibration and reduce stick/slip oscillations—to address the problem.
Implementing the software provided a major benefit to the operator, which drilled the next section using only two 12?-in. bits. This saved the operator two bit trips, as the previous offset well had been completed with four bits, and even the best record for other wells was three bits. Also, the bit pulled from the new well was still in excellent condition, while bits from previous wells had been damaged. Despite the operator’s belief it had maximized ROP, implementing the recommended software and drilling parameter adjustments—determined after analyzing the BlackBox data—enabled a dramatic increase in efficiency. The offset well had been drilled to 1,504 m (4,935 ft) at an on-bottom ROP of 17 m/hr (56 ft/hr) in about 88.5 hours. Meanwhile, the new well—using the new parameters— was drilled for 1,773 m (5,817 ft) at an on-bottom ROP of 33.8 m/hr (111 ft/hr) in about 52.5 hours. The improvements saved the operator 36 on-bottom hours and increased ROP over the offset well by 98%.
Oklahoma case study
An independent operator in Oklahoma was experiencing torsional vibration in several shale wells, with energy loss at the bit leading to reductions in ROP and section intervals taking too long to drill. The operator initially decided to use the SoftSpeed II software to reduce or eliminate vibration, deploying the system in three 12?-in. sections of its well to try to increase ROP and drilling efficiency. In the operator’s offset wells, vibration-induced ROP reductions led to costly delays in drilling time, with the operator drilling 2,498 m (8,196 ft) in 158 hours. While using the SoftSpeed II system, the operator was able to drill a longer interval of 2,549 m (8,365 ft) in 100 hours. ROP was improved from about 15.5 m/hr (51 ft/hr) to 25 m/hr (82 ft/hr) in this application, an increase of 61%.
In a unique application, the operator decided to run BlackBox tools to record torsional vibration levels at the bit to validate that the SoftSpeed II system was responsible for decreasing vibration levels and allowing a more efficient transfer of energy from the top drive to the bit. The downhole rpm recorded by the BlackBox tools closely matched the estimated BHA speed calculated by the SoftSpeed II system, validating the system’s model. When stick/slip was induced, heavy torque fluctuation was seen at the surface, with downhole data collected by the BlackBox tools confirming downhole rpm was fluctuating heavily. When the SoftSpeed II service was activated, the surface rpm fluctuations counteracted the torsional energy being transmitted up the drillstring, preventing the reflection of that energy—which would have been a driving force in causing stick/slip.
The result was a near-immediate decrease in both surface torque fl uctuation and downhole rpm fluctuation. The drilling records acquired by the BlackBox tools allowed NOV to confi rm for the operator that the SoftSpeed II service was indeed mitigating torsional vibration at the bit and enabling the rig to drill ahead for longer before pulling a bit. BlackBox data have been used to identify performance limiters and validate solutions in several other projects for other NOV technologies, including the FluidHammer performance drilling tool.
Conclusion
Shale projects will only continue to grow in importance as drilling activity rebounds, and the need for greater operational efficiencies in shale plays will remain a focus. Using drilling software and optimization services tailored to the unique needs of each operator ensures the solution cost-effectively addresses their specific challenges. Drillers in the future will be armed with more intelligent downhole data that enable continual improvement in BHA design and well planning, helping the industry to continue advancing.
未经允许,不得转载本站任何文章: