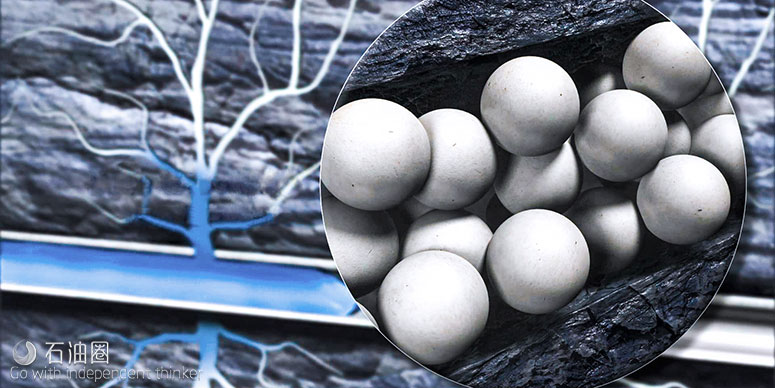
随着作业公司寻求经济高效的增产措施,新技术亦旨在降低维护成本,减少对环境的影响。
来自 | DC
编译 | 白小明 影子
对油气行业而言,减少非生产时间(NPT)和增加非常规油气产量的目标正在推动水力压裂技术的发展。特别是随着作业公司非常规油气产量开始达到自然物理极限,优化压裂工艺的需求变得更加旺盛,EvercoreISI的石油服务、设备和钻井高级总经理James West如是说。优化过程因区块而异,但总体而言,各公司正在寻求更好的井眼和裂缝布局,以及压裂簇的筛选和分段。
处理产出水
支撑剂供应商Fairmount Santrol认为,行业对压裂技术的要求,不仅要能够提高产量,而且要更低的前期投资,更易于部署应用、更环保。
Fairmount Santrol公司自悬浮砂产品经理Sid Banerjee表示,他很高兴应用公司的自悬浮砂生产线Propel SSP来减少压裂作业中的淡水用量。Propel SSP 350可以使用总溶解固体含量高达350,000 ppm的水。该产品于2017年1月首次推出,公司还在继续修改以应用于不同的场合,包括重复压裂。
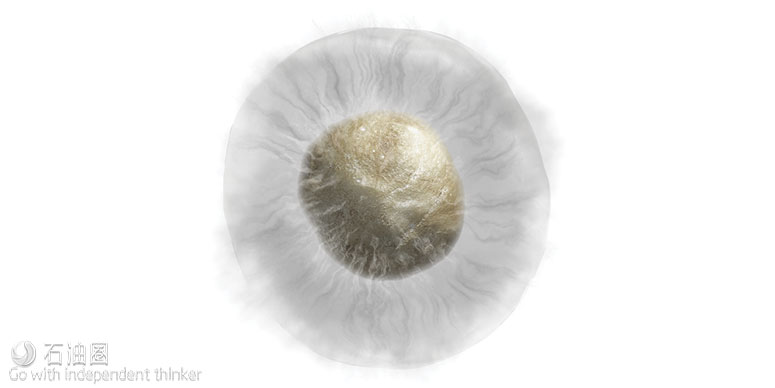
Fairmount Santrol公司的Propel SSP 350可以减少水力压裂作业中的淡水用量。
Banerjee说,“污水是北美水力压裂最大的液体废弃物之一,压裂使用的水必须相对清洁,这使得油气行业与农、牧业、城市和其他消费淡水的实体互相竞争。一些地区的水资源短缺加剧了人们对现有水供应的担忧。”
在未来的技术开发方面,随着E&P公司寻求以尽可能低的成本提高产量,Fairmount Santrol正在研究井筒重复压裂技术。对于一口产量表现不佳的井或老井,可以仅用十分之一的钻新井成本,提高或增加产量。如果井筒问题得到解决,那么重复压裂一口老井可以获得客观的回报。但是,时间紧迫的公司通常会选择在一个新区域,采用他们可以理解的设计钻一口新井,而不是对老井进行重新设计。Banerjee称,“大家对这个领域有相当大的兴趣,但没有太多人了解怎样的一口井才是良好的重复压裂备选井。”
优化支撑剂分布
CARBO全球工程总监Terry Palisch表示,油气行业虽然还在关注最大化开采一个油藏所需支撑剂数量的问题,但现在行业应该聚焦于非常规油气井的长期生产能力。在这种削减成本仍是主流的大环境下,公司看到其客户大规模转向使用压裂砂产品。然而,这种转变带来了与将大量压裂砂(约9000~14000吨的砂子)泵入井内相关的可持续性和物流问题。例如,在某些地区缺乏高质量的砂,只能在压裂改造中使用化学材料。而返排水的处理、运输砂所需的火车和卡车数量,也给行业带来了挑战。
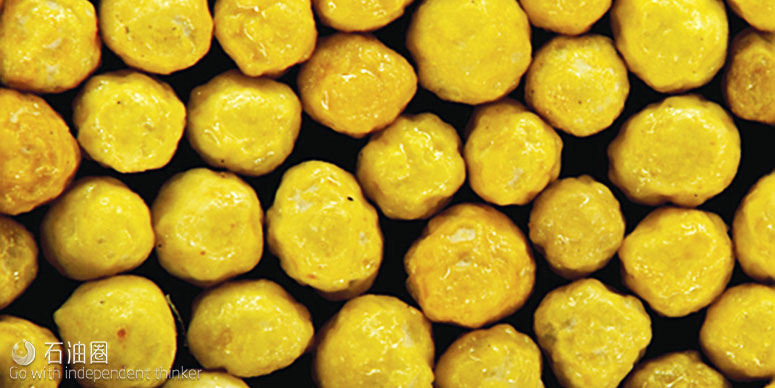
CARBO Ceramics公司认为,用低密度陶瓷支撑剂CARBOAIR代替砂,可以使用更少的水将支撑剂输送到井内地层更深处。
公司认为,通过用低密度陶瓷支撑剂CARBOAIR代替砂,可以用比常规方法少25~30%的水将支撑剂泵送得更远,从而减少压裂作业对环境的影响。新支撑剂已于去年发布,并进行了2次初步的现场试验;Palisch称,今年早些时候也已进行了另一次的现场试验。CARBOAIR是一种超低密度陶瓷支撑剂,具有采用化学方法设计的孔隙度和2.0的比重,与砂相比,沉降速率降低了30 – 40%。据CARBO称,与传统支撑剂相比,该技术减少了保持裂缝张开所需的支撑剂数量,减少了水的消耗量和返排液的处理成本。
2017年初,在新墨西哥州的Eddy县,一家作业公司对一口位于Bone Springs地层薄油产层中的初探井进行了压裂改造作业,通过将低密度支撑剂作为尾部流体泵入井内以获得更大的支撑压裂半长。作业公司总共进行了26段压裂,泵送了1134~1360 t的CARBOAIR(相当于每级45吨),以获得与40/70的常规砂相当的效果。最终,根据CARBO的研究,该井的产量递减速率低于附近的其他井。
在另一个案例研究中,一家Eagle Ford的作业公司计划钻2口相邻的平行水平井。在一口井中,用40/70目的CARBOAIR代替每级最后20%的100目和40/70砂支撑剂。据公司称,最终该井的产量提高了20%。
为了帮助油气公司了解支撑剂在地下的流动路径,CARBO一直在努力开发不仅仅用于保持裂缝张开的支撑剂。公司计划在2018年下半年将其新产品QUANTUM商业化,该产品使操作人员能够探测到地下数百米以外的支撑剂。
目前,可用的探测支撑剂的技术,可以使用下入井内的中子测井或伽马测井观察到含有放射性或非放射性示踪剂的特种支撑剂。然而,这种技术只能探测到井筒周围18~24-in内的支撑剂。Palisch解释说,这主要是通过向井内下入测井工具来探测支撑剂,基本可以在任何储层深度进行。
QUANTUM技术可以观察到据井眼数百米的导电支撑剂或带有金属涂层的标准支撑剂。Palisch表示,“到目前为止,虽然我们不知道探测的极限范围,但目前能够探测到的支撑剂的深度已达到了3000m,这是通过安装在地面井口附近的传感器测得的。”
该技术使用了电磁方法、地面电磁场传感器以及一种专门配制的支撑剂,已在西德克萨斯州、Marcellus和STACK区块进行了现场试验。Palis表示,CARBO目前正在进行第5次,也是该产品的最后一次现场试验。
您也有让人挠头的难题需要解决,或是优质技术想要找应用市场吗?如果有的话,欢迎联系小编微信或邮箱,也许能找到一剂良药。
二丫:022-65771089;131-3255-0596
For English, Please click here (展开/收缩)
Still struggling to understand how much proppant is enough to optimally deplete or drain a reservoir, the oil and gas industry now must focus on the long-term productivity of unconventional wells, Terry Palisch, Global Engineering Director for CARBO, said. With cost-cutting still king in this environment, the company saw a massive shift among its customers toward sand-based products. However, this shift raises questions around the sustainability and logistics of putting 20 million to 30 million pounds of sand in a well. For example, there are challenges around the shortage of sufficient-quality sand in some areas and the use of chemicals used in frac treatment. The disposal of flowback water also poses challenges, as do the number of trains and trucks required to transport sand to worksites.
By substituting sand volume with a low-density ceramic proppant, CARBOAIR, the company believes that operators can transport proppants further in the wellbore with 25% to 30% less water than typically used, reducing a fracking operation’s environmental footprint. The release of the new proppant began last year with two initial field trials; it has also been deployed in another field trial earlier this year, Mr Palisch said. CARBOAIR is an ultra-low density ceramic proppant with chemically engineered internal porosity and 2.0 specific gravity that offers 30% to 40% slower settling rates compared with sand. According to CARBO, the technology reduces the amount of proppant needed to keep fractures open versus conventional proppant, reducing water consumption and flowback treatment costs.
In early 2017 in Eddy County, New Mexico, an operator was able to stimulate a wildcat well with thin gross pay in the second Bone Springs formation by pumping in the low-density proppant as a tail-in to promote greater propped frac half-length. A total of 26 frac stages were pumped using a smaller amount by weight of CARBOAIR – 2.5 million to 3 million lb total, or around 100,000 lb per stage – to achieve the equivalent volume as 40/70 conventional sand. As a result, the well experienced a shallower production decline than other nearby wells, according to the CARBO study.
In another case study, an Eagle Ford operator had planned to drill two parallel offset horizontal wells. In one well, 20% of the final proppant in each stage – 100 mesh and 40/70 sand – was replaced with 40/70 mesh CARBOAIR. As a result, a 20% productivity increase was seen in the well, according to the company.
To help oil and gas companies understand where proppants are flowing in the subsurface, CARBO has been working to develop proppants that do more than just prop open the fracture. It plans to commercialize in the second half of 2018 its new product, QUANTUM, which allows an operator to detect proppants in the subsurface from hundreds of feet away.
Technology currently available for detecting proppants can see specialty proppant that contains either radioactive or non-radioactive-based tracers using gamma ray or neutron logs run in the wellbore. However, such technology can only detect the proppant location within 18 to 24 in. of the wellbore. It is measured using a log run in the wellbore, and this can be done basically at any depth reservoir, Mr Palisch explained.
The QUANTUM technology is meant to see electrically conductive proppant – or standard proppant with a metal coating – from hundreds of feet away from the wellbore. “To date, the proppant has been at depths up to 10,000 ft, although we do not know what the limit will be. It is measured using sensors located on the surface around the wellhead and pad,” Mr Palisch said.
Using electromagnetic methods, surface electric and magnetic field sensors and a specially formulated proppant, the technology has been tested in field trials in West Texas, the Marcellus and STACK plays. CARBO is currently holding its fifth and hopefully last field trial of the product, Mr Palisch said.
Tackling produced water
Proppant provider Fairmount Santrol sees the need for fracking technologies that not only boost production and require a lower upfront investment but are simpler to deploy and more environmentally friendly.
Sid Banerjee, Product Manager for Self-Suspending Sand at Fairmount Santrol, said he is excited about applying the company’s self-suspending sand production line, Propel SSP, to reduce the use of fresh water in fracking operations. Propel SSP 350 can tolerate water with up to 350,000 parts per million total dissolved solids. The product had a soft launch in January 2017; the company continues to revise the technology for various applications, including refractures.
“Water has been one of the biggest waste streams in hydraulic fracturing in North America, as water types used had to be relatively clean. This put the oil and gas industry in competition with farms, ranches, cities and other entities that consume fresh water. Water shortages in some areas have heightened concerns over available supply,” Mr Banerjee said.
In terms of future technology development, Fairmount Santrol is looking at well refracture technology as E&P firms seek to boost production at the lowest cost possible. For the tenth of the cost of drilling a new well, production can be boosted or regenerated from an underperforming well or old well. Refracking an old well could pay off if the well’s problem is solved. But companies short on time have often opted to drill a new well in a new area with a design they can understand, rather than reengineer an old one. “There’s considerable interest in the space, but not a lot of understanding about what makes a well a good refracture candidate,” Mr Banerjee said.
未经允许,不得转载本站任何文章: