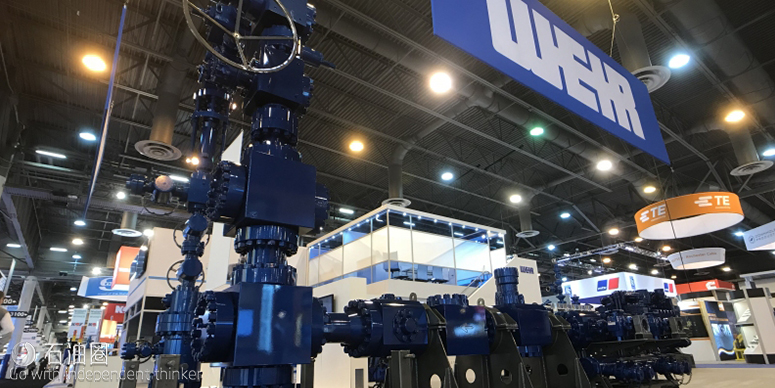
在钻井作业中,溢流是一种高发问题,常规检测器响应时间较长,操作人员无法及时发现、解决问题,Weir推出的新型智能检测器可以极大改善这一现状。
来自丨Weir
编译丨白小明 惊蛰
Weir油气公司是一家领先的压力泵和压力控制设备和服务提供商。近期,该公司宣布在智能传感器领域取得了重大突破,其研发的传感器可以实时准确地测量泥浆气体液位,防止溢流,并最大限度地提高安全性,同时提供主动溢流管理,降低清理成本并减少非生产时间。
溢流是氮气充气钻井作业中的一种高发风险,在Wyoming的一次作业中,钻井公司使用了Weir的传感器。之前,操作人员在溢流发生时紧急处理时间不足20分钟,而现在他们有3.5小时的时间来防止溢流,并避免流体进入副安全保护罐,从而减少停机时间和成本。过去几年中,这项增强技术为已安装设备的井队节省了数十万美元。
Mathena泥浆气体分离器智能液位传感器是Mathena泥浆气体分离器智能系统(MGS-ISC)的一部分,可精确测量泥浆气体分离器内的液位,适用于控压钻井和欠平衡钻井,能够在钻井现场精确控制溢流并提供实时数据。为操作人员提供了更多时间,避免气体进入使用中的泥浆系统,并防止出现液体从点火器系统溢出的情形。
传感器系统中可以添加控制阀自动操作功能,实现智能排液控制,进一步提高溢流处理能力。利用这种能力,泥浆排放可以完全封闭进行,以保持液体密封防止气体到达泥浆振动筛,同时降低泥浆罐溢出的风险并确保实现固液分离所需的理想气体流速。控制阀自动操作还有助于优化劳动效率。
采用Weir久经考验的系统方法,智能液位传感器也可以应用于副安全保护罐的全方位监控。Weir油气公司压力控制工程经理Matt Green表示,“目前,人工故障识别和响应时间不足以让操作人员避免溢流和泄露。提供实时数据可以防止事故发生,并最大限度地延长正常运行时间。”
Mathena智能液位传感器和MGS-ISC可与Weir的压力控制智能系统以及Mathena系统的其他模块集成,包括Mathena排气分析仪、智能流量仪表系统(VGA-ISF)和Mathena ECO-Tank智能系统(ECO-ISL),核心技术来源于Mathena Frac Flowback智能系统(FFB-ISL)。
Weir的智能系统产品在北美每个主要作业盆地都有技术支持,并与其他钻井平台数据管理系统集成,使钻井工程师能够在一个地方汇总所有数据。
在北美,钻井作业中经常会发生钻井液溢出到MGS排气管线中的情况。人工故障识别和响应时间通常不足以防止流体进入点火系统,从而造成溢出事故。为了改善识别能力和响应时间,Weir安装了泥浆气体分离器智能系统(MGS-IS),用于连续监测MGS中的实时液位。实时数据使决策制定更快、更明智。通过采用系统方法,Weir应用其基于波雷达液位测量的智能系统液位(ISL)技术来监控MGS和副安全保护罐,通过WITS将信息传输到本地EDR、本地物理警报系统,并通过云进行远程传输。
该系统避免了排气口溢流。预测MGS钻井液填充速率大大提高了人工响应的准备时间,从大约15分钟提高到近2.5小时。除了降低相关的HSE风险,该系统每月还减少了大约十几起溢出事件,节省了数千美元的清理成本和非生产时间。如果将Mathena IS技术推广应用到该地区的其他井,那么节约的成本将成倍增长。
监控应用的成功为增加控制阀自动操作功能奠定了基础,从而实现智能主动排放控制,这将进一步提高溢流处理能力。借助主动排放控制,泥浆排放可以完全封闭进行,以保持液体密封防止气体到达泥浆振动筛,同时降低泥浆罐溢出风险并确保实现固液分离所需的理想气体流速。
使用WM-IS获得的其他钻井液流量数据和控制,为提高安全性和理解钻井作业提供了新的机会。传输到钻机电子钻井记录仪后,数据可以协同阀门自动操作功能获得泵速数值,增强流体系统控制。WM-IS平台建立了一个节流与压井监测和控制系统,并可扩展包含排气流量监测和节流性能监测和控制。此外,Weir的Synertrex状态监测、过程效率和生产优化举措可以直接向钻井工程师或数据中心提供基于云的MGS数据报告。长期数据评估为提高安全性和效率提供了新的思路。
MGS-ISC可以作为单个产品使用,也可以与多种IS产品结合使用,如Mathena排气分析仪(VGA-ISF)。该系统还提供通过WITS通信协议与Pason、MD Totco和其他EDR平台集成的功能。
应用特性
- 主动溢流控制和液封保护,在不到18秒的时间内将完全打开的阀门关闭
- 适用于高压地层和环境敏感区域
- 波雷达技术用于监测MGS液位,并可与其他传感器集成来监测副安全保护罐
- 更准确的MGS液位传感和实时液位变化分析和性能监测
- MGS条件分析和报警
- 自动MGS液体排放控制
- 本地和远程性能监控,通过文本、电子邮件或基于云的门户将客户与数据连接起来
- 可存储、共享和报告实时数据,以供将来参考
- 可选的传感器和软件集成包,将MGS-ISC/F作为井筒返液流量计
- 电动控制系统,可优化性能并最大限度地减少执行器循环
- 手动执行器超控
- 可同时确保MGS排气分离效果,与Mathena™排气分析仪ISF集成
- 简化诊断和故障排除
- 可供出租,每个盆地都有服务中心;每次工作后都要经过全面检查和重新认证
- 安装和部署的交付周期为2-4周
适用作业
您也有让人挠头的难题需要解决,或是优质技术想要找应用市场吗?如果有的话,欢迎联系小编微信或邮箱,也许能找到一剂良药。
二丫:131-3255-0596;zhanglingyu@cnoocraiborn.com
For English, Please click here (展开/收缩)
Weir Oil & Gas, a leading upstream provider of pressure pumping and pressure control equipment and services, today announced it is achieving significant success in the field with intelligent sensors designed to accurately communicate mud gas liquid levels in real time to prevent overflows and maximize safety while providing active kick management, reducing cleanup costs and lowering non-productive time.
The sensor has been used in the Wyoming region in nitrogen-aerated drilling operations in which overflow is a constant risk. Where operators previously had less than 20 minutes of response time, they now have 3.5 hours to prevent overflow and eliminate liquid in the secondary containment vessel – thus reducing downtime and direct costs. This technology enhancement has generated hundreds of thousands of dollars in savings for installed sites over the course of a few years.
Mathena™ Mud Gas Separator Intelligent Level Sensor, part of the Mathena™ Mud Gas Separator Intelligent System (MGS-ISC), accurately measures the liquid levels within the mud gas separator for managed-pressure drilling and underbalanced drilling operations, providing accurate kick control and real-time data on-site. This gives operators much more time to avoid gas carryover to the active mud system and prevent an overflow scenario creating a fluid spill from the igniter system.
Control valve automation can be added to enable intelligent active discharge control that further improves kick-handling capacity. With this capability, the mud discharge can be completely closed to maintain the liquid seal needed to prevent gas from reaching the shale shakers while reducing the risk of vessel overflow and ensuring an ideal gas velocity for liquids and solids separation. The control valve automation also helps optimize labor efficiency.
Intelligent level sensors can also be applied to the secondary containment vessel for comprehensive monitoring with Weir’s proven systems approach.
“Manual event recognition and response time is insufficient for today’s operators to prevent overflows and spills,” said Matt Green, Pressure Control Engineering Manager of Weir Oil & Gas. “Providing real-time data prevents incidents and maximizes uptime.”
The Mathena™ Mud Gas Separator Intelligent Level Sensor and Mathena™ Mud Gas Separator Intelligent System (MGS-ISC) can be integrated with Weir’s Pressure Control Intelligent Systems as well as other modules of the Mathena system including the Mathena™ Vent Gas Analyzer and Intelligent Flow Meter System (VGA-ISF) and Mathena™ ECO-Tank Intelligent System (ECO-ISL.) All modules are available for rent. The core technology has been adapted from the Mathena™ Frac Flowback Intelligent System (FFB-ISL).
Weir’s line of intelligent systems is supported in every major basin in North America and integrates with other drilling rig data management systems, allowing drilling engineers to aggregate their data in one place.
Drilling operations in the area frequently experience drilling fluid overflow into the MGS gas vent line. Manual event recognition and response time is often insufficient to prevent fluid from entering the flare system and creating a spill incident. To improve recognition and response, Weir installed its Mud Gas Separator Intelligent System (MGS-IS) for continuous monitoring of real-time fluid levels in the MGS. The data enabled faster and more informed decision making. By taking a systems approach, Weir applied its Intelligent System Level (ISL) technology based on wave radar level measurements to monitor the MGS and secondary containment vessels, and communicated the information via WITS to the local EDR, local physical alarms, and remotely via the Cloud.
The system eliminated vent overflows. Projection of MGS drilling fluid fill rates dramatically increased manual response lead-time from approximately 15 minutes to nearly 2.5 hours. Along with lessening the associated HSE risk, the system mitigated approximately a dozen overflow incidents per month to save thousands of dollars in cleanup costs and non-productive time. The value is multiplied by the ability to extend the Mathena™ IS technology to many other wells in the area.
Success of the monitoring application sets the stage for adding valve automation to enable intelligent active discharge control that further improves kick-handling capacity. With active discharge control, the mud discharge can be completely closed to maintain the liquid seal needed to prevent gas from reaching the shale shakers. The control also reduces the risk of vessel overflow and ensures the ideal gas velocity for liquids and solids separation.
The additional drilling fluid flow data and control achieved with the WM-IS provides new opportunities for improving safety and understanding drilling operations.Delivered to the rig’s electronic drilling recorder, the data can inform pump rates in coordination with valve automation for enhanced fluid system control. The WM-IS platform establishes a choke and kill system monitoring and control system, expandable to include vent gas flow monitoring and choke performance monitoring and control. In addition, Weir’s Synertrex™ condition monitoring, process efficiency and production optimization initiative can provide cloud-based reporting of MGS data directly to the drilling engineer or data center. Long-term data evaluation offers new insights with the potential of additional safety and efficiency improvements.
Modular and flexible
The MGS-ISC can be deployed as a single product or integrate with multiple IS products, such as the Mathena™ Vent-Gas Analyzer (VGA-ISF). The system also offers integration capability with Pason, MD Totco, and other EDR platforms via WITS communication protocol.
Features
- Active kick control and liquid seal protection, with total valve open-to-close actuation in less than 18 seconds
- Ideal for high-pressure formations and environmentally sensitive areas
- Wave-radar technology to monitor MGS fluid levels and can be integrated with additional sensors to monitor secondary containment vessels
- More accurate MGS liquid-level sensing and real-time liquid-level change analysis and performance monitoring
- MGS conditional analysis and alarms
- Automated MGS liquid-discharge control
- Local and remote performance monitoring, connecting customers with data via text, email, or Cloud-based portal
- Real-time data that can be stored, shared, and reported for future reference
- Optional sensors and software integration package that establishes the MGS-ISC/F as a wellbore return flow meter.
- Electric-actuated control system to optimize performance and minimize actuator cycles
- Manual actuator override
- Simultaneously ensures MGS vent-gas separation performance, integrating with the Mathena™ Vent-Gas Analyzer ISF
- Simplified diagnostics and troubleshooting
- Available for rent, with service centers in every basin; fully inspected and recertified after every job
- Two-to-four weeks lead time for installation and deployment
Processes
- Drilling
- Low pressure flow control (Industrial)
未经允许,不得转载本站任何文章: