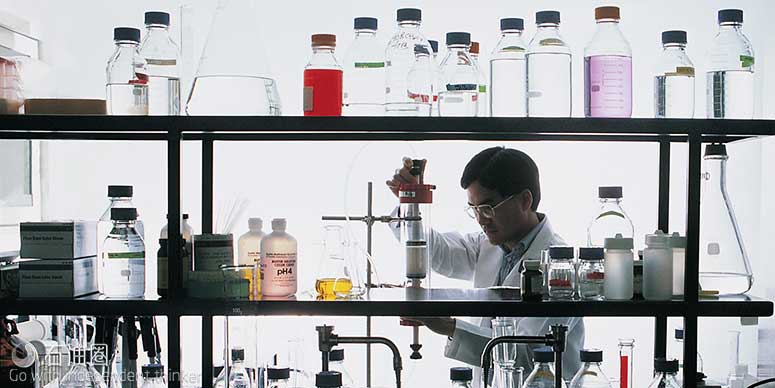
对于解决结蜡问题,最常见的化学解决方案之一是在产出液中添加结蜡抑制剂或降凝剂(PPD)。
来自 | E&P
编译 | 影子
现场使用的大部分PPD都是有机溶剂型。为了在较低的温度下能够自由流动,且保持稳定,这些PPD需要大量稀释至2~5%浓度。所选择的溶剂通常是大量的有毒有机溶剂,例如芳香族溶剂(例如二甲苯,甲苯或甲醇)。如果没有选择合适的溶剂或试剂配制的有效成分太高,PPD会结成凝胶,失效并难以处理。大量有机溶剂的使用成本较高,且对环境,储存设施和操作人员的安全构成威胁。
合格PPD的使用
为了应对这一挑战,Solvay公司开发了一种以聚合技术为核心的水基PPD分散体系。该体系的主要成分是一种专门设计的两亲聚合物,由亲水性聚合物头部基团和疏水尾部合成。通过控制分子结构和粒度,形成独特设计的分子量,从而形成独特而稳定的分散体。这种合成基产品可以保持较高的有效成分(15~30%甚至更高)。在聚合物配方中适当添加互溶剂和润湿性或分散性较好的表面活性剂后,即使在-40℃(-40℉)下也可正常泵送。一般来说,室温条件下PPD在40%有效成分时粘度为200~250cp,呈乳白色。
有四种通用的标准来检测PPD的使用。
首先是产品热稳定性。Solvay公司的水基PPD使用Chandler 5550高温高压粘度计在500psi(磅/平方英寸)的条件下测试粘度,在200℃(392℉)以下温度可以保持稳定。
其次,该材料须是环境友好型。PPD分散在水或与水互溶的溶剂中,取代了有毒溶剂的使用。
第三个标准是测试在-40℃下的粘度。Solvay公司的PPD的倾点为-30℃(-22°F),有效成分为40%,可在-40℃下配制为可泵送的体系。
最后,材料的闪点必须以配方产品的浓缩液为标准。由于PPD分散在水或高闪点溶剂中,因此在这方面无危险。
PPD检测
满足四个标准后,然后检测沉积控制性和降凝性。检测人员取西德克萨斯州的不同种原油评估了Solvay公司的第一代水基PPD分散体系的性能。第一代PPD与常用溶剂型PPD比较的结果表明,Solvay公司 PPD能够显著降低近70%的原油蜡质沉积,并将原油倾点降低了18℃(64.4℉);使用标准冷凝管评估了沉积控制性,并且使用PSL Systemtechnik GmbH倾点测试仪(图1)测试了降凝性。
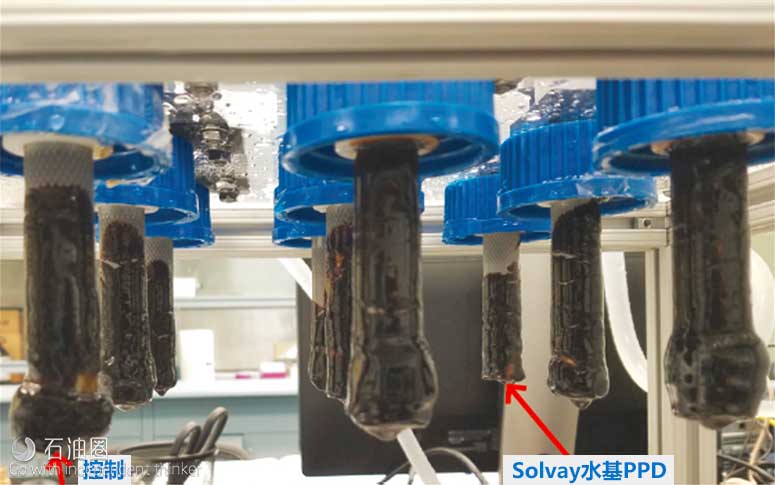
图1.在西德克萨斯州原油的冷凝测试中,使用Solvay的水基PPD比对照样品及其他PPD产品显示出更好的蜡沉积控制性能。
众所周知,PPD的性能是与特定原油性质有关。为了进行准确的比较,按照已知配方混合成模拟原油。模拟原油包含有分散溶解在低分子量烃例如癸烷,十二烷和十四烷中的石蜡(来自Sigma Aldrich)等混合物。低分子量烃用作蜡的溶剂,并且如果需要的话,可以通过气相色谱帮助分离馏分。
在溶剂中添加5%的石蜡混合物,将水基聚合物分散体系和市售结蜡抑制剂/PPD聚合物加入到含5%石蜡的脂肪烃样本中,通过对比其表现出的性能进行筛选。聚合物添加浓度为500ppm(作为有效成分)。将样品充分混合并在85℃(185℉)(高于结蜡温度)下储存1~2小时以消除温度差异影响,然后在冰箱中(0~5℃)储存一整夜。
将样品从冰箱中取出后记录其外观表现,并使用带相机的偏光显微镜进行评估。
将显微镜放大100倍(图2),观测到的纹理用交叉偏光镜或正交偏光镜和云母过滤器(1/4λ测试板)进行观察,并使用数码相机拍摄纹理图像,通过图像捕捉软件进行处理(图2)。模拟原油凝胶化后形成大量的斜方或针状(刺状)晶体(10~30μm)。与之对比的PPD虽然也抑制了大蜡晶体的形成,但蜡晶体(约10μm)的尺寸远大于水基PPD分散体系中的尺寸(约1~5μm)。此外,与Solvay公司的水基PPD相比,模拟原油具有更高的粘度(流动性也不好),表明Solvay公司的水基PPD性能更加优越。
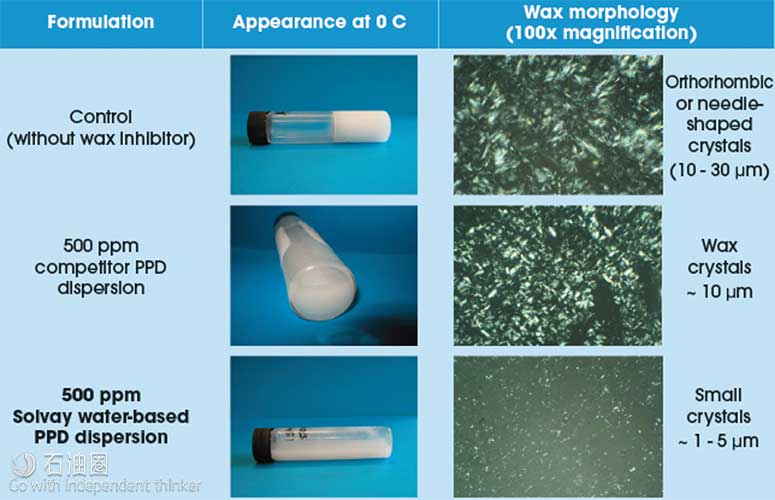
图2.本实验测试了模拟原油中水基PPD的结蜡抑制性能,并通过显微镜观察与其他商业PPD产品进行了对比。与竞争产品相比,添加水基PPD的模拟原油保持较好的流动性,且只形成少量蜡晶体。
而且,与传统的有机PPD相比,Solvay公司的水基PPD在低温应用方面也有优势。Solvay的水基PPD分散体系体现其优势的一个例子就是在极寒气候中的使用。为了能够在寒冷的环境中成功应用特定的PPD,PPD必须大量稀释至约2~5%的有效含量,使用二甲苯保持其低粘度以便将其加入到井中。实际使用的聚合物的有效含量非常有限,并且添加的大部分溶剂仅仅作为载体被浪费。 但是,Solvay公司的水基PPD分散体系在20%的有效含量下仍可以正常泵送,这比传统的PPD具有更高的有效含量,从而提高了效率。
PPD和结蜡抑制剂的性能与原油密切相关,因为它取决于原油的许多特定参数,包括API比重、轻馏分、沥青质含量和碳链分布等等。Solvay正在开发一系列这些水基聚合物PPD分散体系,以适用许多不同的原油种类,帮助油气行业解决这一重要挑战。
您也有让人挠头的难题需要解决,或是优质技术想要找应用市场吗?如果有的话,欢迎联系小编微信或邮箱,也许能找到一剂良药。
二丫:131-3255-0596;zhanglingyu@cnoocraiborn.com
For English, Please click here (展开/收缩)
As crude oil comes to the surface and exits a well, it cools down, generally causing the wax components of the crude to gel. The gelled crude chokes the well, leading to restricted or blocked production and costly downtime for operators. One of the most common chemical solutions to address the wax deposit challenge is the application of wax inhibitors or pour point depressants (PPDs) to the production stream.
Most of the PPDs used in the field are organic solvent- based. To maintain a stable, free-flowing formulation at very low temperatures, these PPDs need to be heavily diluted down to about 2% to 5%. The solvents of choice quite often are large quantities of toxic organic solvents such as aromatic solvents (e.g., xylene, toluene or methanol). If the proper solvent is not used or the activity of the formulation is too high, the PPD will gel, becoming extremely difficult to handle and dose efficiently. The application of a large amount of solvent is not cost-effective and poses threats to the environment, storage facilities and the safety of the personnel handling the materials.
Qualifying PPD use
To address this challenge, Solvay developed a waterbased PPD dispersion system centered on the company’s polymerization technology. This technology is a specifically designed amphiphilic polymer that is synthesized with a hydrophilic polymeric head group and hydrophobic tail. The molecular weight and, specifically, the architecture and particle size of this polymer can be controlled, creating a unique and stable dispersion. This synthesized product can maintain high activity (15% to 30% or higher) and remain pumpable even under -40 C (-40 F) after properly formulating the polymer with a mutual solvent and wetting or dispersing surfactant. Generally, the viscosity of the PPD, at 40% activity, is between 200 cp and 250 cp at room temperature with a milky color.
There are four common standards for which to qualify a PPD for use. The first is that the product must be thermally stable. Solvay’s water-based PPD is stable up to 200 C (392 F) under 500 psi tested by a Chandler Viscometer 5550. Second, the material should be environmentally friendly. The PPD is dispersed in water or a water-mutual solvent package, which replaces the need for the application of toxic solvents. The third standard is the viscosity of the formulation at -40 C. Solvay’s PPD has a pour point of -30 C (-22 F) at 40% activity and can be formulated to be pumpable under -40 C. Finally, the flash point of the material must be considered as both a concentrate and a formulated product. This PPD is not hazardous in this aspect since it is dispersed in water and/or a high flash solvent.
PPD testing
Once the four standards are met, the deposit control and pour point reduction performance is examined. The performance of Solvay’s first-generation water-based PPD dispersion was evaluated using several crude oils from West Texas. This first-generation PPD was compared to some commonly used solvent-based PPDs, and the results showed that the Solvay PPD significantly reduced crude oil wax deposition by nearly 70% and reduced the pour point of the crude by 18 C (64.4 F). The deposit control performance was evaluated using a standard cold-finger apparatus, and the pour point reduction was tested using a PSL Systemtechnik GmbH pour point tester (Figure 1).
It is well-known that PPD performance is crude-specific. To make an accurate comparison, a model crude oil is blended following a published recipe. The model crude oil comprised a mixture of paraffin waxes (from Sigma Aldrich) dispersed in a low molecular weight hydrocarbon such as decane, dodecane and tetradecane. The low molecular weight hydrocarbon was used as a solvent for the wax and to aid differentiation of the fractions by gas chromatography if required.
The mixture of paraffins (5%) was added to the solvents. The performance attributes of the aqueous polymer dispersions and commercial wax inhibitor/PPD polymers were screened by adding them to samples of 5% weight to volume paraffin wax in aliphatic hydrocarbon. The polymers were dosed at 500 ppm (as active), respectively. The samples were mixed thoroughly and stored at 85 C (185 F) (above the wax appearance temperature) for 1 to 2 hours to eliminate the thermal history of the samples before cooling overnight in a refrigerator at 0 C to 5 C (32 F to 41 F).
The appearance of the samples was noted after removal from the refrigerator and assessed using a polarized light microscope with camera attachment.
The microscope was set at 100x magnification (Figure 2), and the textures observed were viewed either with crossed polarizers or crossed polarizers and mica filter (1/4 λ test plate). Images of the textures were taken using a digital camera and processed using image capture software (Figure 2). The model crude oil gelled up and formed a large amount orthorhombic or needle- shaped (bayonet) crystals (10 μm to 30 μm). The competitive PPD inhibited the formation of large wax crystals, but the size of the wax crystal (about 10 μm) is much larger than that in the water-based PPD dispersion (about 1 μm to 5 μm). Also, the model crude oil has higher viscosity (not flowing as well) compared to the Solvay water-based PPD, indicating a much better performance of the Solvay water-based PPD.
Moreover, compared to the conventional organic PPD, Solvay’s water-based PPD has an advantage in low-temperature applications. An example of a situation where Solvay’s PPD dispersion will have an advantage is in its use in very cold climates. To be able to successfully apply a typical PPD in a cold environment, the PPD would have to be heavily diluted to about 2% to 5% active, using xylene to maintain low viscosity so that it can be dosed into the well. The amount of active polymer actually applied is very limited, and much of the solvent added is wasted simply as a carrier. However, Solvay’s water-based PPD dispersion can remain pumpable at 20% activity, a far greater active level than traditional PPDs and thereby increasing efficiency.
PPD and wax inhibition performance is certainly very crude-specific, as it depends on many particular parameters of the crude, including API gravity, light ends, asphaltenic content and carbon chain distribution to name a few. Solvay is developing a series of these polymeric water-based PPD dispersions to address the many different crude varieties, helping the industry tackle this important flow assurance challenge.
未经允许,不得转载本站任何文章: