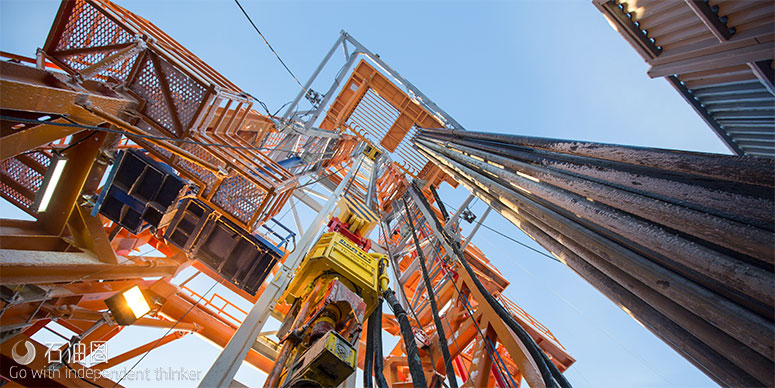
SLB与Stena Drilling合作开发的业内首款适用于深水作业的集成MPD系统投入了应用。
来自 | Eva Vigh
编译 | 张德凯 影子
近日,斯伦贝谢推出了业内首个完整的深水MPD集成解决方案。不同于常规方法,该解决方案仅有一个控制系统,需要的操作人员也更少。立管单根是该系统的一大特色,由旋转控制装置(RCD)、超薄环形防喷器和流量滑阀组成,总重约80000lb,长度40ft,是当前同类产品中尺寸最小、重量最轻的,能够大幅提高作业效率。M-I SWACO MPD产品经理Bas Liezenberg说:“我们的目标是降低开发商开发成本”。
通过高度集成,斯伦贝谢将立管单根的尺寸和重量都大幅降低,所有部件都集成在一个新设计中。“MPD立管单根通过一条脐带缆控制,该脐带缆也是由两根常规脐带缆集成得到,控制系统本身是五个独立控制系统的集成产物,”Liezenberg介绍到,“通过将M-I SWACO和Cameron的系统集成,实现了作业过程中MPD全部组件的可视化,并以预先设计和协调的方式做出反应。截至目前,该系统已在北美、拉丁美洲、挪威、俄罗斯、非洲、东南亚和中东得到了应用,完成了400多口井的钻探作业。”
Liezenberg表示,“由于单根的尺寸和重量都显著降低,一次起重就可完成配置和安装,MPD设备与立管的连接时间减少了一半。”斯伦贝谢的作业数据显示,通过使用该系统,设备安装、回收时间节约了75%,这主要得益于单次起升钻作业效率的大幅提高和立管控制与管路的良好结合。
密封旋转系统(SRS)置于RCD内并锁定,同时RCD具有可伸缩活塞设计。当SRS处于未安装、活塞处于收缩状态时,RCD内部是平滑的,不需要使用耐磨轴套。这就意味着当MPD开始运转时,一次下钻就可以完成轴承的安装,而常规系统则需要在轴承安装前将轴套移除,减少了作业时间。“显而易见,通过技术改进,只需一次下钻即可完成作业,大幅降低了作业时间,”Liezenberg说。
MPD系统的每个部件都配置了传感器,可以连续发送实时数据至地面控制系统,包括井筒压力、温度和流入/流出数据等。“基于这项功能,我们可以根据测量和/或计算数据点来设置报警窗口。当实际数值超过设定值,控制系统会发出警报,提醒操作员发生了异常情况,”Liezenberg说。
此外,MPD系统还可以进行功能扩展以满足井筒的特殊需求,并可根据井筒和/或操作人员的需求复杂性,进行手动或实时水力模型模式操作。
斯伦贝谢与Stena一起,利用跨度广泛的专业知识和经验,最终带来了业内首个全OEM(代工生产) MPD系统,该技术于2017年一季度交付Stena Drilling。随后,该系统在Stena Carron钻探船上进行了安装和调试,使其成为业内首个获得DNVGL DRILL MPD入级符号的钻井船。
闭合回路MPD系统首次应用在Guyana的海上油田完成,两口井的井眼尺寸分别为12-1/4in和8-1/2in,作业区域水深达2735米,最终钻井作业顺利完成。
“按照最初的设计,该系统可用于任何井底压力恒定状况的作业,包括控压固井、控压电缆作业、地层完整性动态测试。例如,在恒定井底压力控制模式下,该系统可以根据设计值控制压力变化范围在+/- 0.1ppg范围内。在此种模式下,通过调整扼流器位置来控制环空压力,达到井底压力恒定的目的。”
您也有让人挠头的难题需要解决,或是优质技术想要找应用市场吗?如果有的话,欢迎联系小编微信或邮箱,也许能找到一剂良药。
二丫:131-3255-0596;zhanglingyu@cnoocraiborn.com
大安:131-3203-1392;lishian@cnoocraiborn.com
For English, Please click here (展开/收缩)
Schlumberger has introduced the industry’s first complete deepwater MPD integrated solution that uses only one control system and requires fewer personnel to operate. The system features a riser joint – including a rotating control device (RCD), a slim-line annular blowout preventer and flow spool – that weighs just over 80,000 lb and measures 40-ft long, making it the shortest and lightest available on the market, according to Bas Liezenberg, DPM Deepwater Product Champion, M-I SWACO, a Schlumberger company. “Our goal was to reduce the total cost of ownership,” he said.
The small size and light weight of the riser joint is enabled by a high level of integration, where all components of the riser joint were integrated into one design. “The MPD riser joint is operated through a single umbilical, which is also an integration of two umbilicals into one, to the single control system. The control system itself is also an integration of five control systems into one,” Mr Liezenberg said. The integration of M-I SWACO and Cameron systems allows the components to be visible to one another at all times and react in a pre-designed and coordinated manner. The control system has previously been deployed in North America, Latin America, Norway, Russia, Africa, Southeast Asia and the Middle East to drill more than 400 wells.
“Because of the joint’s reduced size and weight, it can be picked up and deployed in a single lift, halving the time associated with running MPD equipment into a riser,” Mr Liezenberg said. Schlumberger believes it has achieved a 75% reduction in flat time associated with deployment and retrieval, he added, much of it attributed to the ability for single-lift deployment and Schlumberger hook-up of riser control and flow lines.
The sealed rotating system (SRS) lands and is locked inside the RCD with retractable pistons. When the SRS is not installed and all pistons are retracted, the inside of the RCD is flush and, therefore, does not require a wear sleeve. This means when MPD operations have started, the bearing can be deployed in a single run, unlike other systems that require the wear sleeve to be removed before the bearing can be deployed. “This results in a single deployment run that reduces the flat time associated with this type of operation,” Mr Liezenberg explained.
Each component of the system is outfitted with sensors that continuously send data, such as wellbore pressure, temperature and flow in/out, back to the control system for processing. “It gives us the ability to set alarm windows around measured and/or calculated data points,” Mr Liezenberg explained. When a parameter is breached, the control system raises alarms to alert the operator of any abnormal conditions.
The MPD system is also scalable to fit specific well demands and can be run in manual or real-time hydraulic model-based mode, depending on the complexity of the well and/or operator needs.
Schlumberger, alongside the expertise of Stena Drilling, drew experience across a broad range of disciplines to deliver the industry’s first all-OEM MPD system, which was delivered to Stena Drilling in Q1 2017. The system was installed and commissioned onboard the Stena Carron, which resulted in the drillship obtaining the industry’s first DNVGL DRILL MPD notation.
The closed-loop MPD system was primarily installed to safely drill to TD offshore Guyana. The system was utilized on two well locations to drill 12 ?-in. and 8 ?-in. sections in water depths up to 2,735 m.
“The system performed as designed for constant bottomhole pressure, managed pressure cementing, managed pressure wireline operations and performing dynamic formation integrity tests,” Mr Liezenberg said. For example, pressure management stayed within +/- 0.1 ppg of the desired pressure during constant bottomhole pressure control mode, he said. In this mode, he explained, the target pressure downhole is kept constant by controlling the annulus surface pressure through the means of a choke position.
未经允许,不得转载本站任何文章: