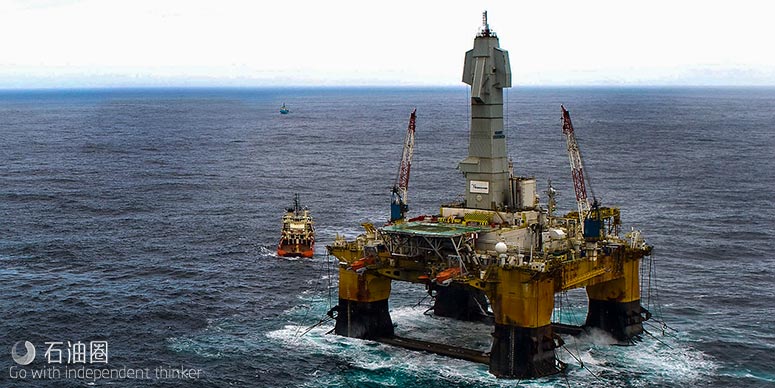
膨胀工具的技术进步,已使其成为了作业公司在整个油气井生命周期中值得依靠的一项技术。
来自 | TAM International
编译 | 白小明
膨胀封隔器的主要用途之一是在建井时的固井阶段。膨胀元件紧贴在套管上,作为多级固井或井底固井作业的底部支撑,当然这只是膨胀工具最常见的用途之一。在油气井生产阶段要进行修井作业时,如果使用机械桥塞或封隔器存在井下限制,通常需要使用膨胀工具。例如,可膨胀工具可以采用电缆从生产油管内下入做封堵之用,或者可以与连续油管连用进行过油管挤注作业。通常,过油管作业比较理想;否则,作业公司必须进行压井以实施油井干预作业。另外,在裸眼完井需要进行油井测试或堵水时,可膨胀工具也非常适用。对于海上油井,膨胀工具也是P&A作业经常需要进行的切割锻铣工作的理想工具。
测量裸眼原始应力
明确裸眼井段的原始应力有诸多益处,首先,地层应力对于注水井非常重要,因为需要知道油气藏盖层的岩石强度以确保注入区的压力完整性,并且要确保不形成可能使注入流体窜到区域以外的裂缝。原始应力数据还可帮助工程师选择最佳的套管下入深度。钻井团队在设计套管鞋深度时,当井下信息受限或者采用预测模型时,他们通常比较保守。如果套管下太早可能会增加成本;而如果下太晚,可能过于激进,导致井控问题,甚至要启动成本高昂的应急预案。
常规测量原始应力的方法是采用电缆部署的地层测试工具。然而在井斜大于30°的井中,可用的液压能较小,不足以使电缆地层测试器获得精确的测量数据。
膨胀工具替代方案
采用配有压力表的裸眼膨胀封隔器,已成为电缆地层测试工具的一个成熟替代方案。使用膨胀裸眼封隔器可以不受液压能限制进行测试。虽然这种作业成本更高且风险更大,但这需要将其与应力预测不确定性带来的成本进行权衡。
作业公司已成功利用裸眼膨胀封隔器来测量原始应力。经验表明,当办公室人员和井队人员制定了详细的作业计划后,实际作业往往能够取得成功。在最近的两个案例中,作业公司在海上采用了裸眼膨胀封隔器来隔离和测量原始应力。
在一个案例中,使用了两个封隔器的跨式配置,完成了应力的测量。这种配置相比仅采用一个封隔器而言,可以使工程师能够更精确地确定测量的位置。测试的目的是测量原始应力,以便在井的整个生命周期内管理注入压力。采用膨胀封隔器测量原始应力的基本操作是通过向地产注入流体,加压并初步形成裂缝,同时保持恒定的注入速率。然后获取裂缝传播压力和闭合压力以确定应力数据。对于每个坐封深度,测试通常重复3次。
单封隔器案例研究
使用单封隔器配置,也可以实现同样的裂缝传播过程,然后测量关闭压力。然而,使用单个封隔器,无法确定在封隔器下方裂缝开始形成的具体深度。对于一些作业人员来说,相比隔离不同井段获得的更高精度,他们更看重采用单个封隔器,而不是两个封隔器的低风险。该作业公司在一次深水作业中使用单个封隔器方法成功测量了原始应力,获得了足够的可用数据,以准确预测下一开套管鞋深度。与之前采用应力预估相比,通过避免下入额外的钻井尾管,单封隔器应力测量作业节省了大量成本。
高膨胀元件
深水封井和弃置(P&A)作业时,通常在预弃井程序前,需要使用连续油管来完成所需的各种服务。很多时候,用于连续油管设备的BOP内径比管柱的内径小。在这种情况下,就需要使用高膨胀率的膨胀元件。通常来说,预弃井作业是指在动员钻机进行完整的P&A作业前,进行产层隔离。使用连续油管装置进行预弃井工作成本较合理且安全性高。采用连续油管完成初期作业可以确保井控安全。
案例分析
在一个多分支井项目中,需要在筛管上坐封桥塞,然后打水泥灰。坐封桥塞的套管为6-5/8in,其上为5-1/2in油管,如图6。根据5-1/2in油管的最小内径选择了4-3/4in的膨胀工具。封隔器下到位后,打压膨胀并坐封桥塞,如图7。采用液压丢手工具使送入工具与桥塞断开,之后在桥塞顶打水泥灰。
水泥固化后,进行了压力测试来评估水泥塞的压力完整性,通常需要在地面打压来完成此项工作。然而,在某些井,水泥桥塞之上压力并不完整。在这种情况下,采用一个2.90-in外径的多次坐封封隔器,坐封在桥塞之上进行压力测试。
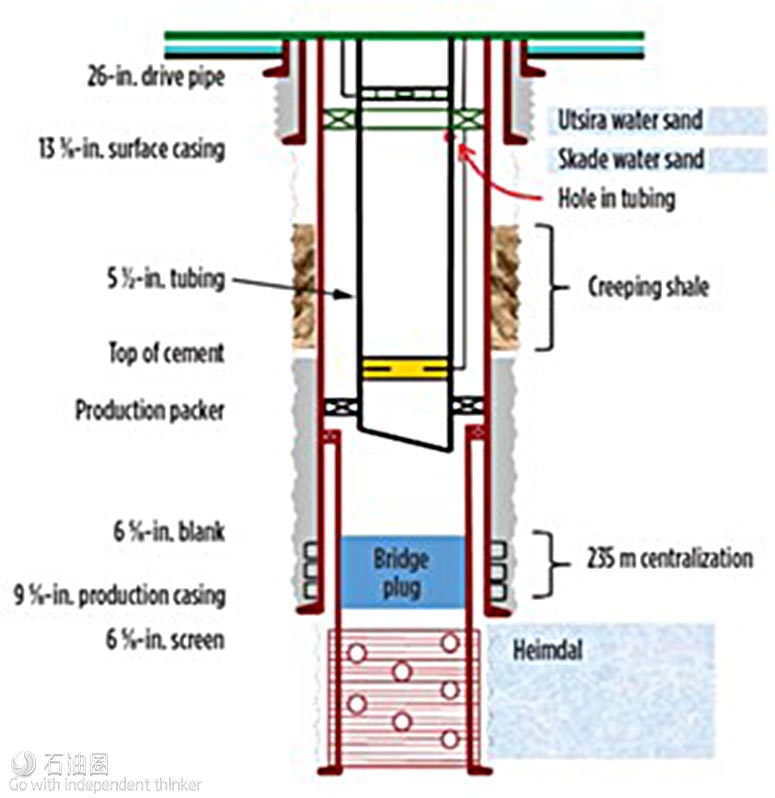
图6.一个大规模P&A项目中的典型井的示意图
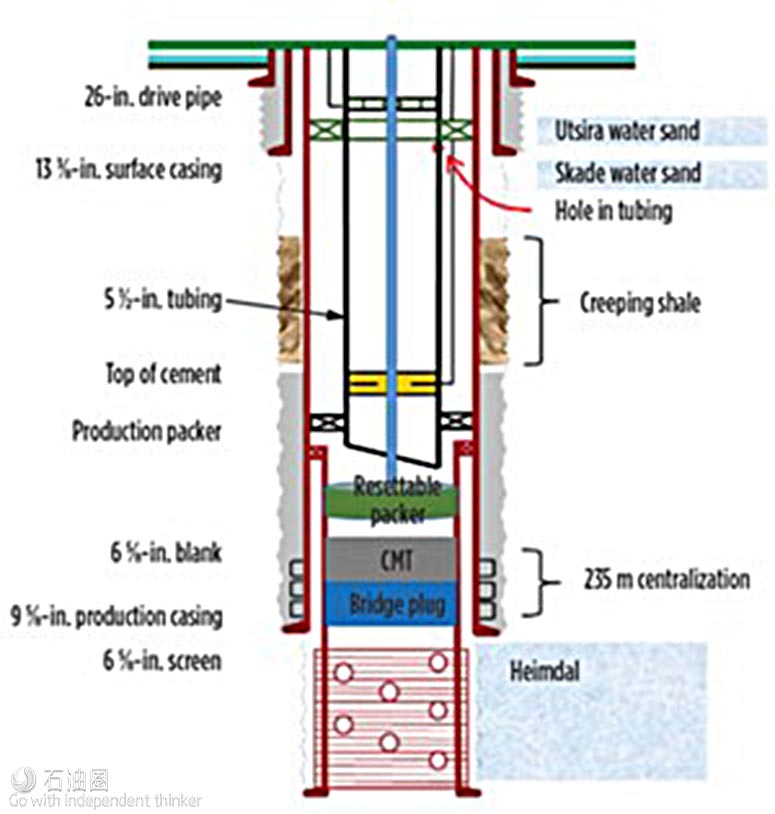
图7.封隔器位置图和井内工具详细图
作业结果
总共成功完成了16口井的预弃井作业,使用连续油管下入膨胀桥塞。此项目的成功很大程度上得益于作业前详尽的设计规划。虽然工程师有意愿,但许多情况下,并非所有的相关人员都参与了设计过程。参与人员最好包括平台工作人员、连续油管操作人员和负责下入膨胀工具的服务人员。他们的参与利于明确工作的重点环节并识别出关键的意外风险。在这种多分支井项目中,“做好充分的准备,再付诸行动”是明智之举。
结论
在过去20年,膨胀工具的设计有了明显的提高,技术的不断研发使其应用范围不断扩大。在无法采用传统的方法时,这些新的膨胀工具为作业公司提供了一种经济有效的替代方案。选择膨胀工具的首要原因是其可以克服使用标准工具的井眼限制;其他原因包括保护措施较弱,或者套管腐蚀,使用标准方法可能损坏套管。膨胀工具还具备在受限条件下的回收能力,而且对于大尺寸套管,在常规工具供应不足或者根本就没有相应常规工具的情况下,膨胀工具可以有效解决问题。
您也有让人挠头的难题需要解决,或是优质技术想要找应用市场吗?如果有的话,欢迎联系小编微信或邮箱,也许能找到一剂良药。
二丫:131-3255-0596;zhanglingyu@fonchan.com
大安:131-3203-1392;lishian@fonchan.com
For English, Please click here (展开/收缩)
MEASURING IN-SITU OPEN-HOLE STRESS
Knowing the in-situ stress of an open-hole section is desirable for several reasons. Firstly, stress values are crucial to managing an injection well to ensure that the injection zone maintains integrity with respect to cap rock strength and that no fractures are created that would allow injection fluids to go out-of-zone. In-situ stress measurements also help engineers select optimal casing shoe depths. Drilling teams are typically conservative when planning casing shoe depths when there is limited information or predictive modeling is used. However, setting casing early may drive-up well cost, or conversely, estimations may be aggressive which could lead to well control issues and implementing costly contingency plans.
The typical method used to measure in-situ stress is a wireline deployed formation testing tool. However, in wells with angles of more than 30° challenges arise due to the small volume of available hydraulic energy, which may not be sufficient for a wireline formation tester to gain accurate measurements.
Inflatable alternative. The use of an open-hole inflatable packer, equipped with pressure gauges, is a proven alternative to wireline formation testing tools. Using an inflatable open-hole packer allows access to unlimited hydraulic energy to perform the test since fluid is being pumped from surface. While this operation has a higher cost and poses greater risk, these must be weighed against the cost of the uncertainty in estimating stress.
Operators have successfully used open-hole inflatable packers to measure in-situ stress. Experience has shown that when office and rig personnel conduct detailed job planning, execution of the operation is successful. In two recent cases, companies working in an offshore environment used open-hole inflatable packers to isolate and measure in-situ stress.
Measurements were made in one case with a straddle configuration using two packers. This type of set-up enables engineers to determine exactly where the measurement was taken as opposed to when only one packer is deployed. The purpose of the test was to measure the in-situ stress to manage the injection pressure through the life of the well. The basic operation in measuring in-situ stress with an inflatable packer is to pressure up and initiate a fracture by injecting fluid into the formation while maintaining a constant injection rate. The fracture propagation pressure and closure pressure thus obtained are then used to determine the stress measurement. This test is typically repeated three times for each setting depth.
Single packer case history. The same process of propagating a fracture and then measuring the closure pressure was performed using a single packer configuration. However, with a single packer there is no way to determine at what depth below the packer the fracture was initiated. For some operators, the reduced risk of running one packer, rather than two, is more advantageous than the greater accuracy that comes from isolating an interval. This operator used a single packer approach in a deepwater application to successfully measure in-situ stress, deriving enough usable data to accurately predict the next casing point. The simplified operation generated substantial cost savings by eliminating an additional drilling liner compared to stress estimations used on previous wells.
HIGH EXPANSION ELEMENT
Deepwater plugging and abandonment (P&A) operations commonly use coiled tubing to deploy various services required in pre-abandonment procedures. In some instances, the BOP riser package for coiled tubing units can have an ID smaller than the ID of the pipe where an operation is to be performed. This restriction typically requires the use of a high expansion inflation element. Pre-abandonment work is often done to isolate production zones prior to moving in a rig to perform the full P&A procedure. Doing pre-abandonment work with a coiled tubing unit is cost effective and operationally safe. Doing the initial work on coiled tubing further allows complete well control to be maintained since the work is conducted through the existing wellhead.
Case study. A multi-well campaign was planned and required a bridge-plug be set above screens and cement dumped on top. The casing to set the bridge-plug in was 6 5/8-in. with 5?-in. tubing above. A 3?-in. inflatable element was selected based on the minimum restriction in the 5?-in. tubing. The packer was deployed to depth, and pressure was applied to inflate and set the plug. A hydraulic disconnect was used to release the tool from the plug, after which cement was spotted on top of the plug.
Once the cement had set, a pressure test was performed to assess the integrity of the plug. This typically was done by applying pressure at the surface. However, in some wells pressure integrity was lacking above the cemented bridge plug. In these cases, a multi-set packer with a 2.90-in. OD was run in the well to set just above the bridge-plug, to perform a pressure test.
Results
In all, 16 wells were successfully pre-abandoned, using inflatable plugs run on coiled tubing. Much of the success of this project was due to the detailed pre-job planning. While engineers have good intentions, in many cases not all stakeholders are included in the planning process. It is important to include platform workers, coiled tubing operators, and the actual service personnel responsible for running inflatable tools. Their input can highlight important details and identify critical contingencies. It is wise to “measure twice and cut once,” in this type of multi-well campaign.
CONCLUSION
Inflatable tool design has improved significantly over the past 20 years, and research and development is ongoing to extend the limits of the technology. These new inflatable tools provide operators with a cost-effective alternative method when a conventional approach is not possible. The primary reason for selecting an inflatable tool is to circumvent a wellbore restriction that prevents the use of a standard oilfield tool. Other reasons are to safeguard weak and/or corroded casing that might be damaged using standard methods. Inflatables also have the capability to retrieve a tool through a restriction, and efficiently handle large casing sizes where conventional tools may be in low supply or non-existent.
未经允许,不得转载本站任何文章: