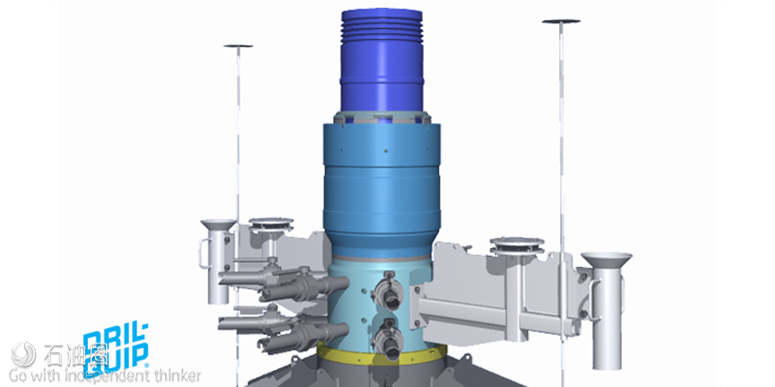
面对深海高温高压井复杂的生产环境,Dril-Quip公司推出新一代水下井口系统,该套设备以其优越的性能表现解决了深海井口系统面临的多种技术挑战。
来自 | Dril-Quip
编译 | 葡萄
Dril-Quip公司的BigboreⅡe水下井口系统可以灵活调节以匹配复杂的套管组合形式,满足水下高温高压的生产环境要求。整套设备通过了结构性能测试和抗疲劳测试。其高压井口头公称内径18-3/4″,工作压力等级有15000psi和20000psi两种,工作筒外径有27″和30″两种,井口头可匹配连接表套以及16″和18″两种辅助套管悬挂系统。
系统特征
(1)消除钻井/生产锁定设备;
(2)密封总成可实现高温高压下悬挂锁定载荷达2百万磅;
(3)通过减少起下钻次数大大降低操作费用;
(4)其载荷能够承受钻机2万磅/平方英寸的压力强度和高温高压井设计承载需求;
(5)DXe锁定剖面提高了结构性能和抗疲劳强度;
(6)根据API 16A第四版和API 17 TR7标准,该设备通过正常、极限和生存载荷试验;
(7)通过全套设备的抗疲劳测试;
(8)在20000psi、35-350℉条件下进行动态密封性测试,测试结果符合API 6A 附录F PR2 Group 4标准要求。
系统设计
BigboreⅡe水下井口系统是专为深海高温高压井口设计的新一代井口系统。
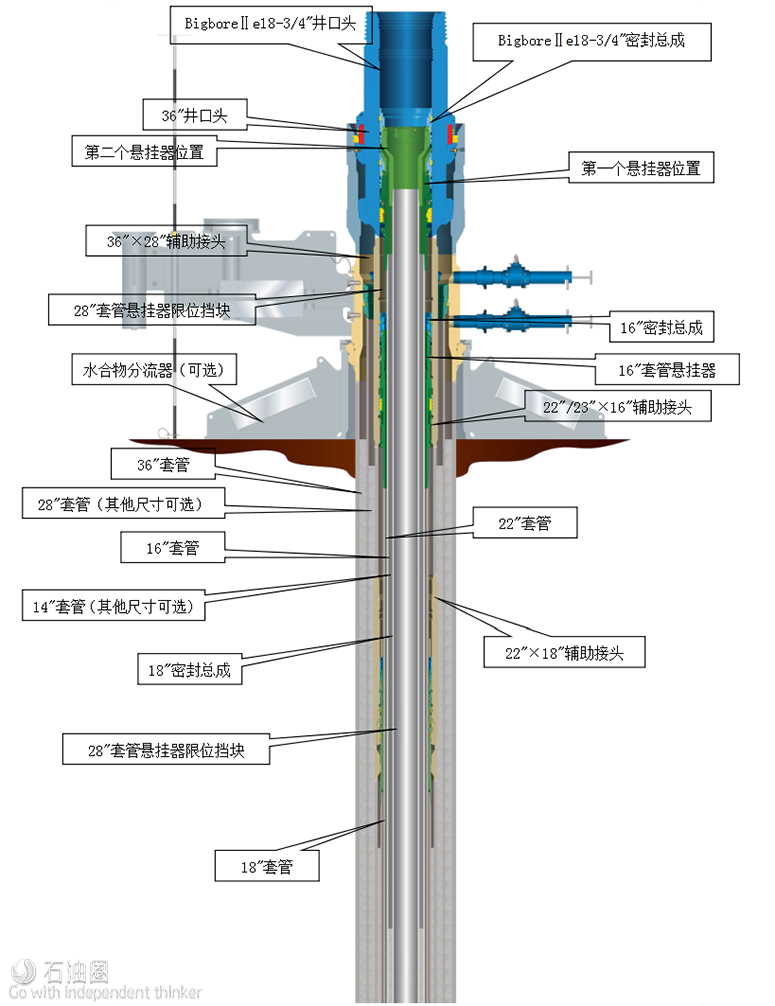
(1)采用金属对金属密封形式,在35-350℉条件下,可用于15000psi(27″)和20000psi(30″)两种工作压力和含有硫化氢的环境。
(2)系统底部内孔承载台阶可承受880万磅的末端载荷(包括套管重量和实验压力)。
(3)DXe锁定剖面使得设备具备很强的抗弯、抗拉和承载能力。
(4)利用位于22″/23″表套接头处的辅助接头连接18″和16″套管悬挂辅助系统。
(5)18″和16″套管、套管悬挂器和可测试/检索/更换密封总成能够通过外径为21″的钻井隔水导管、18-3/4″的防喷器组和BigboreⅡe井口头。
(6)所有的悬挂器和密封总成都是通过钻杆一次下入、安装和测试的。
(7)高压井口头以2百万磅预载荷锁紧低压井口头,将导管和表套组装在一起,提高设备抗弯和抗疲劳性能。
(8)应用了已被现场验证过的BigboreⅡ-H高温高压金属对金属密封技术。
(9)利用远程辅助环空封闭监测系统监测所有水泥返高至地表的套管柱。
(10)所有套管悬挂器环空流道面积大。
(11)可通过钻头的抗磨衬套和抗磨补心。
(12)可供选择的水合物导流板。
(13)具有备用套管。
(14)所有组件设计都是基于目前BigboreⅡ-H技术和BigboreⅡ的现场成功应用经验。
套管悬挂器密封总成
BigboreⅡe套管悬挂器密封总成具有高强度锁紧能力和双向高压金属对金属密封,适合用于高温高压液体或气体中。
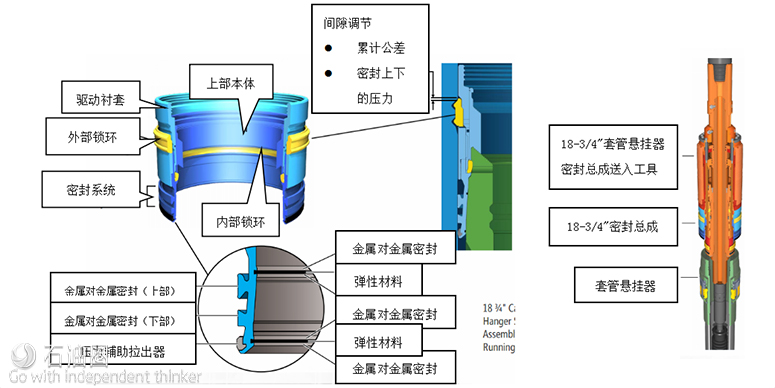
(1)井口凹槽处的密封用于防止密封筒划痕;
(2)外部锁环锁紧井口,固定住密封件,防止套管受热后套管悬挂器和密封总成产生过多移动;
(3)内部锁环锁紧套管悬挂器,防止密封件受到下压影响产生移动;
(4)密封总成外部锁环具备2000000磅的锁紧力;
(5)在气体介质中,按照API 6A PR2要求无泄露以及Group 4动态密封测试要求没有弹性材料,均成功通过测试;
(6)金属对金属密封采用重力加压实现密封;
(7)密封总成下部有一个压力辅助拉出器,利用它通过试验压力将密封件拉到预定密封位置;
(8)在第一和第二个套管悬挂器位置使用相同的密封总成,将悬挂器和井口同时密封锁紧;
(9)只需垂直拉动即可收回密封总成,无需转动;
(10)利用密封总成送入工具可单独下入。
性能测试
Dril-Quip水下井口系统及其组件符合最新行业标准。
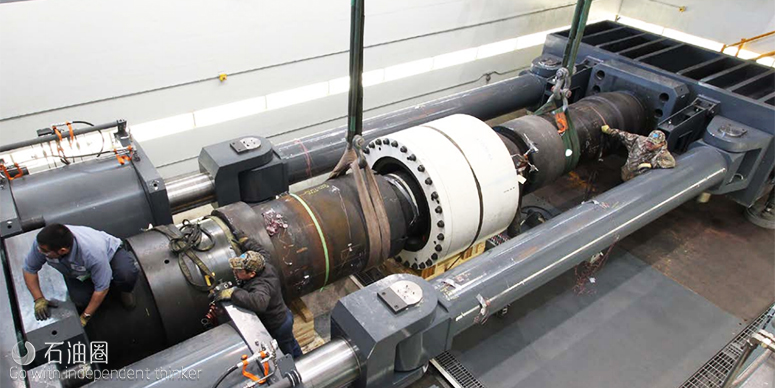
(1)Dril-Quip公司内有经验的应力分析工程师利用最新三维有限元分析软件对井口系统进行评估。
(2)设备的验证和性能测试都通过了最新的API标准。
(3)所有井口组件都经过了性能测试并符合API 17D 第二版和6A PR2第二十版的要求。
(4)所有井口组件都经过了高温高压测试,除了动态密封测试达到行业标准以上要求外,其余满足API 6A 附录 F Group 4要求。
(5)井口系统的整体验证和性能测试确保单个组件达到或超出了系统整体性能要求。
您也有让人挠头的难题需要解决,或是优质技术想要找应用市场吗?如果有的话,欢迎联系小编微信或邮箱,也许能找到一剂良药。
二丫:131-3255-0596;zhanglingyu@fonchan.com
大安:131-3203-1392;lishian@fonchan.com
For English, Please click here (展开/收缩)
Dril-Quip’s BigBore IIe™ Subsea Wellhead System meets the demands of HPHT well environments. The BigBore IIe™ is fully verified and validation tested for structural capacity and high fatigue resistance.
The 18 ¾” nominal bore high-pressure wellhead housing is available with a 15,000 psi and a 20,000 psi working pressure (WP) rating. It is available with a 27″ nominal O.D. and a 30″ nominal O.D. mandrel. The wellhead is sized for mating to surface casing and accommodates 16″ and 18″ supplemental casing hanger systems.
The BigBore IIe Subsea Wellhead System is highly flexible to accommodate a complex casing program that satisfies deep HPHT well objectives.
Features / beneFits unique to the bigbore iie™
•Eliminates the need for extra drilling and production lockdown devices
•Seal Assembly provides 2 million lbs. hanger lockdown capacity to resist thermal and pressure loads
•Significant cost savings by reducing the number of trips
•High load capacity meets requirements of next generation 20 ksi drilling rigs and HPHT well designs
•DXe™ locking profile offers industry best structural capacity and fatigue resistance
•Tested and qualified to normal, extreme and survival loads per API 16A 4th Edition and API 17TR7
•Full scale fatigue tested
•Qualified to 20,000 psi WP and 35° to 350° F per API 6A Appendix F PR2 Group 4, with additional dynamic seal endurance testing
The BigBore IIe Subsea Wellhead System is the next- generation wellhead system designed for HPHT service in deepwater / deep well applications.
•Designed for 15,000 psi (27″) and 20,000 psi (30″) rated working pressure and H2S service between 35° to 350° F with all metal-to-metal sealing
•Supports 8.8 million lbs of end-load (combination of casing weight and test pressure) at the bottom internal landing / load shoulder profile
•Highest available combination of bending, tension and load capacities using the Dril-Quip DXe™ profile
•Utilizes adapters positioned in 22″/23″ surface casing joints for landing 18″ and 16″ supplemental casing hanger systems
•18″ and 16″ casing, casing hangers and testable / retrievable
/ replaceable seal assemblies can pass through 21″ OD drilling riser, 18-3/4″ BOP Stack and BigBore IIe wellhead housing
•All casing hangers and seal assemblies are run, set and
tested on drill pipe running string in a single trip
•
High pressure wellhead actively locked into low pressure wellhead with 2.0 millions lbs of preload to unitize both conductor and surface strings for superior bending load reaction and fatigue resistance
•Utilizes field proven BigBore II-H HPHT metal-to-metal sealing technology
•Incorporates ROV-assisted annulus shutoff monitoring systems for all casing strings cemented back to surface
•Large cement return flow-by areas on all casing hanger systems
•Bit-runnable wear sleeves and wear busings available
•Available with hydrate diversion plate option
•Alternate casing programs accommodated
•All component designs are based on existing BigBore II-H technology and long successful BigBore-II field history
The BigBore IIe Casing Hanger Seal Assembly provides high lockdown capacity and bi-directional high pressure metal- to-metal sealing, suitable for liquid or gas HPHT service.
•Seals in a recessed groove in the wellhead bore, which protects against scoring in the seal bore
•Locks to the wellhead using the outer lock ring to hold down the seal and prevent excessive movement of casing hanger and seal when casing strings are exposed to thermal growth loading
•Locks to casing hanger using the inner lock ring to resist seal movement when seal is exposed to pressure from below
•Seal Assembly outer lock ring as 2,000,000 lbs lockdown capacity
•Successfully tested in gas medium per API 6A PR2 requirements with zero leakage and Group 4 Dynamic seal endurance testing with no elastomers
•Metal-to-Metal sealing element is weight set and pressure energized
•Lower portion of seal has pressure assisted puller element that acts as piston to pull seal into position using test pressure
•Same seal assembly is used on first and second position casing hangers; seal locks to both casing hanger and wellhead
•Can be retrieved with straight vertical pull – no rotation required
•Can be run separately with Seal Assembly Running Tool
Dril-Quip subsea WeLLheaD anD coMPonents are quaLiFieD to the Latest inDustry stanDarDs
•Designs are evaluated with the latest 3-D analytical software tools by experienced Dril-Quip stress engineers.
•The latest API standards are used for both design verification and validation testing.
•Wellhead components have been tested and qualified to API 17D 2nd Edition and 6A PR2 20th Edition requirements.
•High pressure/high temperature wellhead system components have been tested and qualified to API 6A Appendix F Group 4 in addition to dynamic seal testing over and above industry requirements.
•Complete system integrated verification and vali- dation testing helps assure individual component capacities match or exceed the system capacity requirements.
未经允许,不得转载本站任何文章: