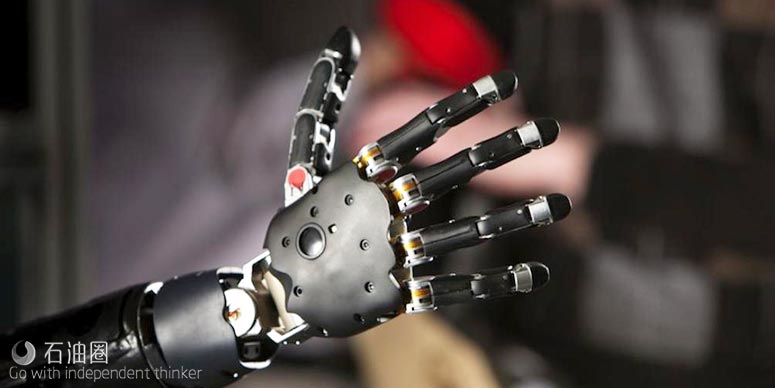
随着作业时间延长,井架工的作业效率也急剧下降,这将会严重影响作业效益。因此,为解放井架工双手,RigArm公司研发了一种新型智能机械臂。
作者 | Alex Endress
编译 | 二丫 白矾
钻井设备厂商RigArm的研究数据显示:钻井作业过程中,最好的井架工排列管柱工作的初期速率约为20秒/根。但这只是精力充沛时的最高速率,随着作业时间延长,作业人员的疲劳程度也相应增加,效率随之下降。RigArm创始人兼负责人Vlad Jorgic说:“假设一个井架工在二层台要排列200根管柱,那么疲劳程度加剧,毫无疑问,工作速率也会迅速下降。”为了实现陆地钻机二层、三层台管柱排布自动化,RigArm正在研发一款智能液压机械臂。“我们的目标是实现管柱排布的自动化,控制人员只要在司钻房内发布指令,机械臂就能完成整个流程。”
机械臂重量仅为2000lb,一般固定在二层台,操作人员在司钻房内发布指令,机械臂在液压控制下就可以完成所有工作,RigArm声称其机械臂的工作速率可以达到20~25根/秒。
为了扫描二层台景象和精确排布管柱,同时避免设备碰撞,机械臂的顶端安装了一个激光探测传感器(LIDAR)和两个超声波传感器。Mr Jorgic说,“传感器寻找到管柱,然后机械臂执行排列操作。管柱的位置并不固定,所以自动导向功能就显得非常重要了。”
LIDAR传感器
超声波传感器在油气行业的应用已经非常普遍,但LIDAR传感器的跨界应用(借鉴于自动化行业)还是首次。LIDAR最早出现在1960年,2000年之后制造业的快速发展带动了LIDAR的广泛应用,2010年之后,自动化行业开始将LIDAR应用到汽车无人驾驶技术的研发中。
Mr Jorgic表示,正是意识到了无人驾驶汽车对路况识别与机械臂对钻杆识别的相似性,RigArm才决定将LIDAR传感器引入到机械臂的设计中。“钻台上的情况复杂多变,我们要随时做好作业不顺利的准备,所以机械臂应该能够快速识别作业条件的变化,并可以迅速做出反应,这就是引入LIDAR的意义。”
RigArm机械臂研发挑战
机械臂研发过程中最大的挑战是对管柱定位算法的优化,Mr Jorgic表示,“目前研发人员正在尝试将算法与机械臂摄像机的三维扫描影像结合在一起,希望以此来解决定位的难题。如果某个传感器的数据与三维影像不一致,那么系统将会自动忽略来自该传感器的错误数据,以保证作业顺利进行。常规机械臂操作程序都是预先植入的,而我们公司要做的则完全不同,我们设计的机械臂具有自主的行为规划功能,它能根据环境变化更新自身程序。”
RigArm机械臂研究进展
目前,RigArm公司的机械臂已经完成了实验室测试,正在北美陆地油田寻找现场测试的机会,预计测试将会持续至少六个月。“我们想在现场油管排列工作中测试机械臂工作性能,稳定性数据对我们来说非常重要,对那些对机械臂的高效性感兴趣但不愿承担相关风险的开发商也同样重要,所以我们必须要证明研发的机械臂具有极好的稳定性。”
Mr Jorgic多次强调:“我们研发的机械臂并不是通过操作杆进行远程控制,因为那样的操作难度太大了。管柱排布的整套工作都可以由我们研发的机械臂自动完成,操作人员只需在司钻房内按下驱动按钮即可。”针对目前还在测试中的机械臂,Mr Jorgic表示该产品有望在今年首次在北美市场投入应用。
您也有让人挠头的难题需要解决,或是优质技术想要找应用市场吗?如果有的话,欢迎联系小编微信或邮箱,也许能找到一剂良药。
二丫:131-3255-0596;zhanglingyu@fonchan.com
For English, Please click here (展开/收缩)
The best derrickmen in the drilling business can rack a stand of pipe at an approximate rate of about 20 seconds per pipe at the start of a tour, according to RigArm, a Calgary-based drilling equipment manufacturer. However, fatigue then begins to set in and can affect performance. “If somebody is standing on top of the rig and needs to move around 200 pipes, the speed will deteriorate over time as they get tired,” Vlad Jorgic, RigArm Co-Founder, President and Software Developer, said. To automate pipe handling on double and triple land rigs, the company is developing the Intelligent Hydraulic Pipe Handling Robotic Arm. “Our goal is for the operator in the control room to be able to tell the machine what to do and allow the machine to complete the entire sequence.”
The hydraulically powered robotic arm, which weighs just under 2,000 lb, would be bolted onto the rig’s racking board and controlled from the driller’s cabin. It can rack a stand of pipe in an estimated 20-25 seconds, according to the company.
The machine will be equipped with a light detection and ranging (LIDAR) sensor and two ultrasonic sensors, located at the tip of the arm, to scan the racking board and precisely locate each stand of pipe. This will help to prevent any equipment collisions. “It senses where the pipe is and then it reaches for it. We have realized that you can’t rely on things being at fixed positions on drilling rigs, so the machine is able to navigate to find the pipe,” Mr Jorgic said.
Ultrasonic sensors are already commonly used in the oil and gas industry, but LIDAR sensors are a relatively new technology being borrowed from the automotive industry. Although LIDAR technology has been available since the 1960s, LIDAR sensors did not become widely used until the manufacturing industry adopted them in the 2000s. Since 2010, the automotive industry also has begun using the sensors to assist in the development of autonomous car prototypes.
Mr Jorgic said his company recognized the similarity between how an autonomous car must react to road conditions and how the robotic arm would need to react in a drilling operation, leading to the adoption of LIDAR sensors for RigArm. “The conditions on drilling rigs are demanding and uncertain. Things move, shake and you can expect that nothing will go as expected, so we needed a system that can understand these changes and quickly adapt on its own, which is what LIDAR technology allows.”
The main challenge in developing the robotic arm has been refining algorithms to allow the arm to properly locate the pipe. Mr Jorgic said the company is experimenting with algorithms that coordinate with cameras mounted onto the robotic arm to scan a three-dimensional image of the environment. If one of the device’s sensor readings doesn’t match the 3D scan, the system’s algorithms will ignore data from the faulty sensor in order to keep the machine operational. “The machine is much different than traditional robotics where everything is preprogrammed. This actually uses motion-planning algorithms that allow it to basically program itself based on changes in the environment.”
The robotic arm has been tested in a lab, and the company is now seeking to test the machine on a North American land rig for at least six months. “We would like to get the machine onto a live well to prove it can work reliably in the field,” he said. “Proving the reliability is very important because we’ve seen mixed feelings from drilling contractors who have worked with these types of machines and have not been successful – which is maybe why we still see a lot of manual pipe handling.”
Mr Jorgic emphasized that this robotic arm is not something that the derrickman would operate remotely with joysticks, which can be challenging to control. The pipe-handling sequence would be carried out autonomously by the robotic arm once the driller pushes a button in his cabin. Pending the field trial, Mr Jorgic said, the robotic arm is expected to become commercial for the North American market by 2017.
未经允许,不得转载本站任何文章: