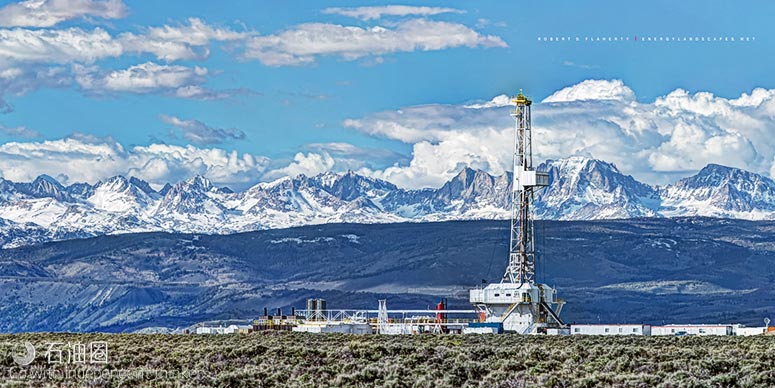
低油价或成油气工业发展拦路虎,却并没有减慢钻井技术发展的速度。
来自 | E&P
编译 | 白小明
根据摩根士丹利的数据,在过去一年中,如果按照头尾净增量进行周化平均的话,美国原油钻机数的增量达到了7.3台/周,超过了2009年页岩油气革命处于爆发期的钻机增速,创下过去30年最高水平。
另一消息称,北美钻井商预将今年的预算提高到840亿美元,预算的大部分增幅将流入二叠纪盆地。Wood Mackenzie Ltd估测,新开支将使今年美国原油产量增加80万桶,约相当于沙特和俄罗斯领导的削减产量计划的44%。另外,美国总统特朗普已经签署行政命令,允许扩大海上石油钻探活动,这对美国石油行业而言无疑是一大利好消息。
油价低迷至今,粗犷式开发已成过去,技术创新悄然转变为油气企业的核心竞争力。
针对页岩气钻井而设计的高规格钻机
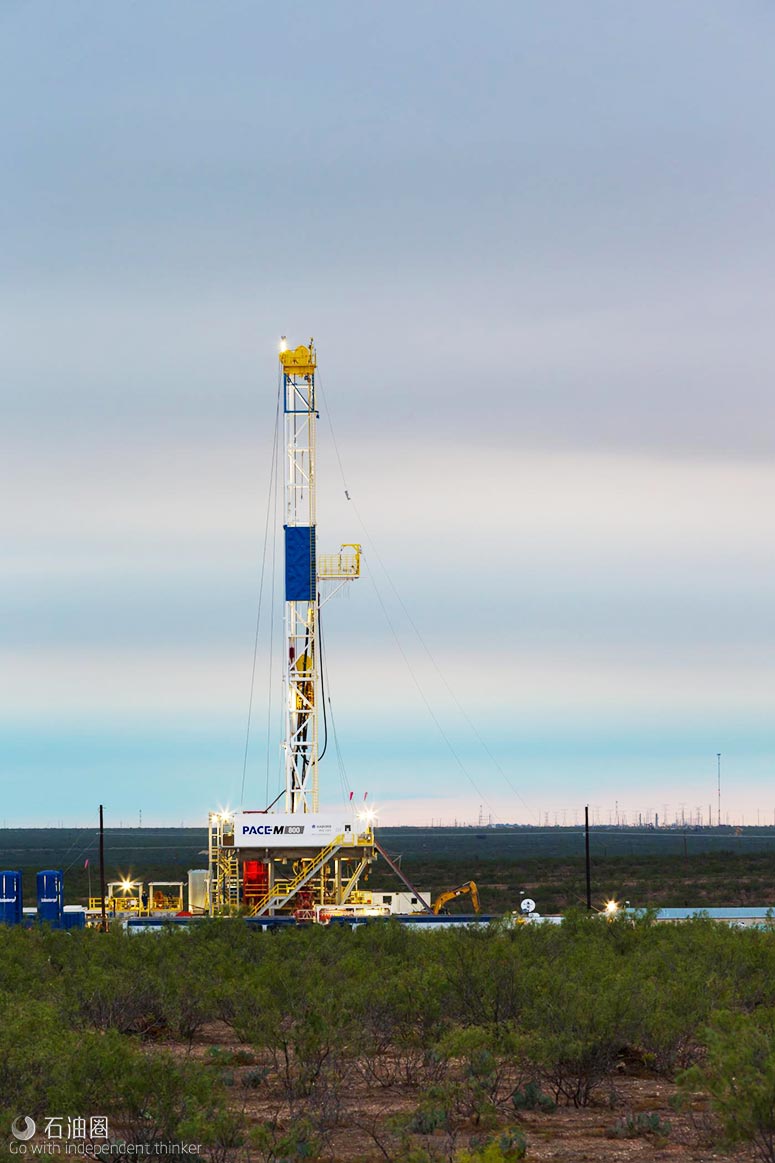
在如今以效果驱动的非常规油气开发环境下,作业公司追求的是花费更少的时间和成本,钻成更高质量、更多产的油气井。传统意义上的钻机通常作为一个整体,各零部件独立自主运转,结果是缺乏整体性,自动化程度低,需要协调许多第三方公司。通过将井下测量数据与地面设备集成到AC电动钻机设计中,同时包含一系列性能优化软件、井位布局和控压钻井解决方案,Nabors公司引入了开展业务的新路径。这种模型降低了HSE风险,提高了性能,从根本上改善了复杂大位移井的经济性。Nabors智能钻机(Smart Rig)的特点是具备高规格能力,包括快速移动最优模块设计,是页岩气环境的理想钻机。这些钻机也包括Rigtelligent基于图标的模块控制操作系统,可以实现日常自动化钻井程序,更精确且更利于连续操作。专有的性能优化软件可用于进一步提高效率、ROP和精确执行钻井设计。Nabors的钻机可以进行定向和控压钻井,将相关软硬件均集成到了钻机基础设备中,减少了起、放钻机的要求,提高了可靠性,简化了操作。
无粘土聚合物钻井液系统带来良好应用效果
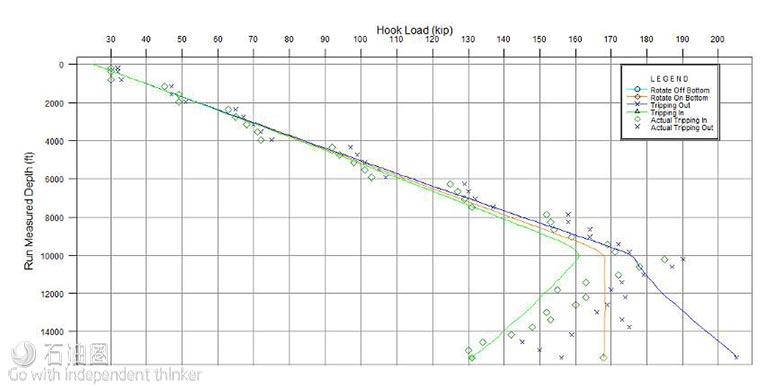
应用于Permian 盆地井的Evolution摩擦系数分析,模拟摩擦系数0.22
Newpark Resource公司的Evolution无粘土聚合物钻井液系统,是一款高性能水基钻井液(HPWBF)系统,结合了一种高效聚合物增粘剂/页岩稳定剂和一种有效的钻井性能增强剂。一家作业公司在德克萨斯州Angelina和Jasper县钻一口高温高压勘探井时,采用了HPWBF,井垂深6096m。采用Evolution系统成功完成钻井作业,测井顺利。最终井温超过200℃,密度1.64g/cm3。相比Permian盆地的其他研究应用,使用Evolution将钻井时间从14天减少到了7天,用HSE友好型的HPWBF替换传统的柴油基钻井液,获得了等价或者更好的润滑性,降低了总成本。该系统具备热稳定性特点,可以降低摩阻,提高ROP,形成的井眼不缩径,钻井、测井和下套管过程中几乎无风险。
新型电机控制驱动系统延长正常工作时间
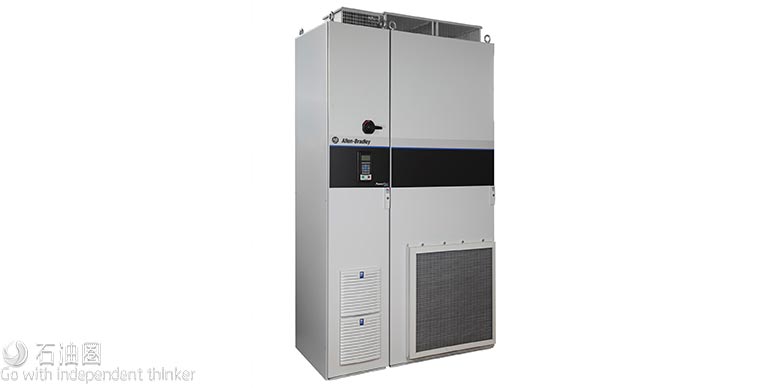
为了帮助油气生产商在需求旺盛的页岩油气应用过程中减少能源消耗成本,提高机器运行时间,Rockwell自动化公司发布了一款新的动力系统,Allen-Bradley PowerFlex 755T驱动器。这种驱动器带来一种低谐波主动前端结构,帮助减少配电线的相关问题。该设备还具备高性能变速控制特性,非常适用于顶驱、泥浆泵和绞车,提供精确的电机控制,占地面积小。该驱动系统的总线系统配置,减少了所需配件数量,减少了像多井模块化作业应用所需的井场面积,可以将多套系统安装在同一个集中位置。低谐波主动前端结构、高性能控制系统,以及共享DC总线结构的结合,减少了设备的占地面积,使755T非常适用于页岩油气各种作业,如钻机、泵送、人工举升系统和多井模块化作业。
陀螺磁力测距
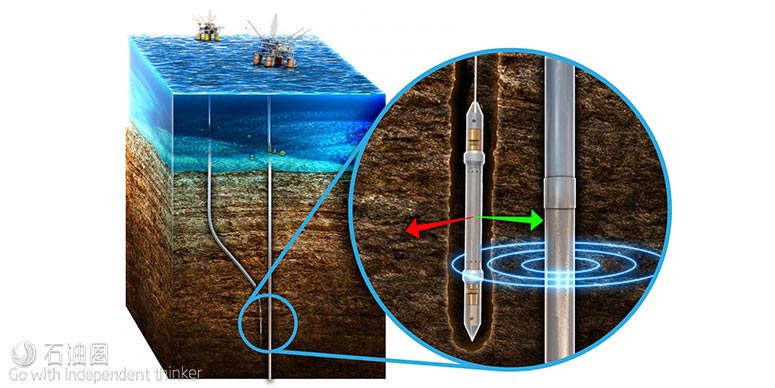
钻救援井通常需要进行磁力测距作业。在多数情况下,主动磁力测距是首选解决方案。这种工具可以确定工具自身内部参考轴与目标的距离和方向。在无磁性干扰的情况下,可以使用方位磁性工具面,将内部参考轴与地球东北纵坐标对齐。然而,当测距工具与目标井位置靠近时,磁性方位工具面参考就会出问题。为了保证使用磁性参考继续钻进,常规的行业实践做法是分别下入陀螺测量和测距工具。然而,由于对高边参考和方位的定义通常不理想,如果井接近垂直的话,这种方面可能不奏效。解决这个问题的另一个经过证实的方法,是将陀螺和测距系统结合在一个工具内,并使用方位陀螺工具面(而不是方位磁性或者高边重力工具面),在世界坐标框架下,定义测距探管参考轴。科学钻井国际公司同时拥有陀螺和测距系统,在钻救援井时结合使用,可以在井间参考方面带来巨大的效率提升。
针对长分支段设计的尾管系统
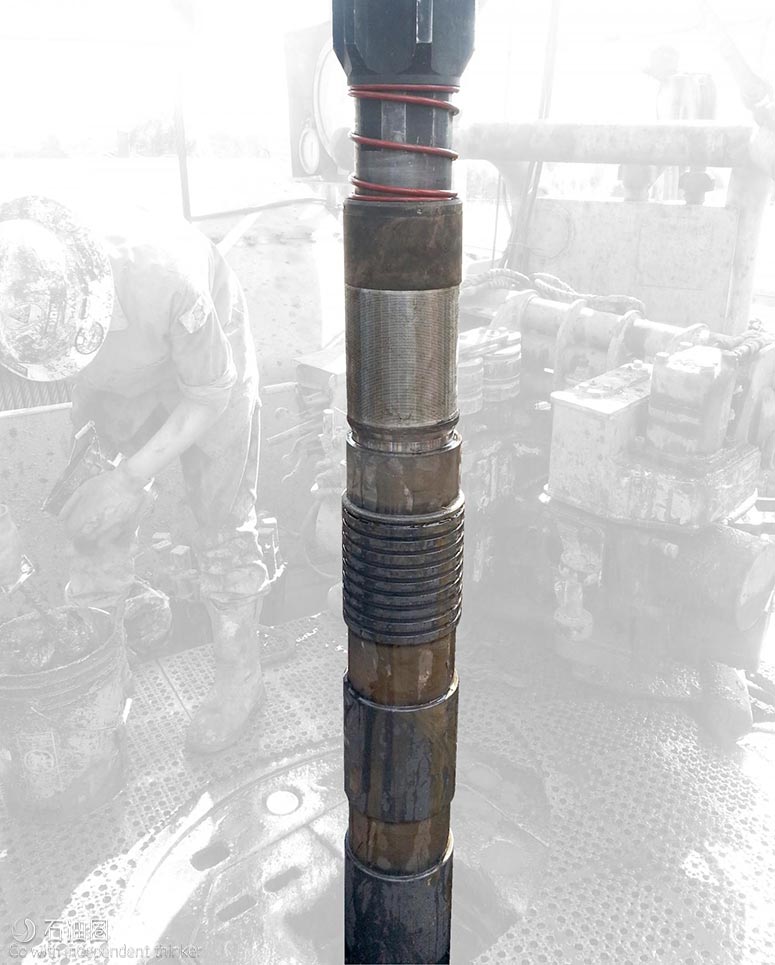
对于页岩气钻井而言,长分支段意味着提高产量。作为长分支井建井设计的一部分,通常在某一分支会下入尾管。在这种情况下,往往需要提高送入工具的扭矩和抗压强度,以顺利将尾管下至预定井深。Seminole油服公司的Powerscrew尾管系统,便用于满足这种需求。系统的坐封工具在坐封尾管顶时,同时使用下压力和扭矩。最终,在下入过程中,这些载荷可以轻松传递到尾管,无需特殊的适配器。
长分支段的另一个挑战是尾管部署过程中需要旋转和循环。该系统可以旋转和循环,克服了当今建井过程中的挑战。另外,系统先进化的可扩展设计也提高了稳定性。如今,作业公司不再需要悬挂尾管。通过下压力和扭矩将尾管下到分支段后,然后将其与中间套管啮合即可。
井下自动化技术提高非常规钻井ROP
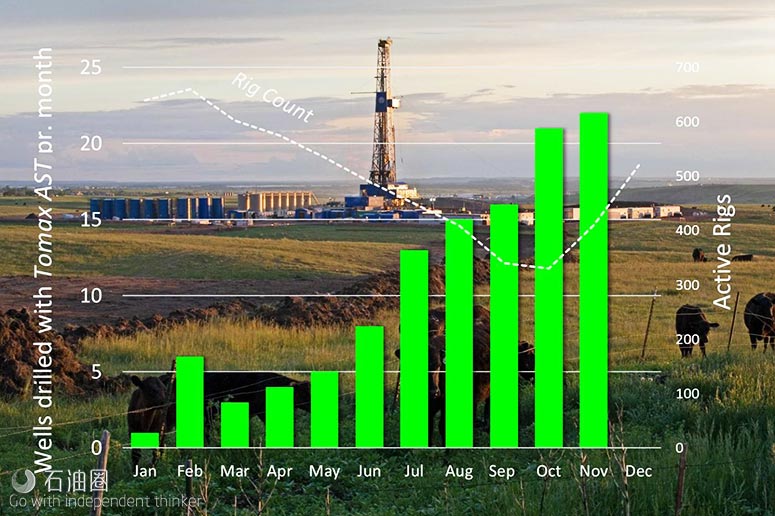
AST效率的改善降低了热损失和震动,延长了井下电子元件和钻头的整体服务寿命
当桶油成本逐渐成为油气公司关注的焦点,钻井公司必须想办法提高生产力。Tomax公司的防粘卡工具(Anti Stick-slip Tool)AST应运而生。常规钻柱因弹簧效应在向钻头传递动力时,容易引起严重的扭曲。因为钻头也压在其将破损的岩石表面,因此如果钻压传递不稳定,很容易使钻头掉齿。AST可以在5/100秒的时间内响应这种扭矩变化,调节轴向载荷,维持稳定的扭向载荷和破岩过程。AST连续的载荷也可以减小冲击载荷和防止钻头切削齿的提前泥包。
新PDC钻头提高恶劣环境钻井性能
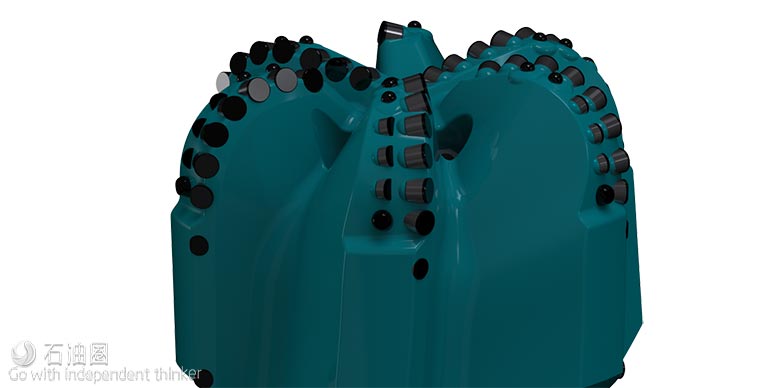
目前,作业公司已经可以通过井底钻具组合,向井下传递更大的动力,他们正在寻求提高钻头的性能。Ulterra公司新的Xtreme Parameter(XP)PDC钻头,可以通过强化钻井参数,如钻压和使用高扭矩马达,来获得更好的钻井效果。在过去18-24个月里,公司重新设计了钻柱组合和井下工具等钻井组件,以增加功率输出。Ulterra开发和测试了钻头理念。这些经过证实的理念一起被加入到了XP产品线。通过重新设计本体和刀翼几何尺寸,强化切削齿,使用优化的材料选择流程,XP系列钻头产品整体性能得到提升。Ulterra即将发布带XP系列PDC切削齿的新设计的钻头。通过材料优化和测试流程,经证实,相比之前的齿,XP切削齿损坏小,产生的力更大,提高了近20%的抗冲击性。通过新的XP产品线,Ulterra可以延长恶劣钻井环境下PDC钻头的寿命和可靠性,而不牺牲其他方面的性能。油气钻井技术将继续高速发展。
您也有让人挠头的难题需要解决,或是优质技术想要找应用市场吗?如果有的话,欢迎联系小编微信或邮箱,也许能找到一剂良药。
柠檬:186-2292-2332;weiyameng@fonchan.com
二丫:131-3255-0596;zhanglingyu@fonchan.com
For English, Please click here (展开/收缩)
HIGH-SPECIFICATION RIG FLEET DESIGNED FOR SHALE DRILLING
In today’s performance-driven unconventional environments, operators are seeking new ways to deliver a higher quality and more productive wellbore in fewer days and at a lower cost. Traditionally, rigs operate as an independent machine with all equipment operating autonomously, resulting in a lack of integration, minimal automation and coordination of many third parties. By integrating downhole measurements with surface equipment into AC electrical rig designs and with an extensive portfolio of performance optimization software, wellbore placement and managed-pressure drilling solutions, Nabors has introduced a new way of doing business. This model reduces HSE exposure, increases performance and ultimately improves the economics of challenging extended-lateral wells. Nabors SmartRig fleet features high-specification capabilities, including fast-walking pad-optimal designs that are ideal for shale environments. These rigs also include the Rigtelligent icon-based modular controls operating system, which automates routine drilling procedures and enables more precise and consistent operations. Proprietary performance optimization software can be applied to further improve efficiencies, ROP and precise execution of the well plan. Nabors’ rigs can be directionaland managed-pressure ready, with all necessary software and hardware integrated into the rig infrastructure, reducing rigup and rigdown requirements, increasing reliability and streamlining operations.
CLAY-FREE POLYMER SYSTEM DELIVERS RESULTS
Newpark Resource’s Evolution clay-free polymer system is a high-performance water-based drilling fluid (HPWBF) system that combines a rugged polymeric viscosifier/ shale stabilizer with an effective drilling performance enhancer. An operator sought a HPWBF for a well in Texas’ Angelina and Jasper counties for exploratory HP/HT drilling up to 6,096 m (20,000 ft) total vertical depth. The interval was successfully drilled using the Evolution system, with all logging runs executed successfully. The final temperatures were in excess of 200 C (392 F), with densities of 13.7 lb/gal. In comparative studies in the Permian, using Evolution shortened drilling time from 14 days to seven days and replaced traditional diesel oil-based mud with an HSEfriendly HPWBF while providing equivalent or better lubricity and reduced overall cost. The system is designed to provide thermal stability; reduced torque and drag; high ROP; near-gauge hole; and virtually trouble-free drilling, logging and running casing to total depth.
NEW MOTOR CONTROL DRIVE SYSTEM DELIVERS INCREASED UPTIME
To help oil and gas producers reduce energy costs and increase machine uptime for assets running in high-demand shale applications, Rockwell Automation has released a new drive tool, the Allen-Bradley PowerFlex 755T drive. This drive provides a low-harmonic active front-end structure that helps reduce problems in power distribution lines. It also features a high-performance variable-speed control that’s ideal for top drives, mud pumps and drawworks— offering precise motor control in a compact footprint. The drive’s common-bus system configuration reduces the number of components required and minimizes the footprint for applications like multiwell pad operations, where several drives can be housed in a central location. The combination of a low-harmonic active front-end structure, high-performance control and the ability to share a common DC bus structure to reduce footprint make the 755T well-suited for shale oil and gas applications like drilling rigs, pumping applications, artificial lift systems and multiwell pad operations.
GYRO-REFERENCED MAGNETIC RANGING
Drilling a relief well often involves magnetic ranging operations. In most cases, active magnetic ranging is the preferred solution. Such tools can define the distance and direction to the target with respect to their own inner reference axis. In a magnetically clean environment, the azimuthal magnetic toolface could be used to align this inner reference axis with the world’s northeast vertical coordinates. However, when the ranging tool is in close proximity to the target well, magnetic azimuthal toolface referencing is problematic. To make it possible to drill ahead in the presence of this magnetic interference, the normal industry practice is to run a gyro survey and ranging tool separately in a well. However, due to poorly defined highside reference and azimuth, this may not be sufficient if the wells are near-vertical. A proven workaround to this problem is to combine and align both gyro and ranging systems in one tool string and use azimuthal gyro toolface (instead of the azimuthal magnetic or highside gravity toolface) to define the position of the ranging probe reference axis within the world coordinate frame. Scientific Drilling International owns both gyro and ranging technologies which, when combined and deployed during relief well operations, yield dramatic gains in efficiency in well-to-well referencing.
LINER SYSTEM DESIGNED FOR LONG LATERALS
Longer laterals equate to increased production for shale drillers. As part of a well construction design for long laterals, a liner often is installed in one of these laterals. This installation typically requires increased torsional and compressive strength from the running tool to get to total depth. The Powerscrew Liner System from Seminole Services was designed to effectively address this demand. The system’s setting tool uses both compression and torsion while setting the liner top. As a result, these loads transfer more easily to the liner during run-in without the need for a special adapter. Another challenge presented by long laterals is the need to rotate and circulate during liner deployment. The system meets this challenge by providing the rotation and circulation necessary for today’s well construction. In addition, the system’s modern expandable design delivers a step change in reliability. Today’s operators do not hang liners. Liners are worked into the lateral section with compression and torque and then set to engage the intermediate casing.
DOWNHOLE AUTOMATION IMPROVES UNCONVENTIONAL ROP
When cost per barrel becomes an issue, drillers must grab what is available to improve productivity. The Tomax Anti Stick-slip Tool (AST) represents an interesting development in this respect. The spring characteristics of a regular drillstring tend to cause significant distortions in the delivery of power to the bit. Because the bit also is resting on the same surface it is about to remove, it will easily lose its cut when the transfer of weight gets erratic. The AST responds to torsional change within a response time of 5?100 of a second and regulates the axial loading to maintain a steady torsional loading and cut. The continuous loading by the AST also reduces the risk of impact loading and premature spalling of the bits’ cutting edges.
NEW PDC BIT DELIVERS INCREASED PERFORMANCE IN HARSH ENVIRONMENTS
Operators have remarkably increased the energy they run through their bottomhole assemblies seeking higher performance out of their drillbits. Ulterra’s new XtremeParameter (XP) polycrystalline diamond compact (PDC) bits are built for the operator seeking greater performance through increased drilling parameters like weight on bit and the use of high-torque motors. As rig components, drillstrings and downhole tools have been redesigned to increase output over the last 18 to 24 months, Ulterra was developing and testing bit concepts to account for them. These now-proven concepts were brought together into the XP product line. By redesigning body and blade geometry, implementing cutter reinforcement, and using an optimized material selection process, the XP line of drillbits has improved. Ulterra is releasing its XP line of PDC cutters with the redesign of the drillbit. Through a process of material optimization and testing, XP cutters are proven to take greater force with less damage compared to previous generations, improving impact resistance by nearly 20%. With this new XP product line Ulterra is able to extend the life and reliability of PDC bits in the harshest drilling conditions without sacrificing performance in other areas. Oil and gas drilling will keep evolving at an ever-expanding rate.
未经允许,不得转载本站任何文章: