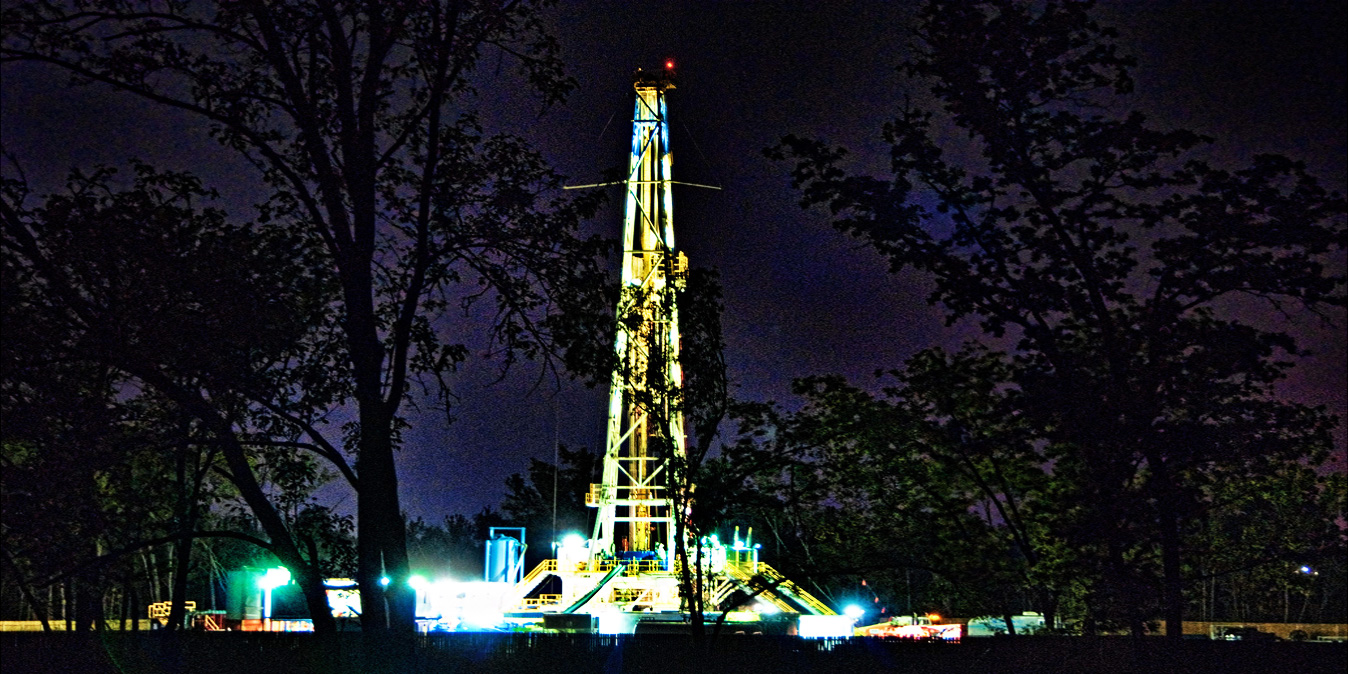
我们知道,如果不采取适当的水力压裂增产措施,致密气藏就无法进行有效的开采。因此,致密气藏钻完井过程的关键就是保证后期能够设计和实施最优的压裂增产措施。
致密气藏钻井时,最重要的就是钻取一个规则的井眼,因此,一般来说,致密气藏钻井需要采用平衡钻井或者过平衡钻井方式。其实,某些情况下,只要井眼保持规则,空气钻井或者欠平衡钻井效果会最佳。
如果井眼比较规则,那我们就可以进行裸眼测井,获得准确的测井数据,从而对地层进行合理的评价,进行最适完井设计。如果井眼被冲蚀或者是不规则的,测井就会变得非常困难或是难以获得精确的数据,并且难以识别干气储层。
如果井眼较为规则,那么生产套管的固井质量就会比被冲蚀井眼的固井质量好的多。并且,对于致密气藏这种必须进行压裂增产的多产层油藏来说,固井质量是尤为重要的。
致密气藏欠平衡钻井
有些钻井专家建议致密气藏采用欠平衡钻井的方式钻进,主要是因为:
1.欠平衡钻井的钻进速度更快;石油圈原创www.oilsns.com
2.地层被钻井液污染的程度最小;石油圈原创www.oilsns.com
3.由于地层渗透率非常低,因此,井喷的可能性非常小。
然而,如果能够保持井眼规则,就可以采用欠平衡钻井。但是,如果井眼被冲蚀,无法进行正常的储层评估,或者无法保证固井质量,此时,钻进速度就没有那么重要了。在致密气藏中,储层损害并不是一个需要着重考虑的因素。因此,钻井过程中是否对近井地带储层造成损害并不重要。在进行致密气开发时,我们一般都会使用多个泵车和泵组来进行压裂,水力压裂不会对近井地带储层造成伤害。石油圈原创www.oilsns.com
致密气藏完井方案
致密气井理想的完井方案是用最低的成本获得最大的产气量,其中完井成本包括了最初的完井成本和后期的作业成本。也就是说,经验丰富的完井工程师们会尝试提出一种全能的完井方案,且对作业者来说也是成本最低的方案。
完井设计过程中,我们通常会考虑产层的数量,这些产层被垂向的隔层分开。不同产层能否视为同一油藏一起进行增产处理,取决于压裂裂缝能否将这么多的产层连通起来。如果一个产层与其他产层之间被细粉砂岩或者页岩层分开,就需要用模型模拟来判断裂缝能否连通所有的产层。
如果一条裂缝可实现多产层增产合采,并且多层合采时不会造成储层伤害,那么就可以把多产层当做一个储层来进行完井。一般情况下,在干气藏中,多层合采不会损害储层。事实上,多层合采时的产气量会更大,因为多层合采会比分层开采时的枯竭压力更低。
如果一层较厚(大于等于50英尺)的页岩层能够隔开两个或者多个产层,并且其有足够的地应力来抵抗垂直裂缝的扩展作用,那么工程师们在完井设计和实施增产措施时就应该考虑如何才能制造出更多的裂缝。在这种情况下,若要对所有储层进行增产,就需要采用压裂转向技术。
致密气藏油管设计
当产气速率下降时,油管设计的两个关键点就是管具能够配合完成最佳压裂方案和具备处理井筒积液的能力。我们必须解决这两个难题,才能达到最佳完井设计。前面提过,如果水力压裂不成功,那么致密气井的钻完井和开发生产都不能获得理想的经济效益。总的来说,产量越高,压裂就越成功,因此为了注入大量的压裂液,我们倾向于使用大直径油管。
当压裂完成,井投产以后,产气量就开始降低。所有的井,甚至干气井,都会产生凝析液或水。无论产液量是多或少,最终都会形成井筒积液,产气量也会随之下降。由于井筒积液量会影响产气速率,因此为了解决井筒积液的问题,我们需要使用小直径油管。
因此,矛盾就产生了,即我们需要较粗的油管来满足压裂的需要,同时,我们又需要较细的油管来解决井筒积液的问题。由于不同油田的特点不同,因此他们的选择也各不相同。
Gidley曾经提出,解决这个矛盾需要考虑许多因素,计算方法也有很多。在某些情况下,当油藏压力等于或低于正常压力时,我们可以进行套管压裂,压裂后下入小油管进行完井。但是,如果油藏压力高于正常压力,我们可能就需要在低于最优排量的排量下进行油管压裂。
由于套管和油管设计以及优化油管设计这两方面的内容非常复杂,很难在这里详细完整的阐述清楚。但是,完井工程师们应尽量在气井开钻之前,就对其压裂和完井进行设计。
如果完井工程师认为需要使用某种尺寸的套管或者油管来实施最优的完井方案,那么完井工程师就应该将这个信息反映给钻井工程师。然后钻井工程师再设计使用合适尺寸的钻头和套管,以满足完井工程师的需求。如果井已经开钻,生产套管已经下入并固定,如果此时再要求采用更粗的套管以实现更高质量的完井作业,那么为时已晚。
同样的道理,在井开钻之前也应该完成压裂设计方案,合理估计造缝压力需要考虑以下几个因素:
1.套管尺寸;石油圈原创www.oilsns.com
2.压裂排量;石油圈原创www.oilsns.com
3.压裂液摩阻和密度。石油圈原创www.oilsns.com
各种完井情况下,压裂作业的最大施工压力都是一个非常重要的数据。钻井工程师可以根据这一信息来选择合理尺寸、重量级和钢级的套管。如果由于套管无法承受施工压力,而改变压裂液的泵入量或粘度,那么此次压裂作业通常是以失败而告终。因此,在开钻之前,就应该把这些问题考虑清楚,对套管进行合理设计,防止这些问题的发生,使作业者顺利实施高质量的压裂作业。
致密气藏射孔需考虑因素
完井和压裂作业中最难的一个步骤就是选择怎样的射孔方式。可以说,射孔作业没有简单的解决方案,最佳的射孔方案会因油藏性质的不同而存在差异。其中,有两点是比较重要的,第一就是确定产层的数量和压裂的级数,第二就是确定地应力的各向异性以及是否存在天然裂缝。
最近在石油行业的文献资料中,有一个压裂相关的话题频繁提及,那就是“近井扭曲效应”,即:当在井筒附近产生多条裂缝时,就会产生近井裂缝的扭曲。通常,产生多条裂缝的原因是有天然裂缝存在,或是因为长射孔段上有方向各异、数量较多的孔眼。
当近井地带产生多条裂缝时,这些裂缝的缝宽都会比单一裂缝的缝宽窄,当向这些较窄的裂缝中泵入支撑剂时就会出现问题。有很多这样的案例,当发生近井扭曲时,近井地带就会随之出现砂堵现象。
有许多方法可减弱近井扭曲效应。最佳的方法可能就是减小射孔段的长度,并且将射孔相位角设为180度,与裂缝扩展方向保持一致(对于垂直裂缝来说,裂缝扩展方向垂直于最小水平主应力方向)。
对致密气井进行射孔时,最关键的一点就是:射孔作业要有利于实施最佳的压裂方案。因此,完井工程师必须选择正确的层位,并在这些层位进行射孔,从而能够在多级压裂中使用转向压裂技术。
在有关射孔的很多文章中,对“每英尺应射多少孔才能保证生产指数不会因为射孔数量太少而减小”这一问题进行了分析讨论。实际上,在需要压裂的致密气井中,不需要过多的考虑每英尺的射孔数,更重要的是,射孔数一定要与压裂液的泵入速度相匹配。石油圈原创www.oilsns.com
经验告诉我们,合理的射孔数量应满足每个孔眼处的排量为0.25~0.5桶/分钟。举个例子,如果压裂液的泵入量为20桶/分钟,那么就应该考虑在射孔层位(也就是裂缝起裂的位置)下入40~80个孔眼的射孔枪。
总之,射孔越紧密越好,并且射孔相位角应该为180度,且应沿着地层的最大水平主应力,这对于水力压裂来说是最好的方案。而最坏的方案就是在很长的距离内每英尺射4孔或者6孔。当很长的距离内有比较多的孔眼时,工程师们就会很难控制裂缝的起裂位置,也会增加生成多条裂缝的可能性。
译者/王凯 编辑/魏亚蒙
The definitio
n of a tight gas reservoir is that the reservoir does not produce at commercial gas flow rates, or recover commercial volumes of natural gas, unless a hydraulic-fracture treatment is properly designed and pumped. As such, the entire drilling and completion procedures should focus on making sure the optimum fracture treatment can be designed and pumped in the field.
When drilling a tight gas well, the most important aspect of the drilling operation is to drill a gauge hole. Many times this means the well should be drilled at a balanced mud weight or slightly overbalanced. In other cases, air drilling or underbalanced drilling works best, as long as the hole remains in gauge. If a gauge hole is drilled, we can run openhole logs and obtain valid data that are required to properly evaluate the formation and to design the completion. If the hole is washed out and rugose, the logs are difficult or impossible to accurately evaluate, and the net gas pay is difficult to identify. Also, if the borehole is in gauge, the chances of obtaining a satisfactory primary cement job on the production casing increase when compared to trying to cement casing in a washed-out borehole. Obtaining a good primary cement job is extremely important when completing a well in a multilayered reservoir that must be fracture treated.
Underbalanced drilling
Some drilling personnel want to drill underbalanced in tight gas reservoirs because:
The penetration rate is faster
Formation invasion of mud filtrate is minimized
There is little chance of a gas kick because of the low permeability nature of the formations
However, underbalanced drilling is only acceptable if a gauge hole can be maintained. Speed to reach total depth is not important if the borehole is washed out and we cannot properly evaluate the reservoir layers or obtain an adequate primary cement job. Also, formation damage is not an important consideration in tight gas reservoirs. It does not matter whether or not the near-wellbore formation has been damaged during drilling. In every case, we still use multiple pump trucks and pump rather large fracture treatments. The hydraulic fracture breaks through any near-wellbore damage.
Completion strategy
The ideal completion is the one that produces the most gas for the lowest cost—considering both the initial completion cost and the subsequent operating costs. This definition implies that a prudent engineer will attempt to provide a functional completion for many years to come at the lowest possible cost to the operator.
Of concern in the design of the completion is always the number of producing zones that are separated in the reservoir by vertical flow barrier layers. To determine whether different producing intervals should actually be treated as a single reservoir, one must first determine if these various intervals are all connected by a single hydraulic fracture. If a particular zone is separated from another pay zone by a thin silt or shale layer with little in-situ stress contrast among the layers, one can use a model to determine if all the zones can be connected by a single hydraulic fracture. If a single fracture treatment is used to stimulate multiple layers, and no reservoir damage occurs by commingling the different zones, the well should be completed as if all the layers are actually a single reservoir. Normally, in dry gas reservoirs, no reservoir damage occurs by commingling zones. In fact, it is likely that more gas will be recovered by producing all the layers commingled because the abandonment pressure is lower at any given economic limit when the zones are commingled vs. producing the zones one at a time.
If two or more productive intervals are separated by a thick, clean shale (say, 50 ft or more) and this shale has enough in-situ stress contrast to be a barrier to vertical fracture growth, the design engineer might need to design the completion and stimulation treatments to consider the fact that multiple hydraulic fractures will be created. In such cases, fracture treatment diverting techniques must be used to properly stimulate all producing intervals. More information concerning completion design in multilayered reservoirs is available in the technical literature.
Tubular concerns
The two main concerns with tubular design are pumping the optimum fracture treatment and liquid loading as the gas flow rate declines. These two concerns must be balanced to achieve the optimum well completion. As previously stated, a tight gas well is uneconomic to drill, complete, and produce unless a successful fracture treatment is designed and pumped. In general, fracture treatments are more successful when pumped at higher injection rates. Therefore, to pump a treatment at a high injection rate, we normally like to use large tubulars.
Once the treatment is pumped and the well is put on production, the gas flow rate begins to decline. All wells, even dry gas wells, produce liquids in the form of condensate or water. Regardless of how little liquid is produced, the well eventually loads up with liquids as the flow rate declines. Liquid loading is a function of gas velocity. Therefore, to minimize liquid-loading problems, we must use small tubing.
Thus, the dilemma: we need large tubulars to pump the fracture treatment and small tubulars to minimize liquid loading. The solutions to this dilemma can be as varied as the number of fields in which we work. Many considerations and computational techniques needed to solve these problems are presented in Gidley.[1] In some cases, when the reservoir pressure is at or below normal pressure, we can fracture treat the formation down casing, then run small tubing after the treatment to produce the well. If the reservoir is geopressured, we might have to fracture treat the well down tubing at injection rates less than optimum.
The topic of how to design casing and tubing and how to design the optimum tubular configuration in a tight gas well is too large to deal with completely in this chapter. The completion engineer should, however, try to design the fracture treatment and the completion prior to spudding the well. If, during the design, the engineer determines that a certain size casing or a certain size tubing is required to implement an optimal design, the completion engineer should provide that feedback to the drilling engineer. The drilling engineer can then design the bit program and casing program to accommodate the needs of the completion engineer. Once the hole is drilled and the production casing is set and cemented, it is too late to redesign the completion if you discover you needed larger casing to implement the optimum completion.
In the same manner, the fracture treatment should be designed prior to spudding the well, so a reasonable estimate of fracture treatment pressures, from bottomhole to the surface, can be estimated as a function of:
The casing size
The injection rate
The fracture fluid friction and density properties
It is very important to know the maximum injection pressure during the fracture treatment for a variety of completion scenarios. The drilling engineer can use that information to select the correct size, weight, and grade of casing. A fracture treatment is usually not successful if the injection rate or fluid viscosity is compromised when the casing cannot withstand the desired injection pressure. Again, working the problem prior to spudding and designing the casing correctly can prevent problems and allow the service company to actually pump the optimum fracture treatment.
Perforating concerns
Perhaps the least understood part of well completions and hydraulic fracturing revolves around how to perforate a well. Again, there is no simple solution, and the best perforating scheme varies depending on the specific reservoir situation. Two factors seem to be very important. First, the number of layers and the number of fracture treatment stages affect how we perforate the well. Second, the in-situ stress anisotropy plus the presence or lack of natural fractures have a strong bearing on how we perforate the well.
A problem associated with hydraulic fracture treatment problems has been recently identified in the petroleum literature as “near-wellbore tortuosity.”[3] Near-wellbore tortuosity occurs when multiple hydraulic fractures are created near the wellbore. These multiple hydraulic fractures are usually caused by the presence of natural fractures or the fact that too many perforations are shot in multiple directions over a long, perforated interval. When multiple fractures occur near the wellbore, each fracture is narrower than a single fracture, and problems occur when trying to pump the propping agent down the narrow fractures. In many cases, a near-wellbore screenout occurs when near-wellbore tortuosity problems occur.
There are several ways to minimize near-wellbore tortuosity problems. The best solution might be to minimize the length of the perforated interval and to orient the perforations 180° in the same direction that the fracture propagates (which is perpendicular to the minimum principle horizontal stress, for a vertical fracture).
Again, the main concern when perforating a tight gas well is to perforate in such a way that the optimum fracture treatment(s) can be successfully pumped. The completion engineer must be concerned with choosing the correct zones and perforating those zones to accommodate any diversion techniques that will be used in multistaged fracture treatments.
In the perforating literature, there are many papers discussing how many holes are needed per foot of casing so that the productivity index is not reduced because of too few holes. In a tight gas well that is fracture treated, the number of holes per foot of casing is really not much of a consideration. More importantly, the number of holes with respect to the fracture treatment injection rate should control the perforation operation. A good rule of thumb is that the number of holes should be such that the injection rate per hole is between 0.25 and 0.5 barrels per minute per perforation. For example, if you plan to pump the fracture treatment at 20 barrels per minute, then you should consider putting between 40 and 80 holes in the pipe in the zone where you want the fracture to initiate. In general, the more compact the perforated interval the better, and perforations oriented 180° in the direction of maximum horizontal stress provide the best situation for hydraulic fracturing. The worst situation is to shoot 4 or 6 shots per foot over a long interval. When too many holes are shot over too long an interval, the engineer loses control of where the fracture initiates, and the chances of creating multiple fractures at the wellbore increases substantially.
未经允许,不得转载本站任何文章:
-
- 柠檬
-
石油圈认证作者
- 毕业于中国石油大学(华东),油气井工程硕士,长期聚焦国内外石油行业前沿技术装备信息,具有数十万字技术文献翻译经验。如需获取更多技术资料,请联系我们。