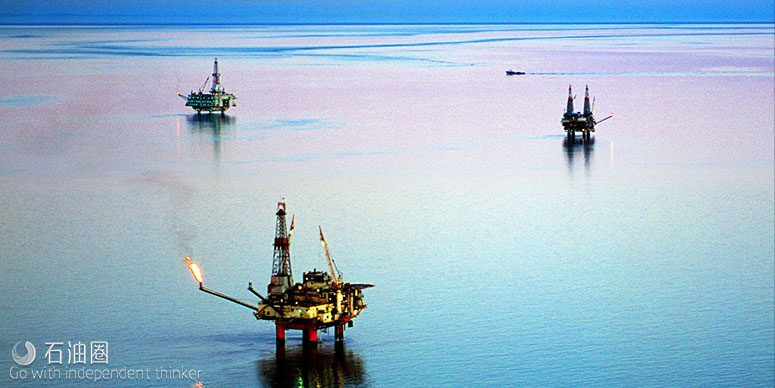
HydrOcean为连续介质力学数值技术提供了全面的、高保真的、全功能的海上平台建模工业可行的CFD模拟方法。
来自 | Marine Link
编译 | 王萌
海上油气平台的CFD模拟用于预测作用在平台上部结构上的最大风荷载(即平台的上半部分、海平面以上及浪溅区以外的部分,包括采油区、住宿区和各种钻井设备)。风荷载在特定海域往往是非常重要的,可用作波浪和海流负载设计平台的系泊结构。传统来讲,平台顶部的几何形状过于复杂,无法高度拟合,CFD模拟依赖于简化的去功能模型。使用低保真的CFD模拟,意味着模拟结果还需通过高成本和劳动密集的装配工作以及风洞中的物理模型测试进行验证和改进。
但是最近在道达尔资助的研发项目中,在海洋工程公司DORIS Engineering的工程管理和额外资助下,法国船级社附属的数字航空和流体力学领域专家—HydrOcean公司,成功地将平台上部模块的CAD模型进行了完全细化。使用这种高保真CFD模型,HydrOcean研究了风的多个角度对平台的影响,将风洞实验数据与风力发电能力的波浪盆测试相匹配,成本占比控制在10%以内,多数情况下为3~5%。
该项目由“油气勘探和生产协作与创新技术计划”(CITEPH)提供资金,这是法国的一项国家计划,协助对油气及相关能源行业创新研发项目的进行私人赞助。这是两个CITEPH项目中的第二个,HydrOcean从道达尔获得资金,以开发和验证使用数值CFD技术,特别是使用连续介质力学数值技术(STAR-CCM+),用于计算海上平台上的风荷载。
CITEPH风荷载项目一
CITEPH风荷载项目一已于2013年完成,在该项目中,HydrOcean使用CFD来重现位于西非的大型FPSO机组中进行的风洞实验结果。 该项目成功验证了CFD在上述场合的应用,还能对实验结果的偏差进行识别,如试验限制、尺度效应和边界层效应。
CITEPH风荷载项目二
在CFD经过验证后,CITEPH风荷载项目二旨在推动CFD的应用达到极限。该项目仍由HydrOcean公司进行管理,需要寻找增加风洞和波盆测试中所使用的物理模型和数字化CFD模型保真度的方法。
在评估海上结构的风荷载物理实验中,海上平台的CAD详细模型在创建测试物理模型的过程中往往被大大简化。细管道被孔隙网格替代,而复杂的物体被立方体、圆柱体或其他简化几何形状所替代。但是在该项目中,工作人员意识到,3D打印技术是制作物理模型的可行方法,这些物理模型能够体现CAD模型中的所有细节;另外,对于数值模拟来说,理论上可以用现代CFD拟合工具捕获任意一种几何形状。
因此,这个项目有两个平行的工作组。
在实验方面,CSTB(法国建筑科学技术中心)为该项目管理风洞试验的建筑环境和建筑行业提供研究、测试、认证和培训服务,而OCEANIDE海洋工程公司在波盆试验中负责风荷载实验。
在数字化方面,HydrOcean的目标是采用DORIS工程公司所提供的平台顶部结构3D CAD模型,直接对其进行网格化,并未抑制或更正任何几何细节。经过几个月的试错过程,HydrOcean成功使用连续介质力学数值技术中的包面法,将这种极其复杂的3D Rhino模型进行了拟合,连续介质力学数值技术将高质量的三角形表面收缩于几何体上,盲孔、断面和重叠面以及自弃表面。该模型中生成的网格平均有1.4亿个修整过的六面体单元格。
HydrOcean与法国的西门子PLM软件支持团队密切合作,获得了正确的参数,为模拟模型提供了良好的网格质量(包面和体积网格)数值参数。
最终目标是证实绕过CAD净化阶段并使用包面控件进行替代的可行性,该目标已被成功证明。
CFD模拟结果与实验数据紧密贴合
最初HydrOcean模拟了7~8个风向角,模拟结果与实验测试数据的偏差在3~5%之内。最终该公司一共模拟了13个专题,与测试数据差异最大的模拟结果偏差为10%。 接下来,针对CFD模型和与之相应的3D打印模型进行了两个层次的简化,用于评估每个简化层次对测量风荷载和力矩的影响。
在3D打印模型的第一个简化训练中,遵循目前典型的行业实践标准,细管道被孔隙网格替代,复杂的物体(如泵和阀)被替换为立方体、圆柱体或其他简化的形状。在第二个简化训练中,进行了更大程度的简化,整个平台被一个简单的立方体形状所代替。所得的几何形状被数字化模拟,并在风洞中进行物理测试。
两个层次的简化都与风荷载力进行了充分的比较—第一层次简化的模拟结果与实验结果的偏差为5~10%,而第二个层次的偏差为8~15%。 然而,目前来说,很难获得能够满足匹配要求而又满足简化程度最大化的几何形状。对于最为详细的几何形状,模拟结果与测试结果的偏差平均值为4~8%。
对第一个层级简化的模拟结果未进行比较。 对于第二个(极端简化)简化层级,模拟结果与实验结果的偏差平均值为4~6%。
CFD模型准备
该项目的资助者道达尔和DORIS Engineering主要的关注焦点之一是弄清楚,从3D CAD文件转化为CFD模型的过程,能否像3D CAD文件转换为STL文件进行3D打印的过程那样简单。基于使用CAD为风洞测试创建物理模型的丰富经验,上述两家公司知道,尽管需要将CAD模型进行简化,但这一过程仍然比劳动密集型的几何简化和传统CFD模型准备所要求的模型简化更为简单。HydrOcean表示,他们的目标是为CFD开发出一套可比较的方法。
HydrOcean从DORIS工程公司获得的3D CAD模型是Rhino格式的,这个纯净模型并非为CFD建模设计,但是它却代表了几何细节的某些特征。
最初,西门子的PLM支持团队建议HydrOcean将模型分为多个立方体区域,对每个立方体分别进行本地包面,然后进行单个包面操作,以合并所有立方体。但是HydrOcean认为,这种做法将需要花费难以想象的时间和劳动量,并非道达尔和DORIS所寻求的可行方法。
相反地,HydrOcean决定投入大量时间,研究寻找应用包面工具的最佳方法,以便在单个过程中完成整个几何体的网格划分,而不分割几何形状或产生明显的细节损失。期间,大多数时间都花在了如何确定创建能生成高质量体积网格的包面上。
最初,解决方案没有实现收敛。经过仔细检查,HydrOcean发现模拟模型的某些区域显示异常高压、高速剖面和体积网格质量不高等问题。
这些现象是由包装器引起的,因此HydrOcean调整了包面过程,创建一个可以产生收敛的模拟卷网格。在进行的大约15次迭代的过程中,也就是,在避免网格出现次优三角测量区域的前提下,寻求各元素之间最佳连接方式的过程中,多个表面参数一直在不断变化。最后HydrOcean发现,表面参数设置产生的仿真结果与实验值的偏差基本都在10%以内。因此可以说,HydrOcean为连续介质力学数值技术提供了全面的、高保真的、全功能的海上平台建模工业可行的CFD模拟方法,降低了原型成本和测试成本。
CFD simulations of offshore oil and gas platforms are used to predict the maximum wind loads acting on the structure of the platform topsides (the upper half of the platform, above sea level and outside the splash zone, including the oil production plant, the accommodation block and any drilling equipment). The wind loads are used as waves and current loads to design the mooring of the structure, and can be significant in specific ocean areas. Because platform topside geometries were traditionally considered too complex to mesh in high detail, CFD simulations relied on simplified, de-featured models. Their low fidelity meant that, when CFD was used, the results needed to be validated and refined through expensive, labor-intensive fabrication and testing of physical models in wind tunnels.
But in a recent R&D project funded primarily by French multinational oil and gas company Total S.A., with engineering management and additional funding from offshore engineering firm DORIS Engineering, numerical aero and hydrodynamics specialist HydrOcean, subsidiary of Bureau Veritas Marine & Offshore, succeeded in meshing a fully detailed CAD model of a topsides module. Using this high-fidelity CFD model, HydrOcean investigated the effects of multiple wind angles on the platform, matching experimental data from wind tunnel and wave basin tests with wind generation capabilities to within 10 percent – and in most cases 3 to 5 percent – at a fraction of the cost.
The project was financed through Collaborative & Innovative Technology Program in Exploration and Production of Hydrocarbons (CITEPH), a French national program that facilitates access to private funding of innovative R&D projects in oil and gas and related energy industries (http://www.citeph.fr/en/). This was the second of two CITEPH projects in which HydrOcean received funding from Total to develop and validate the use of numerical CFD technology, specifically STAR-CCM+, to compute wind loads on offshore platforms.
CITEPH Wind Loads I
In the CITEPH Wind Loads I project, completed in 2013 and funded entirely by Total, HydrOcean used CFD to reproduce results of wind tunnel experiments that had been performed for a large FPSO unit in West Africa. The project successfully validated the use of CFD for such applications, and enabled to identify the bias of experiments such as confinement, scale effects and boundary layer effects.
CITEPH Wind Loads II
With the use of CFD validated, the CITEPH Wind Loads II project was designed to push CFD to its limits. This project, again managed by HydrOcean, required finding ways to increase the fidelity of both the physical models used in wind tunnel and wave basin testing and the numerical CFD model.
Traditionally, in physical experiments used to assess wind loads over offshore structures, the detailed CAD model of the platform is simplified substantially in the process of creating a physical model for testing. Small pipes are replaced by porosity grids, while complex objects are replaced by boxes, cylinders or other simplified geometry. But in this project, the participants realized that contemporary 3D printing technology would make it feasible to produce physical models that reproduce all the details contained in the CAD model. Meanwhile, for numerical simulation, in theory, any kind of geometry can be captured with today’s CFD meshing tools.
Hence, in this project, there were two parallel workgroups. On the experimental side were CSTB, a provider of research, testing, certification and training for built-environment and construction industries which managed wind tunnel testing for the project, and OCEANIDE, an offshore and coastal engineering firm that took charge of wind load experiments in wave basin testing.
Meanwhile, on the numerical side of the project, HydrOcean’s goal was to take a 3D CAD model of the platform topsides provided by DORIS Engineering designed for other purposes (layout, MTO) and mesh it directly without having to suppress or correct any geometry details. After months of trial and error, HydrOcean succeeded in meshing this extremely complex 3D Rhino model using the surface wrapper in STAR-CCM+, which shrink-wraps a high-quality triangulated surface onto the geometry, closing holes, joining disconnected and overlapping surfaces, as well as automatically discarding obsolete surfaces. The generated grids in this model had on average 140 million trimmed hexahedral cells.
In an intensive joint effort with the Siemens PLM Software support team in France, HydrOcean found the correct parameters that provided good mesh quality (wrapper and volume mesh) and good numerical parameters for the simulation model.
The ultimate goal was to prove the feasibility of bypassing the CAD cleaning phase and use the surface wrapper instead and this was successfully demonstrated.
CFD Results Closely Match Experimental Data
Initially, HydrOcean simulated seven to eight wind heading angles, and the results for the forces were within 3 to 5 percent of experimental test data. Ultimately, the firm simulated 13 headings in all. In the largest divergence from test data, the simulation results differed by 10 percent. Next, two levels of simplification were performed on the CFD model and the corresponding 3D printed model to assess the impact of each simplification on the measured wind loads and moments.
In the first simplification exercise in the 3D printed model, small pipes were replaced with porosity grids and complex objects such as pumps and valves were replaced with boxes, cylinders or other simplified shapes – typical of industry-standard practice at present. In the second, more drastic simplification, the entire platform geometry was replaced by a simple box shape.
The resulting geometries were simulated numerically and also tested physically in the wind tunnel.
Both levels of simplifications compared well for the wind load forces – simulation results differed 5 to 10 percent from experimental results for the first level of simplification, and 8 to 15 percent for the second level. For the moment, however, it was harder to obtain a match, mainly for the most simplified geometry. For the most highly detailed geometry, simulation results were within 4 to 8 percent in average of test results.
No comparisons were made for the first level of simplification. For the second (most extreme) level of simplification, simulation results were within 4 to 6 percent in average of experimental results.
CFD Model Prep
One key interest of project funders Total and DORIS Engineering was to learn whether preparation of CFD models from 3D CAD files could be made as straightforward as the process of converting 3D CAD files into STL files for 3D printing. From extensive prior experience using CAD data to create physical models for wind tunnel testing, the companies knew that this process – although requiring some simplification of the CAD model – is nonetheless much more straightforward than the labor-intensive geometry simplification and de-featuring traditionally required for CFD model preparation. Their goal, says HydrOcean, was to develop a comparable approach for CFD.
The 3D CAD model that HydrOcean received from DORIS Engineering in Rhino format was a clean and for other purposes other than CFD modeling (layout, MTO, etc). However, it presented some features that such as multiple disconnected surfaces and elements, and very high levels of geometric detail which made it difficult to mesh for a CFD analysis.
Initially, the Siemens PLM support team suggested that HydrOcean split the model into multiple boxed regions, perform a local wrapping of each box, then perform a single wrapping operation to merge all the boxes. But HydrOcean decided that approach would require an unrealistic amount of time and labor and would not be the industrially feasible method sought by Total and DORIS.
Instead, HydrOcean decided to invest considerable time and research in finding how to apply the surface wrapper tool to accomplish meshing of the entire geometry in a single process, without splitting the geometry and significant loss of detail. The majority of time was spent on finding how to create a wrapped surface that could generate a very good volume mesh.
The quality of the simulation solution, as confirmed by comparison with experimental data, will be the confirmation that HydrOcean had found a very good wrapping setting and methodology. Initially, the solution did not converge. Upon closer examination, HydrOcean found the simulation model showed some areas of very high pressure, high velocity profiles and other results that revealed some regions of the volume mesh were not of high quality.
Those results, it says, were caused by the wrapper, so it explored how to adjust the wrapping process to create a volume mesh that would yield a simulation that converged. Over some 15 iterations, numerous surface parameters were varied, seeking to find the best connection among elements while avoiding such things as suboptimal triangulation areas in the mesh. In the end, it found surface parameter settings that yielded simulation results that in all instances were within 10 percent of experimental values. Thus, HydrOcean delivered an industrially feasible CFD simulation approach for full-scale, high fidelity, fully featured offshore platform modeling with STAR-CCM+, which will lower prototype and testing costs in the industry.
未经允许,不得转载本站任何文章: