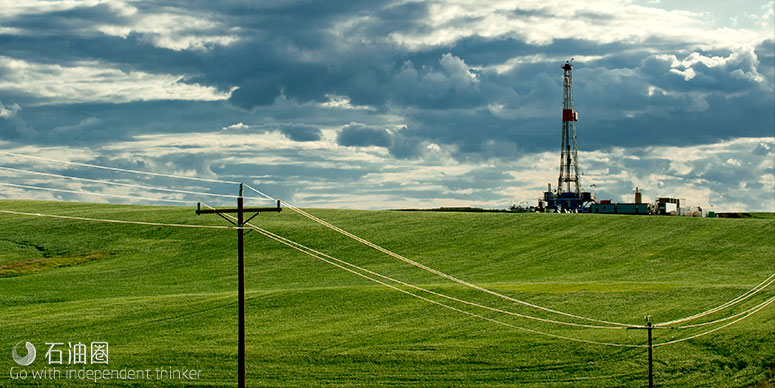
PnP完井工艺是北美地区的非常规完井技术选项,Downhole Technology设计了一种新的桥塞和PnP完井作业方法,可有效节省作业时间和费用。
来自 | World oil
编译 | 张玉亭
为了获得更好的压裂作业增产效果,整个北美地区的页岩油气作业者都将封隔射孔完井作为多级完井最常用的技术选项,并认为该技术的难度和复杂性是可以接受的。追求提高效率和降低成本是非常规油气作业者的追求目标,如果采用新方法对PnP完井工艺进行优化,就能帮助作业者进一步的节省作业时间和成本。
桥塞下放步骤
老版本的压裂桥塞制造商设计方案一般推荐桥塞下入速度不得大于250 ft/min。新一代的桥塞采用新的作业步骤,可以高达1,100 ft/min的速度安全下放。
提高复合桥塞下放速度和可靠性的关键因素在于作业过程中流体通过压裂桥塞和射孔管柱组合上流动的环空流速决定了桥塞的下放速度,而不是泵排量。传统的压裂桥塞供应商一般都会提供一个不同的套管和桥塞尺寸情况下,泵排量与泵送速度相关性的表格,但这一表格中的数据很少能跟实际下放速度吻合,因此供应商只能为电缆作业服务商提供一个关于泵送速度的粗略估算参考值。
环空流速相比于泵排量对于PnP完井作业来说是一个更加精确、更加易于预测的参数。计算环空流速的过程中考虑套管内径、尾管顶深、流动截面和高井斜角的影响非常重要,PnP管柱组合通过变径套管段过程中,这些参数对环空流速的影响很大。
桥塞坐封
一般一套坐封工具在工具寿命周期内会使用成千上万次,而对每次作业做好记录并且每使用1000次左右都重新进行验证非常重要。同样,选择合适的坐封动力弹药也对于桥塞成功坐封也非常重要。像Boss Hog这类桥塞分两步进行坐封,一般建议使用标准弹药的情况下坐封时间为10~40s。使用快速弹药对于此类桥塞的坐封来说坐封时间太短,不利于成功坐封。慢速弹药包含了缓速添加剂,易碎,易破裂失效;慢速弹药还包含一种类似二级弹药的药剂,容易移位妨碍主弹药燃烧。上述两个问题都会妨碍坐封工具充分释放能量导致桥塞在水平井眼中更易发生销钉剪切不充分的情况。
在坐封过程中,当使用投球就位技术的桥塞时,需要保持2~3bbl/min的排量才能保证投球在球座位置的稳定。桥塞一旦坐封完成,地面会会观察到100~200lbf的悬重释放以及约200 psi的立管压力上升。
桥塞磨铣
所有层位都完成增产作业之后,就需要对复合桥塞进行磨铣,对套管通道进行清理以进行生产。新技术采用更短、重量更轻的桥塞,磨铣作业时间是之前常规复合桥塞的一半左右。
磨铣作业之前,我们推荐使用Cerberus软件(或者其他类似软件包)对连续油管以及推荐的磨铣工具组合的预期作业效能进行模拟。该软件能够帮助作业者明确制定碎屑清除所需的化学药品方案,并确定作业工具和循环方案是否能够无阻卡完成所有桥塞(包括趾端桥塞)的移除。
对于大多数5-1/2in井眼,一般推荐使用2-3/8in或者2-5/8in连续油管,而不是更常使用的2in连续油管。大尺寸连续油管能够进行高排量的泵注,并可使用3-1/8in~3-1/2in外径的慢速高扭矩井下马达工具。上述泥浆马达能够不停钻完成桥塞磨铣,并允许进行高排量泵注,将环空流速增至240 ft/min,甚至更高,从而将磨铣碎屑高效返出地面。
由于需要覆盖整个桥塞并避免大尺寸碎屑和桥塞核心部件的产生,因此,磨铣作业要求钻头/磨鞋尺寸为套管内通径的99~100%。因此,推荐使用密封轴承牙轮钻头,能够保证持续产生小尺寸碎屑。这主要是由于此类钻头在作业过程中的三点旋转研磨动作,在固定切削面上产生较大的剪切作用。由于密封轴承牙轮钻头采用了很多创新设计,其寿命得到了很大的提高,特别是在5-1/2in以及更大尺寸的套管中应用的情况下。在4-1/2in套管中应用的时候,该钻头可能仍需与低转速高扭矩井下马达连接使用,并采用钻压最小化钻进方法。上述做法能够有效降低轴承过热以及牙轮脱落的风险。最新的磨鞋,特别是针对桥塞磨铣专门设计的磨鞋,其作业性能已超过了之前的五刀翼磨鞋方案,主要是由于新磨鞋减少了侵入端面,并且水眼更小。
直到最近,桥塞磨铣的标准作业方法仍然是循环胶液清洗井眼和防卡过程中进行短起,将连续油管柱起出水平段。每次短起作业一般要持续几个小时,并且会降低连续油管柱的工作寿命,同时增加作业所需的水和化学药剂用量。为了减少短起次数,整个磨铣过程中将钻压维持在最低水平,产生较小尺寸的碎屑。采用合理的低到中等清扫胶液排量清扫方案,保证磨铣结束时清扫液都离开钻头,有助于保障碎屑携带和清洗效果。
返排是磨铣作业成功的关键因素,确保返排排量合理,保证井眼欠平衡的条件下略大的泵排量,保障整个作业过程中不发生地层流体侵入,这对于确保整个井眼内流动装填为湍流至关重要。湍流能够确保将碎屑连续携带至主流动区域,从而使得碎屑能够高效地被携带至地面。该作业需要连续油管作业人员、泵/化学药剂供应商和返排作业人员的密切配合。
结论
PnP作业是整个北美地区很多非常规含油气盆地的完井作业技术选项,通过对作业方案、现场协调、桥塞选择、下放和坐封步骤、磨铣和碎屑移除作业进行优化,作业者能够大幅节省作业时间和费用,同时还能提高作业井的产能。
SETTING PLUGS
A setting tool can be used for thousands of runs in its life span; however, it is important to document each run and get certified every 1,000 runs or less. Proper power charge selection is an important factor in successful plug setting. Plugs like the Boss Hog model are set in a two-step process. We recommend using standard charges with 10-to-40-sec setting times, because fast-acting charges may set plugs too quickly for them to set properly. Slow charges include additives to slow their activation, and tend to be brittle and prone to cracks and voids. Slow set charges also contain a small pill, like a secondary charge, that can fall out of place and keep the charge from burning. Both problems can prevent the setting tool from releasing its full power and make the tool more likely to not shear properly in horizontal wells.
When setting plugs with the ball-in-place feature, operators should pump at 2 to 3 bbl/min., to keep the ball in its seat during the setting process. Once the plug is set, a 100-to-200-lbf line weight loss and a 200-psi pressure increase will be noted at surface.
PLUG DRILL-OUT
After all stages have been stimulated, the composite plugs have to be drilled out to establish a clear casing ID for production. Shorter, lighter-weight plugs can be drilled out in about half the time required for previous composite plugs.
Before drill-out operations, we recommend using Cerberus software (or a similar package) to model the expected performance of the coiled tubing string and BHA proposed for use on the drill-out. The software helps specify chemical programs for debris removal and determines whether the string and available circulation can remove all plugs, including those near the toe, without getting stuck.
In most wells with 5.5-in. casing, a 2?- or 2?-in. CT string is recommended, instead of the more common 2-in. coil size. The larger coil enables high flowrates and use of 3?-to-3?-in. OD even wall downhole motors with slow-speed, high-torque power sections. These mud motors can drill out plugs without stalling, and can handle high enough flowrates to create AVs of 240 ft/min. or higher, to effectively circulate cuttings back to the surface.
The drilling bit/mill should be gauged at 99% to 100% of the casing ID drift, as it provides full coverage of the plug and prevents production of larger debris, as well as coring of the plug. A sealed bearing roller cone bit is recommended, as it produces consistently smaller cuttings. This is due to its rotary crushing action of three points, versus a shearing action enacted by one solid cutting interface of a mill. With more innovative designs of sealed bearing roller cone bits, the longevity of the bit has greatly improved—especially in 5.5-in. or larger casings. In a 4.5-in. casing, a sealed bearing roller cone bit may still be used in conjunction with a low-speed, high-torque motor, as well as drilling best practices of minimum weight-on-bit (WOB). This reduces the risk of overheating bearings and potentially losing a cone. New mills—specifically designed for plug drill-out operations—have performed better than previous five-blade mill designs. This is due to their less aggressive facing and smaller water courses.
Until recently, standard practice during plug drill-out operation was to perform short trips—pulling the CT string out of the horizontal section, while circulating gel sweeps to effectively clean the hole and prevent sticking. In addition to taking several hours for each trip, this practice reduces the working life of the CT string and increases the overall water and chemical volume for the operation. To eliminate short trips, WOB is kept to a minimum during drill-out to achieve small particle cuttings. Light to moderate viscosity gel sweeps are timed carefully, so that they exit the bit as the plug finishes drilling. This helps entrain all the cuttings and facilitate an effective cleanout.
Flowback is also a key component to drill-out success. Ensuring that the flowback rates are matching—if not slightly exceeding the pumping rate (underbalanced), without drawing in from formation throughout the overall operationis critical to maintain turbulent flow throughout the wellbore. Turbulence allows continuous entrainment of the solids into the main flow regime, to effectively transport the cuttings back to surface. This operation requires close cooperation between the CT operator, pump/chemical supplier and flowback operator. The extra effort can result in significant improvements in efficiency and lower overall cost, as well as achieve earlier production from the well. For example, our company has recently worked with numerous operators in the Rockies to safely reduce drill-out times from 36-60 hr to 10-12 hr.
CONCLUSION
The PnP operation is the completion method of choice in many unconventional basins throughout North America. By optimizing job planning, wellsite coordination, plug selection, running and setting procedures, and drill-out and debris removal processes, operators can realize significant savings in time and cost, while improving productivity from their wells.
未经允许,不得转载本站任何文章: