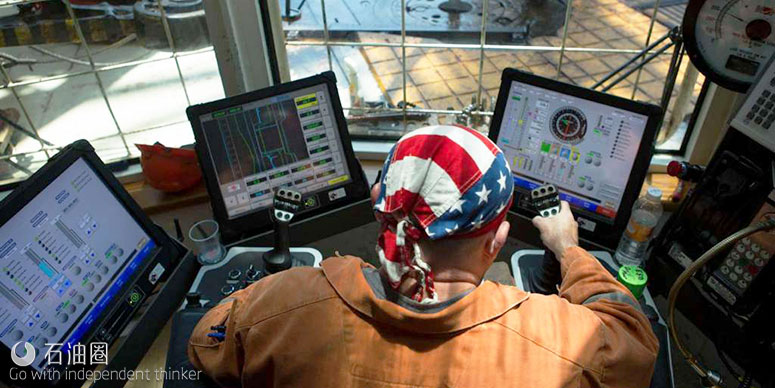
过去几十年,从旋转控制设备(RCD)使用数量的增长幅度来看,闭环及加压循环泥浆系统相关钻井技术正被广泛应用于陆地钻井作业。这些技术的有效性已经在陆上钻井中得到验证,因此,在海上钻井中将其加以推广应用就显得顺理成章又十分必要了。
作业公司使用RFC-HSE闭环系统,有利于井涌-漏失的早期检测,识别井内流体流向,利用回压(SBP)抑制储层流体的溢流。该系统还可以进行动态地层完整性测试(FIT)和破裂压力试验(LOT),以明确井下条件。石油圈原创www.oilsns.com
昨天的【石油科技】板块,小编介绍了RFC-HSE闭环系统的技术背景和应用必要性,今天将继续带大家了解该技术的兼容性、作业优势与作用原理等情况。
设备的兼容性石油圈原创www.oilsns.com
用于海上作业环境的RFC-HSE MPD设备与陆地设备类似,但需要增加一个与作业钻机类型兼容的RCD,并且节流管汇系统必须能够完全采用PLC自动操作。最终的配置基本上与CBHP相同。
RFC-HSE MPD系统不仅可用于井涌-溢流检测,还可以连续监测井眼压力,并将钻井过程中产生的气体安全地引流至预定系统。该系统实时监测从井中返出的泥浆密度,并与含气量进行关联。如果需要,系统可以将单根气导向液气分离器。石油圈原创www.oilsns.com
作业优势石油圈原创www.oilsns.com
虽然RFC-HSE MPD主要的关注点是安全循环钻井液,但同时还节约了MPD设备的相关费用,为客户带来了更多的作业优势。
RFC-HSE MPD采用的闭环系统,可以将井筒返出的流体导流到远离钻台的安全位置,并在需要时施加SBP。该系统独有的监测更小溢流和补偿浮动钻井设备运动的能力,有助于减小井涌的误报频率。RFC-HSE MPD通过提供实时精确的流入/流出量,有利于井涌-漏失的早期探测。
在需要的情况下,RFC-HSE MPD能够进行动态FIT和LOT,让钻井人员能够确定并量化压力控制能力。其他一些值得关注的功能包括:
- 钻井作业期间,实时确定地层压力和破裂压力;石油圈原创www.oilsns.com
- 避免井眼恢复循环后泥浆流入地层以及停止循环后地层液体流入井筒;
- 使用自动节流阀循环出已知的少量溢流,代替手动关井并循环出溢流;
- 特殊作业期间的井眼监测,如起下钻和固井;石油圈原创www.oilsns.com
- 强化井眼压力管理。
控制井眼压力剖面石油圈原创www.oilsns.com
大约自1901年的Spindletop油田以来,传统的钻井水力学几乎没有本质的变化,主要依靠钻井液的静液压力作为一级井控措施。在常规钻井中,二次井控设备(即BOP)用于控制溢流,并阻止地层流体进一步流入井筒。然后,采用常规方法将溢流循环出井,并将泥浆密度提高至大于孔隙压力以恢复钻井作业。
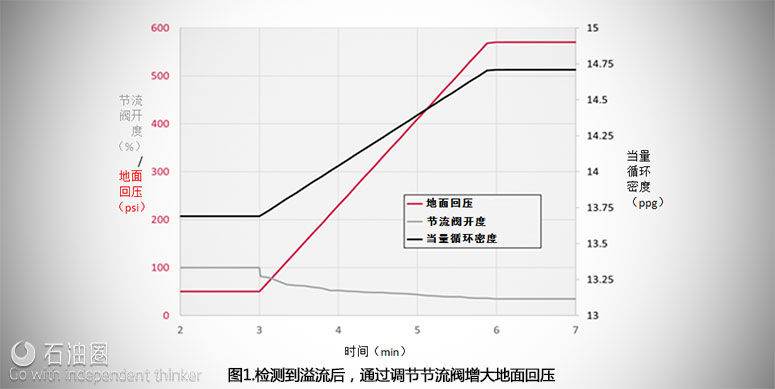
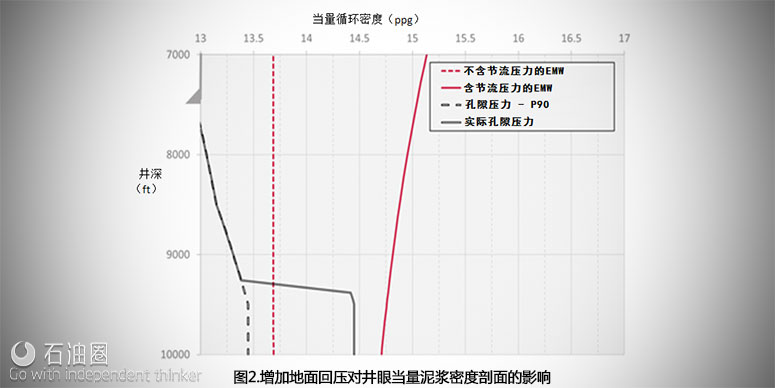
如图2所示,井底压力的增加相应增大了井底的EMW,表明可以迅速地调节环空压力剖面以避免溢流的进一步侵入。注意,根据具体的井眼状况和系统配置,节流阀的响应时间可以比图中所示的更快。与常规井控相比,通过快速响应调节SBP可以有效地减小溢流量。包括及未包括节流压力的EMW曲线,代表特定节流压力下的当量泥浆密度。
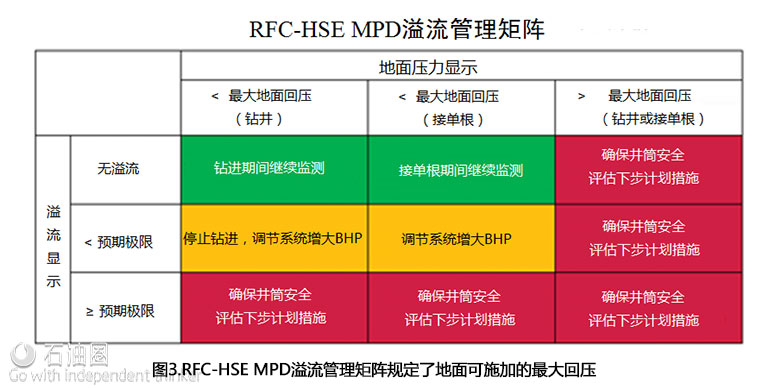
通常根据井眼完整性和地面压力限制,单独计算钻井和接单根操作时的最大SBP。如果得到了钻井公司、油公司和监管机构允许和批准,系统可以循环出少量的溢流,而不必关井。溢流管理矩阵描述了系统可以安全循环出的最小溢流量。石油圈原创www.oilsns.com
在溢流循环出井后,钻井公司可以按BSEE的规定提高泥浆密度继续钻井。RFC-HSE的有效应用可以减小孔隙压力和破裂压力的不确定性带来的影响,而新的BSEE规定正强调了这一点。因此,RFC-HSE MPD系统增强了MPD技术的优势,进一步提高了钻井公司执行监管机构有关安全钻井余量规定的能力。
减少溢流假报警石油圈原创www.oilsns.com
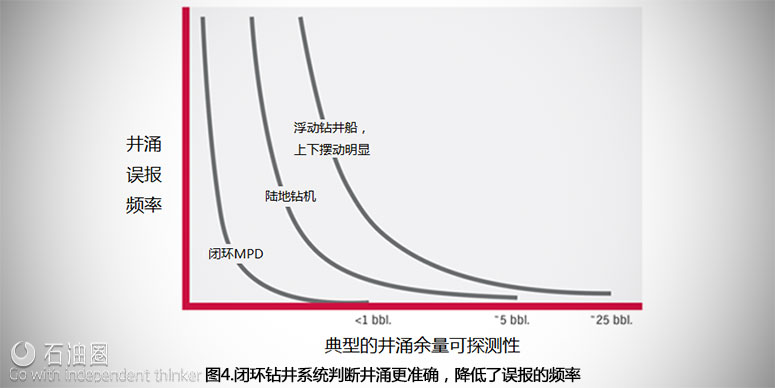
近年来,在经历了几次知名的井控事件之后,作业公司将海上钻井平台上的井涌报警阈值范围设置得更小了。但这一做法却提高了溢流误报的频率,增加了不必要的NPT,作业人员很可能在经历了多次误报后将一次真溢流习惯性得理解为一次假警报。如图4所示,RFC-HSE MPD的一个重要优点在于可以减少误报的频率。
日前,可以兼容MPD的海上钻井平台数量正在不断增加。RFC-HSE版本的MPD系统,最适用于设计采用开放式钻井系统的油气井。RFC-HSE MPD不仅能检测溢流,而且可以根据需要施加SBP,以便在井关井之前,阻止溢流并减小溢流量。RFC-HSE溢流管理矩阵规定了可施加的最大SBP,有效地提高了操作的安全性,保护了人员和财产。
RFC-HSE MPD堪称海上钻井作业中效果最佳、应用最安全的技术之一,并且具有可观的经济效益。在过去的二十年里,闭环系统在陆地钻井中数千次的成功应用,证明其通过减少NPT节约的成本通常大于使用成本,而且闭环系统能够降低侧钻的风险,提高建井作业期间层间的隔离性。
作者/Don Hannegan等 译者/白小明 编辑/Leia
Compatible Equipment
The equipment needed for RFC-HSE MPD in marine environments is similar to that required onshore but adds the stipulations that a fit-for-purpose RCD must be suitable for the rig type being used, and the choke manifold system must be fully automated by a PLC. The resultant setup is essentially the same required for the CBHP variant.
The RFC-HSE MPD system not only can be used for kick-loss detection but can also continuously monitor the wellbore pressures and divert drilling and background gas safely to the appropriate systems. Mud weight returning from the well is monitored in real time and correlated to the associated drilling gas percentage. Connection gases could be routed to the mud/gas separator if deemed necessary.
Operational Benefits
Although RFC-HSE MPD primarily focuses on the safety of the circulating fluids process itself, a range of operational benefits contribute to recovering the cost of the MPD kit. RFC-HSE MPD enables a closed-loop system for diverting wellbore fluids away from the rig floor and applying SBP when needed. The system’s ability to detect flow in gallons rather than barrels and to compensate for floating rig movement helps to minimize false-positive kick alarms. RFC-HSE MPD also facilitates early kick-loss detection by providing precise mass flow in/out measurements in real time.
The ability to conduct dynamic FITs and LOTs whenever advisable enables drillers to verify and quantify pressure containment capability. Other noteworthy capabilities include:
- Real-time quantification of formation and fracture pressures during drilling operation;
- Wellbore ballooning upon regaining circulation and kicks from wellbore breathing;
- Circulating out an influx of known small volume using the automated choke control, as opposed to shutting in and circulating out manually;
- Wellbore monitoring during special operations such as tripping and cementing;
- Managed pressure wellbore strengthening.
Controlling Wellbore Pressure Profile
Conventional drilling hydraulics – which remain virtually unchanged since Spindletop Field, circa 1901 – rely on hydrostatic mud weight as the primary well control barrier. In conventional drilling, secondary well control equipment (i.e., BOPs) is used to manage kicks and stop further intrusion of formation fluids into the wellbore. The influx is then circulated out of the wellbore using conventional methods. Mud weight is typically increased above the pore pressure to resume operations.
Figure 1 illustrates an increase in SBP as the choke reacts after detecting an influx. The corresponding increase in bottomhole pressure results in an increase of downhole EMW, illustrated in Figure 2, which demonstrates that the annular pressure profile can be swiftly manipulated to prevent further intrusion of an influx. Note that faster choke reaction times than those illustrated in these figures are possible depending on the specific well and system configuration.
By enabling a swift response, SBP manipulation can effectively minimize influx size, compared with conventional well control. EMW with and without choke pressure lines represents equivalent mud weight at specific value of choke pressure.
Figure 3 illustrates an influx management matrix that defines the maximum SBP that the system can apply before the well is shut in. The maximum SBP is typically calculated separately for drilling and connection operations depending on wellbore integrity and surface pressure limitations. If permitted and approved by the contractor, operator and applicable regulatory bodies, the system can circulate a small-volume influx instead of shutting in the well. The small influx volume that can be safely circulated through the system is described in the influx management matrix.
After the influx has been circulated out, drilling can continue with increased mud weight in accordance with BSEE regulatory rules. Effective application of RFC-HSE can help minimize the impact of the pore pressure and fracture pressure uncertainty, which the new BSEE rule emphasizes. The RFC-HSE MPD system, therefore, augments the benefits of MPD technology, further enhancing the operator’s ability to comply with the safe drilling margin requirements from regulatory authorities.
Reducing False-Positive Kick Alarms
After several high-profile well control incidents in recent years, there has been a tendency to tighten kick alarms settings on offshore rigs. This practice has increased the frequency of false-positive kick alarms, resulting in unnecessary NPT, as well as increasing the risk of a real kick being interpreted as just another false alarm. A significant operational benefit of RFC-HSE MPD is its ability to reduce the frequency of false alarms, illustrated in Figure 4.
Summary
The availability of MPD-capable offshore drilling units is on the rise. The RFC-HSE variant of MPD is best suited for wells designed with open-to-atmosphere drilling systems. RFC-HSE MPD is intended not only to detect influx but also to apply SBP as needed to stop influx and minimize the influx size before the well is shut in. The RFC-HSE influx management matrix defines the maximum SBP that can be applied while the well is shut in. This effectively increases operational safety and protects personnel and assets.
RFC-HSE MPD may be considered one of the best and safest technologies for drilling in marine environments and offers economic benefits. As proven on thousands of land applications over the past two decades, the cost of drilling with a closed-loop system is often exceeded by the savings resulting from reduced NPT, lower risk of sidetracks and improved zonal isolation during well construction.
未经允许,不得转载本站任何文章: