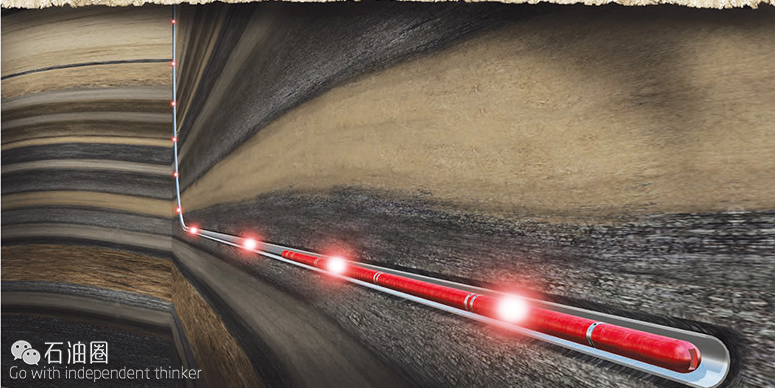
上一期文章中为大家介绍了哈里伯顿SPECTRUM连续油管诊断服务,本篇文章将对修井服务进行简单介绍。SPECTRUM修井服务通过定制化的BHA得到井下关键实时数据,进而优化连续油管修井作业。
标准的连续油管修井作业中,可用的参数仅有管串重量、循环压力,而SPECTRUM修井服务提供井底处理井段的实时井下数据,让操作人员更透彻的了解井下实际的状况。
SPECTRUM连续油管修井服务
SPECTRUM采用模块化配置,在修井作业过程中可以提供实时关键数据测量(如工具内外的压力、温度、距离套管节箍定位器的距离、伽马、井斜、工具面、拉压力和扭矩),井下数据通过遥测系统(如光纤)传至地面,不影响整体服务的进程。
利用这些数据操作人员可以得到地下详细情况的快照和一段时间内的整体趋势,尽可能的在一趟钻完成更多作业内容,并且能够实时优化流体和工具性能。
在SPECTRUM系统工作时,BHA数据可以通过有线或者无线遥测系统传输至地面。在保留所有常规作业参数测量功能的基础上,SPECTRUM的有线遥测系统重量做到很轻,方便陆地运输、海上提升。BHA包括过流工具,传感器能够满足175℃温度、105MPa绝对压力级别的工作状况。
井底数据传输到地面后经过处理可以在控制室得到可视化图像,同时也可以通过卫星传播到全球其他终端用户。SPECTRUM的这一特性可以满足在不同地点的客户、专家和决策者尽快了解当前的井下状况,能够快速做出决策、制定最合适的作业方案。
通过使用实时数据,保证连续油管工具和设备处于最佳状态范围,避免失效,SPECTRUM修井作业中的不确定性得到显著降低,增加了可靠性。例如,通过套管节箍定位器和伽马技术可以准确定位井深,避免射孔或者坐封封隔器时的井深不确定问题。实时温度监测可以帮助了解井下状况,方便优化化学处理。模块化的传感器系统可以根据客户需求定制,满足更加复杂的连续油管作业要求。
应用范围石油圈原创www.oilsns.com
- 磨铣作业
- 操作机械工具
- 清洗井眼
- 打捞作业
- 射孔(连续油管传输和水力喷射)
- 分支井进入
- 增产准确性
- 协调处理(堵水或堵气)
应用优势石油圈原创www.oilsns.com
- 提高可靠性,减少非生产时间
- 防化学腐蚀
- 实时决策能力
技术特性石油圈原创www.oilsns.com
- 光纤、无线或者电缆传输数据
- CCL井深定位
- GR井深定位
- 内外压力和温度测量
- 工具面和井斜测试
- 扭矩、拉力、压力测量
应用级别石油圈原创www.oilsns.com
案例分析:精准定位井底马达,提高磨铣作业效率
磨铣作业通畅是以清除井内障碍为目的,以便提高日常作业或特殊作业的效率,同时开发商希望在降低成本的情况下使用最少的时间。在本案例中,沙特某油田计划在一口关键气井进行侧钻作业,首先要磨铣掉一个油管短节,以便后续下斜向器。
作业人员计划采用连续油管进行作业,使用SPECTRUM修井服务的实时BHA系统,该系统可以精确测量整个磨铣过程的情况,以保证较近处一封隔器的完整性,避免发生事故造成修井等不必要的后果。
挑战石油圈原创www.oilsns.com
早前的作业经验已证明,不当的磨铣作业存在着风险和低效率、马达频繁制动等问题,而重新定位需要耗费很多时间。优化作业和提高工具表现性能需要满足两个关键因素:1)实时监测连续油管的井深来精确定位高效磨铣短节;2)磨铣时优化井下马达的工况来避免非生产时间(NPT)和作业延迟。
解决方案石油圈原创www.oilsns.com
哈里伯顿使用了SPECTRUM修井服务,在连续油管上配合定制的模块化BHA,通过传感器采集实时数据,借助套管节箍定位器来校深,并监测整个马达的压力。实时测量数据传至地面,作业团队就可以通过较深精确确定短节的位置,同时避免马达制动,进一步降低磨铣作业时间,避免额外起下钻趟数。
使用SPECTRUM修井服务获得的实时数据提高了作业效率,达到了客户的目标,同时显著降低了作业中损坏封隔器的风险。另外,井下工况和工具性能更加透明,与类似作业环境下相比,使用SPECTRUM服务提高了整体作业效果。
结果石油圈原创www.oilsns.com
获得了实时压力和井深测量数据,可以使作业者控制和优化作业中的钻压、排量,提升井下马达的可靠性,优化了磨铣作业表现。
作业者如期达到了其磨铣障碍物,同时不损坏封隔器的目的。并且通过使用SPECTRUM修井服务的实时连续油管服务,为客户节省了修井机的作业成本。
来自/Halliburton 译者/白小明 编辑/Lemon
SPECTRUMSM Real-Time Coiled Tubing Services combines intervention and diagnostic services to help operators monitor and optimize job performance in real-time, resulting in greater efficiency, increased reliability, and higher return on investment.
OVERVIEW
SPECTRUMSM Intervention Services optimizes coiled tubing well intervention by providing critical real-time data from a customizable bottomhole assembly (BHA). Unlike standard coiled tubing jobs where surface-measured parameters, such as pipe weight and circulating pressure, are the only available data, SPECTRUM Intervention Services delivers real-time subsurface insight from where the treatment is being applied, along with data from the surrounding downhole environment.
This modular system can be configured to deliver key measurements (such as pressure inside and outside the tool, temperature, depth from casing collar locator and gamma ray, inclination, tool face, tension/compression and torque), resulting in the ability to maximize a single trip downhole and adapt to near-wellbore conditions in real time to optimize fluids and tool performance. The information is transmitted to surface via telemetry systems, such as fiber optic, with no impact on overall service execution. The data can be used to measure what is going on below the surface, as a detailed snapshot or as a more comprehensive trend over a certain period of time.
HOW IT WORKS
Data transmission from the BHA is established via a selection of wired or wireless telemetry systems. The compact size of the wired telemetry allows all regular operational parameters – including pump rates, tolerance to corrosive fluids, and ball-drop capability – to be maintained with minimum added weight for road transportation or offshore lifting purposes. The BHA includes flow-through tools that accommodate sensors rated to 350°F (175°C) and 15k psi absolute pressure. At surface, the information is processed to allow visualization in the operator’s control house, as well as broadcasting via satellite communication to global users. This capability permits customers, subject matter experts, and decision makers to be simultaneously and immediately alerted to current downhole events and to quickly arrive at informed decisions on the most appropriate course of action.
ADVANTAGES
By using real-time data, SPECTRUM Intervention Services reduces uncertainty during operations and increases reliability by keeping coiled tubing tools and equipment in their optimal operating envelope to avoid failures. For example, depth is accurately controlled with the casing collar locator and gamma ray technology, helping to eliminate doubts on where to perforate or set a packer. Real-time temperature monitoring improves insight of downhole conditions and allows optimization of chemical treatments. The modular system of sensors can be combined and customized to meet the demands of the most complex coiled tubing operations.
APPLICATIONS
- Milling
- Manipulating mechanical tools
- Wellbore cleanouts
- Unloading
- Fishing
- Perforating (tubing-conveyed perforating and hydrajetting)
- Multilateral entries
- Stimulation accuracy
- Conformance (water or gas shutoff)
ADVANTAGES
- Help improve reliability and reduce nonproductive time
- Invisible to coiled tubing operations
- High flow rate capability
- Chemical-resistant
- Real-time decision-making capability
FEATURES
- Fiber-optic, wireless, or electric cable
- Depth correlation with casing collar locator (CCL)
- Depth correlation with gamma ray (GR)
- Internal and external pressure and temperature
- Tool face and inclination
- Torque, tension, and compression
RATINGS
- 350°F (175°C) » 15,000 psi
SPECTRUMSM INTERVENTION SERVICES ENABLES ACCURATE DOWNHOLE MOTOR POSITIONING AND FLAWLESS OPERATION ON CRITICAL WELL MILLOUT
OVERVIEW
Milling interventions are often necessary to remove restrictions in a well for optimum efficiency of routine or special operations, while minimizing downtime without incurring any costly damage. In this case, an operator in Saudi Arabia was preparing to sidetrack a critical gas producer well, which first required milling out of a tubing nipple restriction in order to allow subsequent deployment of the whipstock.
A coiled tubing operation was planned, using SPECTRUMSM Intervention Services’ real-time sensing bottomhole assembly (BHA) to maintain accurate depth control throughout the milling process, with an essential goal of preserving the integrity of a close-by packer in order to avoid pulling the completion string. With SPECTRUM Intervention Services, the millout was accomplished without damaging the packer, thus preventing the operator from having to pull the completion string with a workover rig.
CHALLENGES
The prior operator’s experience had demonstrated inherent risks and inefficiencies related to inadequate milling performance, due to frequent motor stalling and extra time on location. Improving operations and tool performance would require two key elements: 1) Monitoring the coiled tubing depth in real time to assist accurate positioning in order to efficiently mill the nipple, and 2) optimizing proper operating conditions of the downhole motor while milling out the restriction to help prevent nonproductive time (NPT) and job delays.
SOLUTIONS
Halliburton used SPECTRUM Intervention Services with a modular BHA on coiled tubing, customized for collecting real-time data with sensors for depth correlation via a casing collar locator and pressure monitoring across the motor. Leveraging the real-time measurements being delivered to surface operations, the team accurately identified the nipple position by correlating depth while also preventing motor stalling – further minimizing millout time and avoiding extra trips to replace damaged components.
The use of SPECTRUM Intervention Services’ real-time data resulted in an efficient operation that achieved the customer’s objectives, while significantly mitigating the risk of unintentionally damaging the packer. Additionally, the transparency of downhole conditions and tool performance led to a significant improvement in overall results compared to similar operating environments.
RESULTS
Real-time pressure and depth measurements allowed the operator to control and optimize weight on bit and pump rate during the job, resulting in improved reliability of the downhole motor and optimized milling performance.
The operator achieved its objective of milling the restriction without damaging the packer or having to pull the completion string, thus saving potential associated workover rig costs by being able to deliver the entire operation via SPECTRUM Intervention Services’ real-time coiled tubing services.
未经允许,不得转载本站任何文章:
-
- Demons
-
石油圈认证作者
- 毕业于中国石油大学(北京),化学工程与技术硕士,长期聚焦国内外石油行业前沿技术装备信息,具有数十万字技术文献翻译经验。如需获取更多技术资料,请联系Demons(QQ2582825239;微信15810965891)