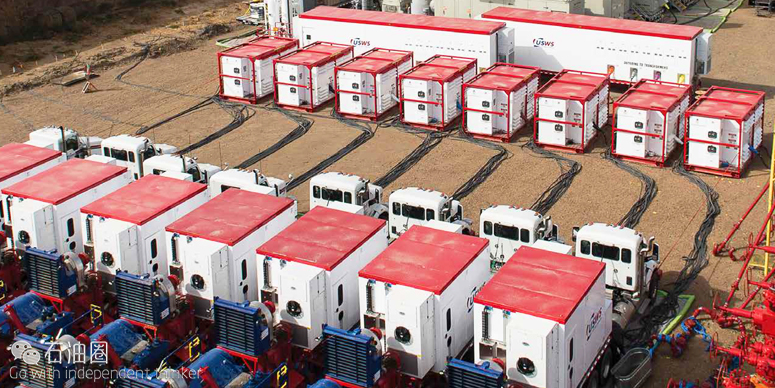
在全球范围内,油田运营商都面对着严峻的环境监管压力,废物排放、噪声、矽尘等都会造成严重的后果。不合格地区对氮氧化物、一氧化碳、甲烷及其他排放物的管控更为严格。
在当今这个低油价、低成本的时代,仍然必须要强调改善这些状况,并同时降低总成本,提高效率。U.S. Well Service (简称USWS)公司近日推出了一项全新、环保压裂技术Clean Fleet with Whisper—首个全电驱动、可移动的水力压裂设备,100%由天然气提供能源,在节约成本的同时解决了环境监管的问题。
电驱动压裂原理石油圈原创www.oilsns.com
传统的水力压裂设备由超过20台柴油机驱动,每台柴油机制动马力(bhp)高达2,500 hp。将压裂现场所有的柴油机由可移动的涡轮发动机替代,整套压裂设备就可以完全由电驱动。这种技术最早于2014年开始现场实施,目前在北美两套可用的电驱动压裂设备。
相对柴油来说,天然气是更加清洁的能源,它产生极少的污染。与传统的四冲程柴油机相比,涡轮发动机可以允许连续燃烧,因此燃烧更充分,大幅降低排放物。天然气驱涡轮发动机有如此大的优点,是源于其采用的预混合燃烧技术,可以保证空气和天然气配比更均匀,避免的禁排物的形成。涡轮发动机内,超过60%的空气可以和天然气预混合,这可以保证空气和天然气混合物的均质性。
电驱动压裂设备完全由从管道供给的天然气提供能源,如果现场没有天然气可用,也可以使用CNG或LNG。两台大型电动压缩机可以将天然气压缩至涡轮发电机需要的300psi压力。两台压缩器一起工作的话,可以为涡轮发电机提供的气体排量高达3 MMcf/d – 4 MMcf/d。
可以根据井增产实际需求的水马力(hhp),来选择使用3台或者4台涡轮发电机。每台发电机可以提供三相交流电量5.67MW(电压13,800 v),合计17.01 MW – 22.68 MW,输出的电符合ISO标准。涡轮发电机发出的电经过装有一组开关设备的拖车。这些设备重新分配电流,提供断路装置,为地面设备如接地设备提供安全保护。然后电流离开开关设备,用变压器降压至600 v。变压器为浇注线圈干式变压器,额定容量3,500千安培伏特。
至此,电动压裂设备和传统的水力压裂设备就差不多了,唯一不同是用电动马达和变频设备(VFDs)替代了柴油发动机和变速箱。每套电动压裂设备有8台双泵拖车,工作电压均为600-v。每辆双泵拖车水马力为3,500hhp,整套设备提供的水马力为28,000hhp。
双泵系统有2台独立的三缸泵。传统的柴油驱动泵设备,在鹅颈管处通常有很大的散热器。在电驱动泵,不需要散热器,取而代之的是一个VFD房和2个独立的VFDs。另外,电驱动泵不需要搅拌器、保湿设备、大风扇、防砂设备、真空除尘设备等。
世界首套全电驱动压裂装置
USWS公司带来的Clean Fleet电驱动压裂装置采用了业内最先进的设备,在保证压裂效率的同时还提高了现场操作的安全性,降低环境影响。
- Clean Fleet的电力来自作业现场的天然气燃烧发电,整个操作过程燃料费用可降低90%
- Clean Fleet能够显著降低压裂对于空气的污染,氮氧化物和一氧化碳的排放降低99%
- Clean Fleet的使用消除了柴油运输的必要,降低运输风险和费用
- Clean Fleet Whisper技术能够显著降低作业现场噪音污染,使作业现场更加安全
- 针对作业时设备的震动问题,Clean Fleet采用了最先进的技术,可降低振动80%,提高操作成功率和安全系数
降低气体污染石油圈原创www.oilsns.com
电驱动压裂设备对环境来说最大的优势是零排放。经第三方检测机构证明,相比于传统的柴油压裂技术,Clean Fleet将污染气体排放降低了99%,几乎可以做到有害气体零排放。
这种零排放主要是因为用天然气作为能源取代了传统的柴油机。排气口测得的涡轮发电机的氮氧化物的排放量少于0.036 g/kWh。这同美国环境保护署(EPA)要求的非公路柴油机的排放量来说是巨大的降低。这看起来有些不可思议,其实这是将柴油机换为电动压裂装置的自然结果。此外,Clean Fleet还能够减少甲烷这一剧毒物质的漏失,这是相对于柴油和混合压裂技术的另一大优点。
降低成本,提高效率石油圈原创www.oilsns.com
用现场的天然气驱动涡轮发动机,降低了90%的成本。Clean Fleet最高可提供14500psi的工作压力,是业内工作压力超过10000psi的最新产品之一,搅拌器的转速可达130bpm。
涡轮发电机平均每小时消耗107 Mcf的天然气,可为压裂设备提供超过10,000 hhp的动力。而柴油发动机要提供同样的动力,每小时需要消耗大约1,000加仑的柴油。这种大幅度的成本节约,源于现场未处理的天然气的低价格和节约了天然气的运输成本。
电动马达第一次维护时间间隔为30,000小时,且预期寿命高达20年。柴油发动机需要每个月进行维护,例如换油和换过滤器,而电动压裂设备不用。长寿命减少了维护时间,增加了泵的使用时间,具有很大的经济优势。
降低噪声污染石油圈原创www.oilsns.com
Clean Fleet Whisper是USWS公司专门用于降低噪声污染而研发的模块,该模块目前是业内最为先进的噪声消除技术。Whisper能够显著降低噪声,提升现场工作到安全性,减少对周边居民的打扰。
在科罗拉多州Wattenberg油田作业的电驱动压裂设备,测得的声音分贝数为7 dBA(dBA,A指描述听得见的高频噪声) 和12 dBC (C指描述低频震动噪声,可以摇动窗户),这都比柴油驱动的压裂设备的噪声低很多。声音强度在dBA级别降低了80%,在dBC级别降低了95%。
降低振动 提高稳定性石油圈原创www.oilsns.com
Clean Fleet®技术通过降低振动和金属疲劳来增加安全性。与传统的柴油驱动设备相比,我们的电驱动压裂设备可以降低金属振动80%。可以通过在柴油机驱动设备上安装3D的加速计来测量振动,将此结果同从电驱动设备上测得的数据进行对比得到这个结论。这种大幅度的降低主要是通过用VFD替代柴油发动机和变速箱实现的,VFD控制电动马达,而电动马达与水力压裂泵是直联的(没有中间设备)。
技术创新不止步石油圈原创www.oilsns.com
SANDSHIELD减少矽尘石油圈原创www.oilsns.com
常规的柴油机压裂作业现场会有大量的矽尘,这对于作业人员身体危害和现场的安全都是非常大的威胁。Clean Fleet技术采用了USWS公司研发的SANDSHIELD技术,显著降低现场的矽尘。两套电驱动压裂设备都有电动尘控设备来减少矽尘,大幅低于PEL标准。和其他增产设备一样,真空除尘设备也由600-v电驱动。测得设备可以减少矽尘排放,低于PEL标准80%。为了增加安全性,在控制危险源方面,相比行政管控和劳保设备,这些工程的控制更有效。
FRAC MD提高工作效率
USWS公司对设备的高质量维护体现在最新技术FRAC MD上,该技术能够对设备进行诊断,降低由于设备疲劳等引起的设备损坏,降低非生产时间。公司技术人员表示:“有了这项技术,现场作业的可靠性得到了显著提高,我们能够更准确的做出预测,提高工作效率”。
关于 U.S. Well Service
USWS是一家专门为非常规油气田、天然气田提供高压水力压裂技术与服务的公司。该公司同时提供柴油压裂服务和电驱动压裂服务,具有多年的压裂经验,工艺成熟,能够满足各种压裂作业需求。
来自/US Wellservice等 译者/白小明 编辑/Lemon
Throughout the U.S. many operators are facing signifcant environmental regulatory pressures such as emissions, noise and silica dust. State and federal agencies are getting stricter with nonattainment areas and are tightening emission regulations for nitrogen oxides (NOX), carbon monoxide, methane and other emissions.
Noise pollution is likewise being more tightly regulated in multiple basins, specifcally how both high- and low-frequency noise affects residential communities as well as wildlife. Permissible exposure limits (PELs) for silica dust from proppant are being tightened over concerns about silicosis.
In this low-price commodity environment improvements to address these issues must be made while simultaneously looking to reduce overall costs and improve effciencies. New technologies such as Clean Fleet with Whisper—the first fully electric, fully mobile electric-powered hydraulic fracturing feet fueled 100% by field natural gas—delivers cost savings and addresses these environmental regulatory pressures.
Electric-powered fracturing
Traditional hydraulic fracturing feets are powered by more than 20 large diesel engines up to 2,500 brake horsepower (bhp) each. By removing all diesel engines from a pressure pumping site and replacing them with mobile turbine engine generator units, a feet can be run completely on electric power. This technology was first deployed in 2014 in the Marcellus Shale in West Virginia and has since also been deployed in Colorado. There are currently two active electric-powered feets in North America.
The electric feets are completely fueled by feld natural gas that is supplied from a pipeline. If need- ed, CNG or LNG also can be used as a fuel when feld natural gas is not available. Two large electric compressors boost the natural gas pressure to a constant 300 psi as required by the turbine engine generators. Combined, the compressors provide up to 84,950 cu. m/d to 113,267 cu. m/d (3 MMcf/d to 4 MMcf/d) for the mobile turbines.
The electric feets can run with the power from three or four turbines depending on the hydraulic horsepower (hhp) requirements to stimulate the well. Each one produces 5.67 MW of three-phase power at 13,800 v for a total of 17.01 MW to 22.68 MW electricity output at the International Organization for Standardization conditions. The power generated by the turbines then runs through
a set of switchgear trailers. These trailers distribute the electricity, provide circuit breakers and establish safeties in the equipment such as ground fault detection. The power then leaves the switchgear and is stepped down to 600 v using multiple transformers. Each transformer is a dry cast coil type rated for 3,500 kilovolt-ampere.
At this point the electric feets are similar to a conventional hydraulic fracturing feet except that all the feet’s diesel engines and transmissions are replaced by electric motors and variable frequency drives (VFDs). Each electric feet has eight dual hydraulic fracturing pump trailers that all run on 600-v power. Each dual pump trailer is rated at 3,500 hhp for a total of 28,000 hhp per feet. The dual pump hydraulic fracturing units have two independent triplex pumps.
On a traditional diesel-powered unit, a large radiator typically sits on the gooseneck. On the electric pump units the large radiator is removed, and in its place sits a VFD house with two independent VFDs. In addition to the electric pumps, blenders, hydration, data van, sand equipment and a silica dust suppression vacuum are all also completely electric powered.
Emission reduction
One of the most notable environmental benefts of the electric-powered feet is reducing emissions to near-zero levels. Excess NOX can lead to acid rain and contribute to unhealthy ground-level ozone and smog. The reduction is primarily achieved by eliminating the conventional diesel engines and using natural gas as a fuel. The emissions on the turbines were measured in the exhaust ports by a third party, and the NOX levels were found to be less than 0.036 g/kWh. This is a dramatic reduction when compared to Environmental Protection Agency requirements for off-highway diesel engines.
Natural gas is a cleaner fuel than diesel, and it produces fewer potential pollutants. Natural gas turbine engines also allow a continuously burning combustion chamber that results in a more complete burn, which greatly reduces emissions when compared to a diesel engine’s four- stroke cycle. The gas turbines have a signifcant advantage because they use lean premixed combustion technology to ensure a more uniform air and fuel mixture and to prevent the formation of regulated pollutants. Up to 60% of the airfow on the turbine engine is allowed to be pre- mixed with the fuel, resulting in a much more consistent air and fuel mixture.
Noise reduction
The Colorado Oil & Gas Conservation Commission has set strict noise regulations for both high-frequency and low-frequency noise. About one-third of all complaints received in 2015
in Colorado were related to noise. One of the electric feets operating in the Wattenberg Field in Colorado was measured to be 7 decibel A (dBA, A-weighting describes audible, higher frequency noises) and 12 dBC (C-weighting describes low-frequency vibration noises that can shake win- dows) quieter than a comparable diesel feet. This correlates to an 80% reduction in sound intensity on the dBA scale and a 95% reduction on the dBC scale.
Silica dust reduction
Both of the electric hydraulic fracturing feets have electric-powered dust control to reduce silica dust signifcantly below PEL requirements. Like the rest of the stimulation equipment, the dust vacuum system is powered by 600-v electricity. This engineered system reduces measured silica amounts up to 80% below PEL requirements. To increase safety, engineering controls like this are more effective at controlling hazards rather than merely using administrative controls or personal protective equipment.
Cost reduction, increased effciencies
Fueling the turbines with field natural gas reduces fuel costs by up to 90%. The turbines consumed an average of 3,030 cu. m (107 Mcf) of natural gas per hour while powering more than 10,000 hhp of fracturing equip- ment during stimulation. An equivalent diesel hydraulic fracturing feet can consume about 1,000 gal of diesel fuel in 1 hr of pumping. These dramatic fuel savings come from both the reduced commodity price of unfltered field natural gas over diesel fuel as well as not having trucking costs for the natural gas.
The electric motors used by the electric feets have their first maintenance period at 30,000 hours and an expected life of up to 20 years. Diesel feets will need to go back to the yard every other month for repairs and maintenance such as oil and filter changes that the electric feets do not have to do. The longer life, reduced maintenance schedule and increased pumping time are an important economical advantage.
VIBRATIONS
Clean Fleet® technology leads the way in advancing safety via reduced vibrations and fatigue of treating iron. Our electric fleet reduces high pressure iron vibrations by up to 80% as compared to diesel powered equipment. These results were validated by installing three dimensional (3D) accelerometers on diesel powered equipment and comparing this baseline to the accelerations recorded on the electric powered equipment (graphs below). This dramatic reduction in vibrations is achieved by replacing the engine and transmission with a VFD that controls the electric motor which is direct coupled to the hydraulic fracturing pump.
未经允许,不得转载本站任何文章:
-
- Demons
-
石油圈认证作者
- 毕业于中国石油大学(北京),化学工程与技术硕士,长期聚焦国内外石油行业前沿技术装备信息,具有数十万字技术文献翻译经验。如需获取更多技术资料,请联系Demons(QQ2582825239;微信15810965891)