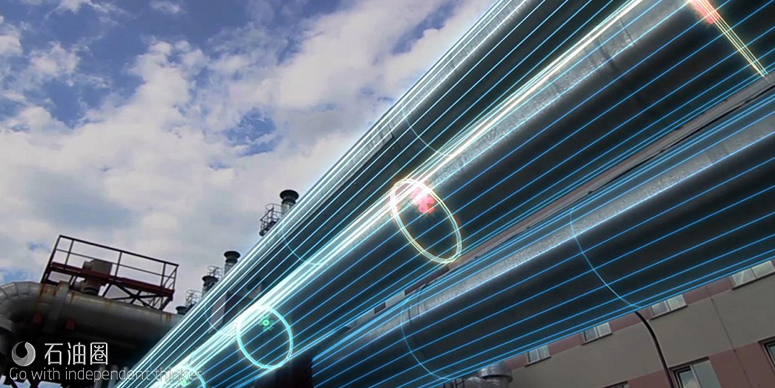
设备完整性一直是油气行业的关注重点,SGS与BHGE推出的腐蚀解决方案能够显著改善当前腐蚀监测中存在的问题。
来自 | BakerHughes
编译 | TOM 惊蛰
近日,SGS与贝克休斯(BHGE)共同宣布了一项战略联盟协议(SAA),将联合部署以及商业化应用BHGE的预测腐蚀管理(PCM)解决方案,PCM将以实时软件与传感器为基础。PCM凭借工业物联网(IIoT)优势,使资产所有者能够强化他们监控设备的能力。
通过BHGE超声波传感技术获取的实时数据,结合高级分析技术,检测与预测腐蚀问题。最近的休斯敦会议上,北美SGS首席运营官FrançoisMarti与BHGE检测技术首席执行官Holger Laubenthal,在客户与公司官员面前签署了该项战略联盟协议。
利用安装在关键设备(如管道,储罐以及容器)上的Rightrax PM超声波传感器,PCM能够生成壁厚与温度测量值。该解决方案采用高级分析技术,可以实时评估收集到的数据,常规方法是通过即冒险又耗时的人工检查来收集这些数据。PCM不仅对油气下游、石化以及上游作业者特别有价值,而且它还可以帮助任何受腐蚀风险影响的工业部门。PCM可以作为油气公司的重要工具,以提高设备的可靠性与完整性,同时最大限度地提高作业的安全性并延长设备寿命。
无论是在作业或停机检修期间,SGS都可为大型工业设备提供外部检查与无损检测服务,以确保工业设备的完整性。BHGE的检测技术是该公司数字解决方案部门的一部分,也一直是SGS的无损检测技术供应商之一,并可为工业设备拥有者提供关键的技术解决方案与服务。PCM技术将SGS的全球网点以及设备完整性专家与BHGE的技术专长相结合,将确保其快速部署,并扩大检查与维护技术服务的市场规模。
预测腐蚀管理 智能预测
PCM将云平台软件与Rightrax PM传感器结合到一个解决方案中,使油气企业能够无损监控管道内壁厚度,并主动减轻腐蚀与侵蚀的影响。PCM可智能管理腐蚀相关风险,将管道监控能力扩展至人工检查所能涵盖的范围之外,并最大限度地降低作业成本。
利用功能强大的软件包,上游、下游、电力以及化工设备的作业者能够以更高的频率监控管道内壁厚度,并可基于计划对设备进行精确的测量。它还有助于提高设施与人员的安全,无需中止关键作业流程,仅在必要时才会部署现场专业维护人员。
借助实时变化趋势与强大的可视化能力,用户可以针对关键设备的寿命与可靠性,做出积极主动的决策,从而降低作业总成本并提高安全性。
趋势观测 优化决策
PCM利用传感器数据可对管道内壁厚度与温度进行可重复、精确的测量。使用BHGE的Rightrax PM传感器,用户可以精确测量与监控炼油厂、化工厂以及上游应用中管道的内壁厚度与温度。数据流传输至云平台存储库中,能够提供可扩展的存储与计算分析。利用BHGE的高级分析与可视化技术,PCM可提供安全视图,显示出由于腐蚀与侵蚀而导致的当前以及预计管道内壁损失。PCM还拥有将作业数据与厚度数据相关联的能力,有助于提高用户的作业认知与决策能力,相比于同类技术,具备许多优点:
- 减轻腐蚀相关的风险:非侵入式监控管道内壁厚度
- 降低检查成本:降低难以触及或无法进入的位置的检查总成本
- 提高设备性能:通过减少过早更换管道来优化维护
- 改进/优化流程与作业:借助创新性分析(如腐蚀率与受监控设备的剩余寿命)做出明智的决策
- 优化化学抑制剂方案:防止过量注入,节约成本
- 提高人员安全:减少检查员暴露于难以触及的潜在危险场所
数字工业软件
PCM软件由Predix提供技术支持,这是GE Digital为工业互联网构建的云平台。通过传感器向云平台软件提供连续数据,用户可以提高检查的可靠性,消除手动误差,查看有助于提高操作意识与决策的趋势和预测,从而延长管道的使用寿命。目前软件可以提供以下功能:
- 空间分析,用于简单、深入的展示安装了传感器的设备的健康状况
- 实时查看腐蚀速率,温度与壁厚
- 传感器设备的健康监测
专家服务
与用户的工艺与可靠性专家以及腐蚀工程师合作,BHGE可协助用户为用户应用制定合适的解决方案。BHGE的服务包括应用评估、现场调查、部署、配置、安装与设置。
性能卓越的传感器
Rightrax PM传感器在最恶劣的环境中几乎无需维护。这些永久安装的传感器可以安装在难以到达的区域,从而降低脚手架与索具的成本。Rightrax PM传感器的薄型设计使它们可以安装在绝缘层下,减少重复且昂贵的绝缘层拆卸与更换。所有这些都意味着更少的人力与更可靠的数据。
- 超声波壁厚监测系统,用于检测管道的腐蚀与侵蚀
- 在使用过程中对管道、弯头、集管、甚至绝缘体进行持续的监控
- 专有的SolGel超声波探头技术,可用于干式耦合
- 安全的ATEX Zone-0认证组件
- 无需耦合剂、粘合剂或焊接即可安装,几乎无需维护
- 通过网页远程访问数据
您也有让人挠头的难题需要解决,或是优质技术想要找应用市场吗?如果有的话,欢迎联系小编微信或邮箱,也许能找到一剂良药。
二丫:022-65771089;131-3255-0596
For English, Please click here (展开/收缩)
SGS and Baker Hughes, a GE company have announced a strategic alliance agreement (SAA) for the joint deployment and commercialization of BHGE’s real-time software and sensor-based predictive corrosion management (PCM) solution. Leveraging the capability of the industrial internet of things (IIoT), PCM will enable asset owners to increase their ability to monitor their facilities, and detect and predict corrosion issues using real-time data powered by BHGE’s ultrasonic sensing technology and advanced analytics. François Marti, SGS COO, North America, and Holger Laubenthal, CEO, inspection technologies for BHGE, signed the SAA in the presence of customers and company officials during a recent conference in Houston.
PCM generates wall thickness and temperature measurements from Rightrax PM ultrasonic sensors placed on critical equipment such as pipes, tanks, and vessels; the solution applies advanced analytics, resulting in real-time assessment of data that has traditionally been gathered through risky and time-consuming manual inspections. While particularly valuable to oil & gas downstream, petrochemical, and upstream asset operators, PCM can help any industry segment challenged by corrosion-related risk. PCM is one essential tool to help asset owners benefit from enhanced plant reliability and integrity programs, while maximizing operational safety and extending asset life.
SGS provides visual inspection and non-destructive testing services to large industrial assets, both in-service and during regular shutdown events, helping to ensure industrial asset integrity globally. BHGE’s inspection technologies business, part of its digital solutions segment, has been one of SGS’ suppliers of non-destructive testing technology for years and is itself providing industrial asset owners with critical technological solutions and services. Combining SGS’ broad network and asset integrity expertise with BHGE’s technological expertise will ensure rapid deployment of PCM, and drive scale in the market for inspection and maintenance services and technology.
PCM
Transforming Inspection Data Into Predictive Intelligence
Predictive Corrosion Management (PCM) combines cloud-based software with Rightrax PM installed sensors into a single solution, giving oil and gas businesses the ability to non-intrusively monitor interior piping wall thickness and proactively mitigate the effects of corrosion and erosion. PCM delivers actionable intelligence for the management of corrosion-related risk, extending pipe monitoring beyond what manual inspections can cover and minimizing operations costs.
This powerful package allows operators in upstream, downstream, power, and chemical facilities to monitor interior wall piping thickness at a higher frequency and take precise schedule-based measurements in your facilities. It also helps improve the safety of the facility and the personnel, eliminates the need to shut down critical processes, and to deploy the field maintenance professionals only when necessary.
With real-time trends and robust visualizations, you can make proactive and informed decisions about the critical asset life and reliability—reducing the total cost of operations and increasing peace of mind.
Enabling better decisions with visibility and trending of interior piping wall loss
PCM draws on sensor data for repeatable, accurate measurement of interior piping wall thickness and temperature. Using BHGE’s Rightrax PM installed sensors, you can accurately measure and monitor the interior wall thickness and temperature of pipes in refineries, chemical plants, and upstream applications. The data is streamed into a cloud-based repository that can provide scalable storage and analytics computing. Using BHGE’s advanced analytics and visualizations, PCM delivers a secure view of current and projected interior piping wall loss due to corrosion and erosion. The ability to correlate process data with thickness data can help improve your operational awareness and decision making.
- Manage and mitigate corrosion-related risks: Non-intrusively monitor interior piping wall thickness
- Reduce inspection-related costs: Reduce the total cost of inspections for hard to reach or inaccessible locations
- Improve equipment performance: Optimize maintenance by potentially reducing early piping replacement
- Improve/optimize process and operations: Make informed decisions with the help of out-of-the-box analytics like corrosion rates and remaining life of monitored assets
- Optimize chemical inhibitor program: Save cost associated with over-injecting
- Improve personnel safety: Reduce inspector exposure to hard-to-reach, potentially dangerous locations
Software for the Digital Industrial world.
Predictive Corrosion Management software is powered by Predix™, GE Digital’s cloud-based platform built for the Industrial Internet. With the sensors feeding continuous data to the cloud-based software, you are able to improve the reliability of inspections, eliminate manual inconsistencies, as well as see trends and predictions that can help improve operational awareness and decision making—extending the run life of pipes across your facility. The software today provides the following capabilities:
- Geospatial analytics for simple, drill-down views of asset health where sensors are installed
- Real-time view of corrosion rates, temperature, and wall thickness
- Sensor equipment health monitoring
Expert services
Working with your process and reliability experts and corrosion engineers, we will help you define the right solution for your application. Our services include the application assessment, site survey, deployment, configuration, installation, and setup.
Sensors that go beyond the expected.
Rightrax PM sensors operate virtually maintenance-free in the harshest environments. These permanently installed sensors can be installed in hard-to-reach areas, reducing the cost of scaffolding and rigging. Their low-profile design can be installed under insulation, reducing repeated and costly insulation removal and replacement. All of which means less manpower, and more reliable data.
- Ultrasonic wall thickness monitoring system for pipe corrosion and erosion
- Continuous monitoring of pipes, elbows, headers, even under insulation—while in service
- Proprietary SolGel ultrasonic probe technology for dry coupling
- Inherently safe, ATEX Zone-0 certified components
- Installed without couplant, adhesives or welding, virtually maintenance-free
- Remotely access data via the web
未经允许,不得转载本站任何文章: