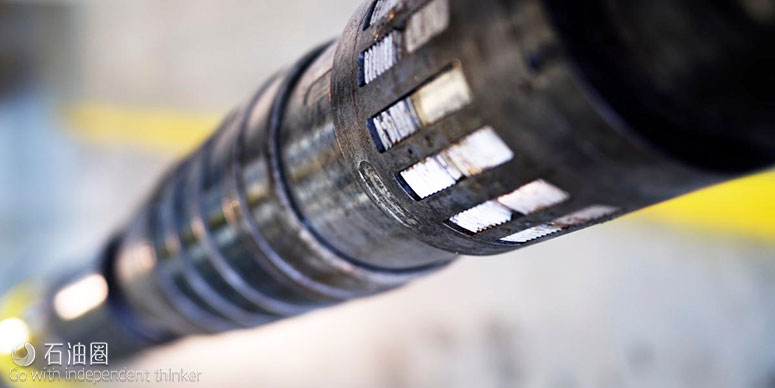
Archer公司研发出SPARTAN桥塞射孔(PNP)新系统,无需切割打捞套管,就能移除环空流体,极大降低了作业费用。
来自 | E&P
编译 | TOM
进行固井作业时,经常会在套管间留有环空流体,比如油基泥浆。在勘探阶段或油井寿终正寝的弃井作业时,如何移除这些环空流体总是另作业者抓耳挠腮。
为了切除并取出井口装置,必须要循环出存在于套管间的环空流体,还需要注入水泥塞形成环境屏障。环境隔离塞的作用是封隔井筒整个横截面,防止井筒内的流体进入到周围环境中。根据挪威石油工业技术标准关于钻完井作业的井筒完整性D-010条规定,井筒屏障需要拥有隔离环境的能力。
传统方法是通过注水泥弃井(P&A)作业期间切割与打捞套管来解决这个难题。例如,在注水泥弃井方案中,通常是在桥塞坐封前选择合适的井深,然后在20寸套管内切割并打捞13.375in套管。此后,注入水泥塞置于20寸套管内的桥塞上。在某些情况下,还需要铣削套管来布置环境隔离塞。
无需切割与打捞
切割与打捞套管是一项费时且费钱的作业。为了应对这一挑战,Archer公司研发了SPARTAN桥塞射孔(PNP)系统。在去除环空流体时,需要切割与打捞套管,并在环空与井筒中注入水泥塞(环境隔离塞或屏障),但这种基于井下工具的弃井系统无需如此,作业照样能够进行,并可以安全移除井口装置。
SPARTAN系统由ISO14310认证的 SPARTAN可回收式桥塞与两个独立激活的套管射孔枪组成。设计的射孔枪能够以受控的方式射孔,在穿透第一层套管的情况下,还不会影响第二层套管的完整性。
利用该系统,无需切割与打捞套管,就能实现循环出环空流体以及形成环境水泥塞的目标。作业的成果就是在两层套管间与井筒中设置了一个永久的屏障。
效率提升
采用传统切割打捞套管的方法进行注水泥弃井作业,大概需要21小时的作业时间。利用两趟PNP作业需要15.5个小时。若利用Archer公司的一趟式SPARTAN PNP系统进行PNP作业则只需要9.75个小时,因此将作业效率提高了50%以上。
该桥塞无需任何加重钻杆或是尾管来安装,这一特性使它成为大斜度井弃井作业的选择。该桥塞被设计为将射孔枪悬挂在它的下方,3寸的投球可以穿过它,进入到油管送入式射孔枪(TCP),然后激活射孔枪。该桥塞的主要特点与功能如下:
经过ISO 14310认证的桥塞;
快速安装与回收;
没有安装负载的限制;
单趟多次安装;
无限制的3寸通径;
超浅、超深或水平的作业范围:20米至6550米(65.6英尺至21489英尺);
与油管送入式射孔枪一起下入。
桥塞射孔方法
利用SPARTAN桥塞的PNP方法可以分为六个步骤(如下图):
(1)将工具下放到计划深度,对套管进行射孔;
(2)将工具下放到套管鞋上方(或计划深度),坐封桥塞并射孔;
(3)泵送管柱,建立深部射孔孔眼与浅部射孔孔眼的联系。当开泵循环时,流体会从深部孔眼进入到环空中,上返至浅部孔眼。泵入为注水泥作业准备的海水,循环替换出环空流体。
(4)将水泥浆通过钻柱注入到深部孔眼中。被替出的流体从浅部孔眼中流出。水泥浆穿过SPARTAN桥塞,被替入到孔眼中,环空B被水泥封隔。SPARTAN桥塞的一体式球阀关闭,因此无需钻柱利用U型管原理,就能水泥浆保持在原位。
(5)当替入水泥以及球阀关闭后,送入工具与桥塞脱离,然后通过送入工具,在SPARTAN桥塞的上方布置一个平衡的水泥塞。这就完成了设置屏障的作业。在这个阶段,环空A与环空B都形成了屏障。
(6)水泥凝固后,可以进行承压实验来验证屏障的效果。SPARTAN系统的一个特点是,环空A与环空B都能够进行承压实验与验证。在这个阶段,环空流体已经被循环出去,也设置了环境屏障,而且整个作业过程没有移除任何管柱。同样还能根据挪威石油工业技术标准D-010规定,安全的拆除井口装置。
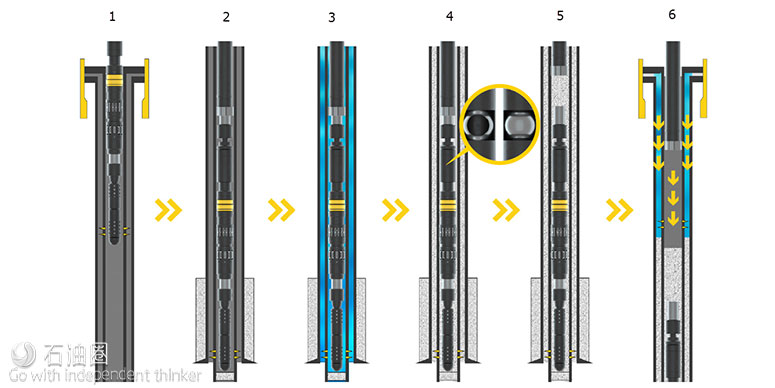
图. SPARTAN桥塞射孔方法可确保在两个环空中形成永久的屏障,而且无需进行切割与打捞作业。
案例分析
SPARTAN桥塞射孔系统已经运用于北海的数个注水泥弃井作业中。在其中某个作业中,该系统为欧洲主要作业者节约了近3百万美元,以及11天的工期。
当该井钻进时,9.625寸套管发生卡钻,无法通过管鞋建立循环。作业者决定注水泥弃井,然后进行侧钻。作业者着手开始回收4577米(15016英尺)的套管,但进展缓慢。花费了21天,才只切割打捞出3182米(10439英尺)的套管。因为该井的井斜角为73度,打捞落鱼作业是一项严峻的挑战。作业者急需探索出另一种技术方案,来完成注水泥弃井作业。
第一步便是下入并坐封SPARTAN桥塞于4852米(15918英尺)的位置,为注水泥提供通道,同时还能隔离井筒底部。当该桥塞下入裸眼段约900米(2952英尺)处,位于9.625寸套管落鱼上方。按照计划与流程坐封该桥塞,并起出下入工具。第二步是下入第二个桥塞与TCP射孔枪,然后在4838米至4840米(15872英尺至15879 英尺)处进行射孔,平均每英尺12发射孔弹。将另一个SPARTAN桥塞坐封于4824米(15826英尺处),并在9.625寸套管环空中建立循环。
第三步也是最后一个阶段。注水泥穿过SPARTAN球阀,进入到射孔孔眼中,上返至4342米(14245英尺),形成对9.625寸套管环空的封固。当替入水泥结束时,管柱中保持压力。在这个阶段,关闭SPARTAN球阀,阻止环空中的水泥流动。最终在套管内形成两个水泥塞,封固至4390米(14402英尺),以完成注水泥弃井作业。
您也有让人挠头的难题需要解决,或是优质技术想要找应用市场吗?如果有的话,欢迎联系小编微信或邮箱,也许能找到一剂良药。
二丫:131-3255-0596;zhanglingyu@cnoocraiborn.com
大安:131-3203-1392;lishian@cnoocraiborn.com
For English, Please click here (展开/收缩)
PNP System Improves P&A Efficiency
A system has been developed to deliver cost savings by removing the need for cutting and pulling a casing when removing annular fluid.
Operators are looking for well barrier solutions that are cost-effective, robust and in accordance with industry regulatory standards. An industry challenge when plugging and abandoning wells during exploration and at the end of a well’s lifetime is to remove annular fluid, such as oil-based mud, between two casing strings, when creating a well barrier that can be documented and verified.
To cut and pull the wellhead, the annular fluid between the casings must be circulated out, and a cement plug needs to be set as an environmental barrier. An environmental isolation plug functions to isolate the full crosssectional wellbore and to prevent the movement of wellbore fluids to the environment. A well barrier may also function as an environmental isolation plug, according to the NORSOK Standard D-010 on well integrity in drilling and well operations.
Traditionally this challenge was solved by cutting and pulling the casing during plug and abandonment (P&A) operations. For example, in a P&A scenario, a 133⁄8-in. casing can be typically cut and pulled at an appropriate depth inside a 20-in. casing in a well prior to setting a bridge plug. Thereafter, a cement plug can be placed on top of the bridge plug inside the 20-in. casing. In some cases, casing milling is required to set an environmental isolation plug.
Eliminating cutting and pulling
Cutting and pulling the casing can be time-consuming and costly. To address this challenge, Archer has developed the SPARTAN plug-and-perf (PNP) system. This downhole tool-based abandonment system eliminates the need for cutting and pulling a casing when removing fluid from the annulus and replacing it with a cement plug (environmental isolation plug or barrier) in the annulus and wellbore. Operations can then proceed and the wellhead can be removed.
The SPARTAN system consists of the SPARTAN ISO 14310 certified retrievable bridge plug and two separate activated single casing perforation guns. The guns’ design enables the first casing to be perforated in a controlled manner without compromising the integrity of the second casing.
With this system, the objective of circulating out annular fluid and setting the environmental cement plug can be met without cutting and pulling. The result is that a permanent barrier is set between two casings and in the wellbore.
Achieving efficiency
The operational time of establishing an environmental P&A plug by implementing a traditional cut-and-pull method is about 21 hours. A twotrip PNP operation takes about 15.5 hours. A PNP operation using the one-trip SPARTAN PNP system takes 9.75 hours, thus improving efficiency by more than 50%.
The plug does not require any weight/tail pipe to set, making it a choice for deviated wells. The plug is designed to hang perforation guns below, and the 3-in. ball valve enables activation balls for perforation guns to be dropped through the plug to fire the tubing-conveyed perforating (TCP) guns. Key features and capabilities include
- ISO 14310 certified barrier plug;
- Rapid set and retrieval;
- No weight below to set;
- Multiple sets without tripping;
- Unrestricted 3-in. fullbore;
- Ultrashallow, ultradeep or horizontal set 20 m to 6,550 m (65.6 ft to 21,489 ft); and
- Designed to be run with TCP guns.
PNP method
The PNP method leveraging the SPARTAN plug can be summarized in six steps:
- Run in hole and perforate the casing at planned depth;
- Run in hole to just above casing shoe (or at planned depth) to set the plug and perforate;
- Pump down the string to establish communication between the deep and shallow perforations. When pumping, the fluid will circulate out the lower perforations into the annulus, up and out the upper perforations. Circulate out and displace annular fluid to seawater to prepare for the cement job;
- Displace the cement slurry through the drillstring and into the deep perforations. Returns are taken through the shallow perforations. By displacing the cement through the SPARTAN plug and into the perforations the B annulus is cemented. The integral ball valve in the SPARTAN plug is closed so the cement will stay in place without U-tubing back up the drillstring;
- After the cement is placed and the ball valve is closed, the running tool is released from the plug, and a balanced cement plug is pumped through the running tool on top of the SPARTAN plug. This completes the barrier. At this stage, a barrier is complete in both the A and B annuli; and
- After the cement is set, the barrier can be verified through pressure testing. A feature of the SPARTAN system is that as a result of the shallow perforations, both the A and B annuli can be pressure tested and verified. At this stage, the annular fluid has been removed and the environmental barrier is in place—all without removing the tubular. The wellhead can be removed safely, in accordance with NORSOK Standard D-010.
Case study
The SPARTAN PNP system has been implemented in several North Sea P&A operations. In one P&A operation, the system saved a major European operator nearly $3 million, or 11 days of rig time.
When drilling the well, the 95⁄8-in. casing became stuck and no circulation was possible through the shoe. The decision was made to plug and abandon the wellbore and facilitate a new sidetrack. The operator started recovering 4,577 m (15,016 ft) of casing and achieved limited progress. The operator then spent 21 days cutting and pulling 3,182 m (10,439 ft) of the casing. The openhole fishing operation with a well profile of 73 degrees inclination proved to be challenging. The operator needed to explore an alternative technical solution to complete the P&A operation.
The first step of the operation was to run down and set a SPARTAN plug at 4,852 m (15,918 ft) to provide a path for the cement and to isolate the bottom of the hole. The plug was run through approximately 900 m (2,952 ft) of open hole before it entered the 95⁄8-in. casing fish. The plug was set according to plan and procedure, and the running tool was pulled out of hole. The second step was to run the second plug with TCP guns, then perforate the casing between 4,838 m and 4,840 m (15,872 ft to 15,879 ft) with 12 shots per foot 0,5 holes. Part of the job was to set the SPARTAN at 4,824 m (15,826) and circulate the 95⁄8-in. casing annulus.
The third and last stage was to cement the 95⁄8-in. casing annulus up to 4,342 m (14,245 ft) through the SPARTAN ball valve and into the perforations and up. At the end of the cement displacement, the pressure was held inside the string. At that stage, the SPARTAN ball valve was closed to stop the cement from U-tubing from the annulus. Two cement plugs were set inside the casing up to 4,390 m (14,402 ft) to complete the P&A operation.
未经允许,不得转载本站任何文章: