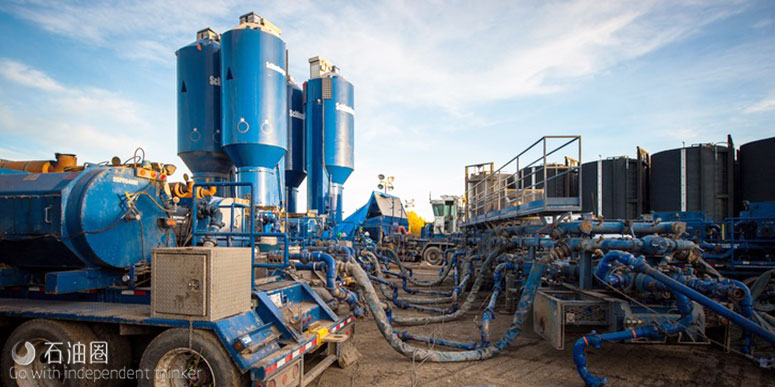
开发商正在努力优化完井作业,以期进一步降低开发成本。在当前进行的大多数水力压裂作业中,开发商都选择使用无涂层的压裂砂,虽然这些井也能够正常生产,但实际研究表明,通过使用新型的树脂涂层支撑剂,井筒的经济效益将进一步提高。
来自 | World Oil
编译 | 张德凯
昨天的【石油科技】板块,小编对目前低油价下的石油开采状况进行了分析,并简要阐述了树脂涂层支撑剂的技术优势。今天,小编将就几个典型的先进支撑剂技术案例做介绍。
新型支撑剂降低桶油成本
目前,油气行业在完井过程中面临着许多挑战,其中包括提高原油产量、减少不地层水 产出、增加裂缝导流活性等。新型树脂包覆支撑剂出现后,桶油成本明显降低,同时其应用优势远非常规涂层技术可比。
增加产量
开发商的最终目标是同时实现桶油成本降低和产量提高。高级支撑剂技术是一种行之有效的方法,相较于传统支撑剂,新技术专为增产设计。Hexion采用先进树脂技术推出了OilPlus支撑剂 (图2),在北美所有的大型油藏开采中都起到了增产作用。相对于传统的涂层、陶瓷及非涂层支撑剂,使用OilPlus的油井产量更高。
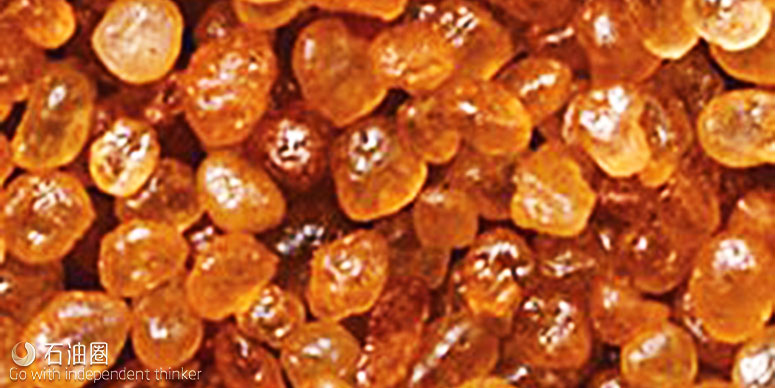
图2.OilPlus树脂涂层支撑剂,增产作用明显优于传统支撑剂
该公司的专利技术提高了支撑剂填充层对油的渗透率,在使用传统支撑剂时,水会附着在支撑剂表面,堵塞油气流动通道。若使用新型支撑剂,水不会依附在颗粒表面,支撑剂填充层的孔道更加清晰,增加了油气流动能力。
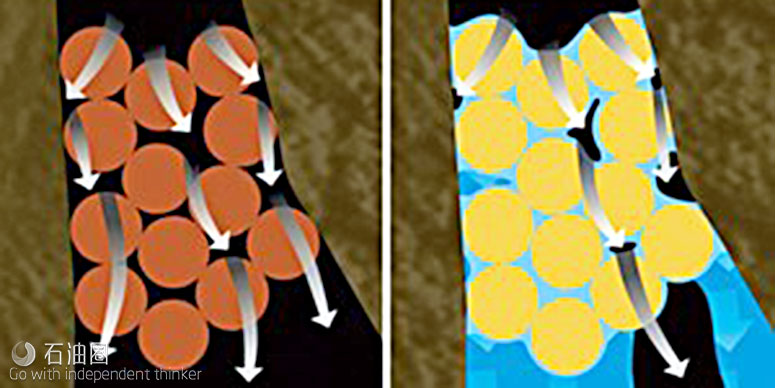
图3.OilPlus(左)与传统支撑剂(右)的导流性能对比

图4.井筒产量增加,证明了OilPlus支撑剂的有效性
根据开发商的生产数据,倘若在之前的完井中也使用了该支撑剂,收益将会提高333万美元。鉴于OilPlus在Permian盆地的成功案例,负责测试项目的完井工程师继续向其他开发商推荐使用OilPlus进行完井作业。毫无例外,使用OilPlus的开发商也确实得到了更高的收益。
降低地层水产出
对于北美的油气开发商来说,压裂增产后的伴生地层水处理是个巨大挑战,废水处理增加了成本,在美国,每生产一桶原油就会平均伴生5~6桶地层水。以Permian盆地为例,每采出一桶原油就会得到6~8桶地层水。由于地层水富含矿物质、油渣、盐类等物质,处于安全和环保考虑,开发商必须妥善处理这些废水。
完井作业频率提高直接导致了用水强度和地层水产量的增加,在一些开采关键地区,含盐废水回注井(SWD)容量不足极大的限制了油气生产。SWD一般靠近地层水产出量巨大的生产井,由于容量告急,开发商不得不将废水运输至更远的地区处理,废水处理成本直线上升。假定石油价格保持稳定,预计Permian盆地的地层水产量每月可能增加至50 MMbbl。如果油气产量增加速率一直如此,那么每个月需要将大约70 MMbbl的产出水转移至新的设施处理或再生利用。
与传统支撑剂相比,在不降低油气产量的前提下,Hexion的AquaBond支撑剂采用了一项特殊的减少地层水产出技术。对每口井来说,地层水产出量降低就意味着成本降低。AquaBond的新型树脂涂层具有独特化学性质,改变了支撑剂外层对水和油流动的渗透性,油更容易通过支撑剂填充层。AquaBond能够在井筒的生命周期内发挥作用,而降低地层水产量只是的特点之一。
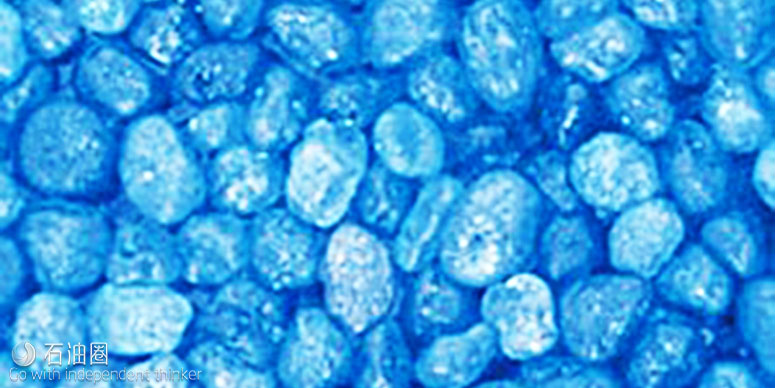
图5.与传统支撑剂相比,AquaBond支撑剂显著降低地层水产出量
地层水产出降低案例
在Oklahoma和Texas州的Granite Wash区块,对涂层支撑剂降低地层水产出能力进行了对比,其中一口井使用了23%的AquaBond支撑剂,另外三口探边井则全部使用无涂层压裂砂。几口井的支撑剂总用量、井深、分支井情况都基本相同,完井作业由同一家服务商在同一时间段内完成。在接下来的9个月里,使用AquaBond支撑剂的井筒地层水产出量要比另外三口井的平均产水量低约26000桶,如图6所示。同时,该井的原油产量则是另外三口井平均水平的三倍,效果显著。
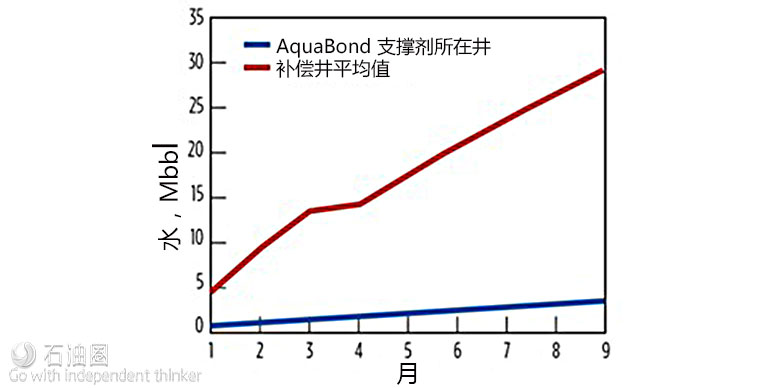
图6.地层水产出曲线显示新型支撑剂使用后其产量下降明显
kRT 100是一种新型支撑剂,转为微小裂缝增产设计,同时具有树脂涂层支撑剂的所有其他功能,kRT 100的树脂涂层支在裂缝中使用100目的颗粒。与无涂层的压裂砂相比,kRT 100具有树脂涂层支撑剂的所有有点,比如减少反排、降低支撑剂磨损以及减少支撑剂嵌入等。因为这些小的kRT 100颗粒粘结在裂缝中,组织了支撑剂充填层的变化,稳定性更强。粘结性能测试显示,kRT 100颗粒在130 ?F即建立了颗粒间的链接,无涂层的支撑剂则无法建立粘结。
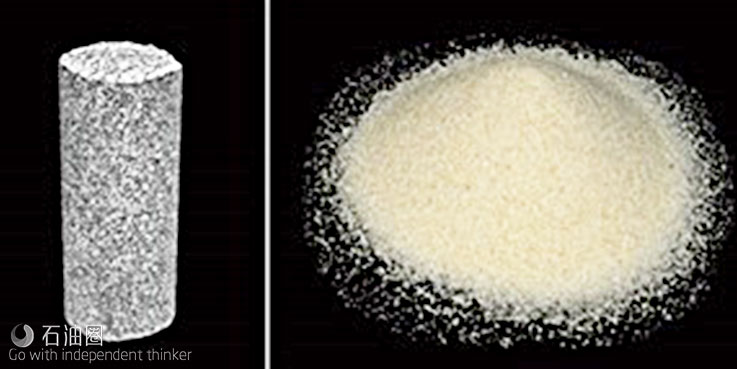
图7. kRT 100树脂涂层支撑剂粘结形成填充层,增加了裂缝的导流能力
结论
如今,开发商正专注于优化完井方案,以进一步降低成本。目前绝大多数的水力压裂作业都使用无涂层压裂砂,虽然也能保持不错的产能,但使用涂层支撑剂能够更显著的提高开发效益。使用非涂层压裂砂对成本的影响几乎可以忽略,而使用树脂涂层支撑剂则会提高产量,带来长期经济效益。产量的下降清楚地表明,非涂覆支撑剂在持续压力作用下会逐渐失效。相反,树脂涂层技术可以改善这种状况。
相对于非涂层压裂砂,传统树脂涂层支撑剂具有很多优势,如减少反排、提高孔隙率和裂缝导流能力等。而先进的树脂涂层支撑剂能够提供更多的应用优势,如增加产量、减少地层水产出以及利用颗粒粘合来维持裂缝导流能力。与传统涂层技术相比,泵入采用新型技术的支撑剂对于提高产量、降低桶油成本非常有效。
您也有让人挠头的难题需要解决,或是优质技术想要找应用市场吗?如果有的话,欢迎联系小编微信或邮箱,也许能找到一剂良药。
二丫:131-3255-0596;zhanglingyu@fonchan.com
大安:131-3203-1392;lishian@fonchan.com
For English, Please click here (展开/收缩)
ADVANCED PROPPANTS CAN REDUCE COST PER BOE
Today’s oil and gas industry continues to face many challenges during well completions, some of which include increasing oil production, reducing unwanted formation water production, and increasing microfracture stimulation. New resin technology has helped operators to reduce cost per boe beyond the benefits of traditional resin-coated proppants.
Increased oil production. An operator objective is to increase oil production while reducing the cost per boe. One proven way to accomplish this is by using advanced proppant technology, designed specifically to increase oil production over traditional proppants. Hexion’s OilPlus proppants have advanced resin technology that has yielded years of enhanced oil production in all the major plays of North America. They provide higher oil flowrates compared to traditional resin-coated proppants, ceramics, and uncoated frac sand.
The company’s patented technology increases proppant pack relative permeability to oil. When traditional proppants are used, water adheres to their hydrophilic surfaces, blocking pathways for oil and gas to flow. With the new proppant technology, water does not cling to the surface of the proppant. This allows a clear path through the proppant pack, resulting in increased flow of hydrocarbons, compared to traditional proppants.
The company’s patented technology increases proppant pack relative permeability to oil. When traditional proppants are used, water adheres to their hydrophilic surfaces, blocking pathways for oil and gas to flow. With the new proppant technology, water does not cling to the surface of the proppant. This allows a clear path through the proppant pack, resulting in increased flow of hydrocarbons, compared to traditional proppants.
If the operator had used the new proppants on the other wells, they would have yielded an additional $3.33 million in revenue. The completion engineers responsible for these wells moved to other operators and continue to pump these proppants, due to the success they experienced in the Permian basin. They continue to see financial value in utilizing the new proppant technology through all market cycles.
Reducing formation water production. The formation water produced after hydraulic fracturing is a challenge to most operators in North America. The disposal of unwanted formation water increases the cost of boe per well. In the U.S., formation water produced averages around 5 to 6 bbl of water for every barrel of oil produced. The Permian basin, for example, produces 6 to 8 bbl of water per barrel of oil. And because this water is full of minerals, petroleum residue, and salt, producers must dispose of the water in a safe and environmentally responsible manner.7
The rise in completion activity has led to an increase in water intensity and formation water production. The basin’s saltwater disposal well (SWD) capacity is facing heavy constraints in key areas. As SWDs—that are near a well, that is producing high volumes of produced water—reach capacity, operators have to transport water to more distant locations for disposal. This has led to a material increase in water disposal costs. Presuming that the price of oil continues to stabilize, it is estimated that water production in the Permian basin could increase by as much as 50 MMbbl each month. If production increases by this amount, approximately 70 MMbbl of produced water would need to be diverted from current disposal facilities to new facilities, or be diverted for reuse.
Without compromising oil and gas production, Hexion’s AquaBond proppants have advanced technology specifically designed to reduce formation water production, compared to traditional proppants. The lower water production results in reduced cost per boe, per well. The innovative resin chemistry of these unique proppants alters the relative permeability of the proppant pack for preferential flow of hydrocarbons over water. The water-reducing properties are part of the chemistry of these resin-coated proppants, which provides water reduction benefits over the life of the well.
Reduction in produced water case study. In the Granite Wash formation of Oklahoma and Texas, production from one well, that used a 23% AquaBond proppant tail-in, was compared to three offset wells that used 100% uncoated frac sand. Total proppant volumes, depths, and lateral lengths were all similar, and the wells were all completed for the same operator in the same time period. Over nine months, the well with the new proppant produced approximately 26,000 fewer barrels of water than an average of the offset wells. The well also produced more than three times the boe than the average of the offsets.
A new innovative solution, kRT 100 proppant, was developed to stimulate microfractures, while providing all of the advantages of a resin-coated proppant. The resin coating supports the intended use of 100-mesh grains within the fracture network. These proppants now provide all of the benefits of a resin-coated proppant, such as mitigating proppant flowback, limiting proppant fines, and reducing proppant embedment, compared to uncoated frac sand. Because these small proppants bond in the microfractures, they also keep proppant rearrangement from occurring. A bond strength test showed that these proppants bonded into a unified proppant pack at 130?F, while uncoated frac sand does not form bonds.
CONCLUSIONS
Operators today are focused on optimizing completions to further drive down the cost per boe. The vast majority of hydraulic fracturing jobs are using uncoated frac sand. While these wells can produce sufficiently, well economics could be improved by utilizing resin-coated proppants. The initial cost-savings of uncoated frac sand are negligible, compared to the long-term benefits of increased production that can be seen from resin-coated proppants. Production declines clearly show that the continued stress on uncoated frac sand causes the grains to fail over time. Conversely, resin-coated proppant technology is proven to improve EUR.
Traditional resin-coated proppants can provide many benefits over uncoated frac sand, such as mitigating proppant flowback, along with providing high porosity and fracture conductivity. However, advanced resin-coated proppants can offer additional solutions over traditional proppants, such as increasing oil production, reducing unwanted formation water, and propping microfractures with grain-to-grain bonding. Pumping proppants with innovative technologies can improve well production and reduce cost per boe, compared to traditional proppants.
未经允许,不得转载本站任何文章: