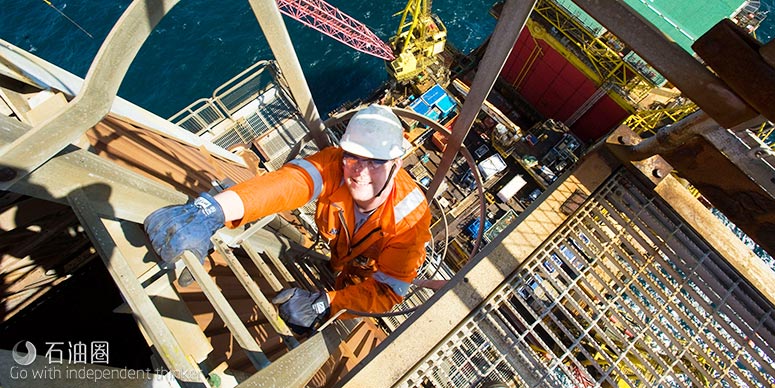
膨胀工具的技术进步,已使其成为了作业公司在整个油气井生命周期中值得依靠的一项技术。
来自 | TAM International
编译 | 白小明
膨胀封隔器的主要用途之一是在建井时的固井阶段。膨胀元件紧贴在套管上,作为多级固井或井底固井作业的底部支撑,当然这只是膨胀工具最常见的用途之一。在油气井生产阶段要进行修井作业时,如果使用机械桥塞或封隔器存在井下限制,通常需要使用膨胀工具。
例如,可膨胀工具可以采用电缆从生产油管内下入做封堵之用,或者可以与连续油管连用进行过油管挤注作业。通常,过油管作业比较理想;否则,作业公司必须进行压井以实施油井干预作业。另外,在裸眼完井需要进行油井测试或堵水时,可膨胀工具也非常适用。对于海上油井,膨胀工具也是P&A作业经常需要进行的切割锻铣工作的理想工具。
套管环空封隔器
套管环空封隔器(CAP)制造加工在标准的API套管上。CAP的组成包括阀套(被固定到在套管壁外)、膨胀元件和滑动端。在膨胀过程中,封隔器的一端滑动以增大外径。CAP最常用于多级固井或底部固井,在CAP之上连接一个多级固井工具或固井开孔短节,以使水泥返到地面。CAP常用于中间套管,因为井底压力低,水泥无法返至地面。
这些井段通常快速钻成,井径未测量,因此井眼通常冲蚀严重。尽管操作人员希望每次都能将封隔器坐封在井径经过测量的井段,但有时封隔器坐封在冲蚀井段时可能导致膨胀元件过度膨胀,最终破裂。此外,如果环空存在漏失,很难重新获得套管的完整性,因为套管内径CAP处的静液压力大于环空静液压力。阀套用于在破裂的情况下锁定膨胀元件,通常压力过平衡情况下不会出现这种情形。虽然经验表明这是低概率事件,但我们需要针对各种可能性制定解决方案。
为了解决压力不平衡情况下无法关闭阀门的问题,需要采用新的阀门设计。
新型关闭阀
为此,阀套融入了新技术,以保证冗余性,确保封隔器坐封后,无论环空液位如何,都能保证套管的完整性。该技术正在申请专利,尺寸涵盖各种套管环空封隔器,已在Permian盆地9-5/8-in井的中间套管进行了现场试验。无论是在Permian盆地还是其他应用中,通常环空液位较低,或中间套管井段环空存在漏失。
双级固井作业首先是利用浮鞋进行一级固井作业;投胶塞坐落在浮箍上,打压,使CAP膨胀。CAP坐封后继续打压,将分级固井工具打开;接下来投入开启塞;然后进行第二级固井作业,水泥泵送完毕后,投关闭塞坐落在分级固井工具上以将其关闭。如果封隔器破裂,启动新阀门以确保套管完整性。对于此项作业,常规的应急预案通常要等待几个小时使水泥凝固,然后再打开分级固井工具进行二级固井。
图4显示了Permian盆地井的典型井身结构,9-5/8in中间套管下通常是8-1/2in的水平段。CAP的密封元件长10ft,上部接有分级固井工具。按设计膨胀封隔器后,成功实现了二级固井作业。服务提供商的新技术可以确保即使发生小概率的封隔器破裂事件,通过启动新阀系统仍然可以立刻重新建立套管完整性。

图4.上图展示了Permian井表层和中间套管方案,井身结构为9-5/8in套管下为8-1/2in水平段
过油管电缆干预作业
可以使用电缆或钢丝来坐封膨胀桥塞或封隔器,采用电池供电系统部署和坐封工具,通过马达/泵总成,采用井下电子元件来控制膨胀过程。作业人员根据坐封井深对作业成功率的重要程度来选择使用电缆或钢丝。坐封井深非常重要的情形则采用电缆,因为可以下入伽马射线和套管节箍定位器,以便在坐封工具之前进行较深。
实际作业中可能需要桥塞或封隔器中的一种。在使用封隔器的情况下,通常使用隔离尾管来隔离井内某一段,近期有一个案例属于这种情况。一口深水井“A”环空出现压力变化,监管机构要求作业公司确定位置并进行堵漏。经分析确认是一个隔离封隔器出现泄漏。一种解决方案是动员一部钻机,起出上部完井工具然后更换隔离封隔器。
但这口井属于一口低产量(1,500 bpd)的老井,采用昂贵的钻机修井作业不经济。因此,作业人员考虑使用电缆系统部署膨胀封隔器的无钻机作业,如图5。选择膨胀技术是因为完井段存在内径限制,传统的机械封隔器无法通过。出现泄漏的隔离封隔器位于开孔短节之上。推荐的方案为一次入井在开孔短节之下坐封一个封隔器,然后再坐封一个上部封隔器,上部封隔器下面接着一段无孔管,以便插入到下部封隔器的顶部。这样就可以将开孔短节隔离,允许流体经无孔管总成流过。
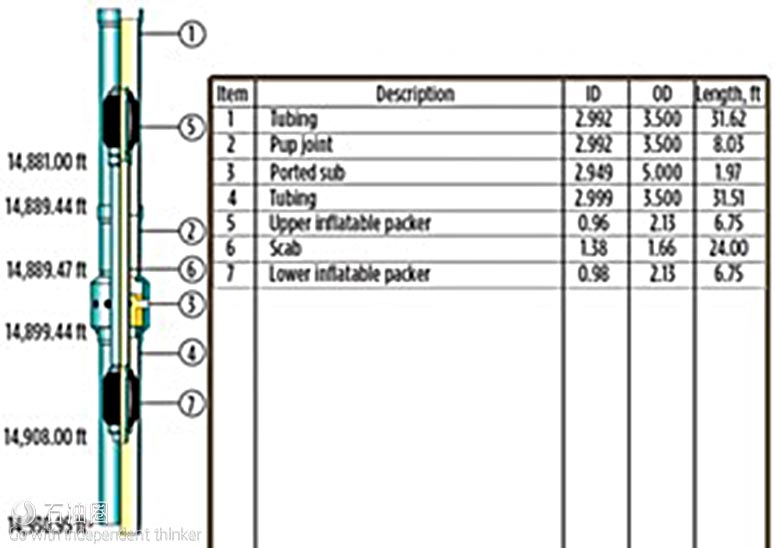
图5.电缆部署带膨胀封隔器的BHA的详细图
下封隔器坐封后,在其顶部预留有回接筒(PBR),以便上封隔器插入,上封隔器插入PBR后与其锁定在一起。锁定机构中的剪切销允许该总成可以回收。在本案例中,成功坐封了封隔器。无孔管就位后,井筒恢复生产,产量逐渐恢复到之前的1500bpd。“A”环空未出现压力变化,满足了监管机构的要求。此次干预作业的成本仅为钻机解决方案成本的约5%。可扩展的补救措施是处于生产后期阶段,即产量和压力已经降低的海上开发井的理想选择。
您也有让人挠头的难题需要解决,或是优质技术想要找应用市场吗?如果有的话,欢迎联系小编微信或邮箱,也许能找到一剂良药。
二丫:131-3255-0596;zhanglingyu@fonchan.com
大安:131-3203-1392;lishian@fonchan.com
For English, Please click here (展开/收缩)
CASING ANNULUS PACKER
A casing annulus packer (CAP) is manufactured onto a joint of standard API casing. The components of a CAP include a valve sleeve (which is fixed to the OD of the casing), the inflation element, and a sliding end. During inflation, one end of the packer slides to allow the OD to increase. The most common CAP application is for secondary cementing or off-bottom cementing, where a stage tool or cementing port collar is placed above the CAP to allow the pumping of cement to the surface. The CAP is often used on intermediate casing strings, when it is not possible to get cement to the surface, due to low bottomhole pressure.
These wellbore sections are typically drilled fast and not calipered, and therefore large wash-outs are common. While every effort is made to place the packer in a gauged section, sometimes the packer is set in a washout, which may result in over-expansion, causing the inflation element to rupture. Furthermore, if the annulus is on losses, regaining casing integrity can be difficult, because there is more hydrostatic pressure at the CAP on the ID of the casing than on the annulus. The valve sleeve is designed to lock-out in the event of a rupture, but an overbalance scenario can prevent this. While experience shows that this is a low-frequency event, the possibility of an occurrence requires a solution.
To address the inability to shut the valve, in the described unbalanced scenario, a new valve design was required to protect against this scenario.
New shut-in valve. To solve the issue, new technology was incorporated into the valve sleeve to provide redundancy, to ensure casing integrity is maintained once the packer is set, no matter the fluid level in the annulus. The technology is patent-pending and available in any size of casing annulus packer. Field trials have been successful in the Permian basin, in wells with 9 5/8-in. intermediate casing. In the Permian basin, and in other applications, it is common to have a low fluid level in the annulus, or for the annulus to be on losses in the intermediate casing section.
The basic operation for a two-stage cement job is to pump the primary cement job through the float shoe. Then, the wiper dart lands on the float collar and pressure is increased to inflate the CAP. After the CAP is set, additional pressure is applied to open a stage tool. Following, an opening plug is dropped. The second stage job is then pumped and a closing plug lands on the stage tool to close it. In the event of a ruptured packer, the new valve sub is activated to ensure casing integrity. The contingency plan at this point is typically to wait a few hours for the cement to setup on the primary job before opening the stage tool to pump the secondary job.
The CAP has a 10 ft seal with a stage tool on top. The packer was inflated as designed and the secondary cement job was successfully pumped. The service provider’s new technology ensures that in the unlikely event of a ruptured packer, casing integrity can be immediately reestablished by activating the new valve system.
THRU-TUBING WIRELINE INTERVENTION
An inflatable bridge plug or packer can be set using wireline or slickline. A battery operated system is used to deploy and set the tool. Downhole electronics are used to control the inflation process through a motor/pump assembly.
Depending on how critical an exact setting depth is to operational success, the operator can use a wireline or a slickline. For applications where the setting depth is critical, wireline is used because it can run a gamma ray and casing collar locator for correlation prior to setting the tool.
A solution may require either a bridge plug configuration or a packer configuration. In the case of a packer, the application is typically to use a scab liner to isolate a section of the wellbore. A recent case history required such an approach. A well in deep water experienced pressure on the “A” annulus and regulators required the operator to locate and repair the leak. It was determined that an isolation packer was leaking. One option would have been to mobilize a rig and pull the upper completion to replace the isolation packer.
But this was an older well producing at low flowrates (1,500 bpd), so an expensive intervention with a rig was considered uneconomical. A rig-less operation therefore was considered using inflatable packers deployed on a wireline system.
Inflatable technology was chosen because a restriction in the completion would not allow conventional mechanical packers to pass. The leaking isolation packer was positioned above a ported sub. The proposed plan was to set a packer below the ported sub on one run, and then set an upper packer equipped with a blank interval of pipe beneath it, to “sting” into the top of the lower packer. This would isolate the ported sub while allowing flow through the scab assembly.
The upper packer assembly was designed to sting into a polished bore receptacle (PBR) that had been left looking up after the lower packer was set. The upper packer assembly was then latched into the PBR. Shear pins in the latching mechanism allowed this assembly to be retrievable. In this case, the packers were set successfully. Once the scab liner was in place, the well was put back on-line and slowly ramped up to the previous 1,500 bpd production rate. No pressure was seen on the “A” annulus meeting the regulator requirements. This intervention was done at approximately 5% of the estimated cost of a rig-based solution. The expandable remedy is ideal for offshore developments that are in the later stages of production, where flow rates and pressures have been reduced.
未经允许,不得转载本站任何文章: