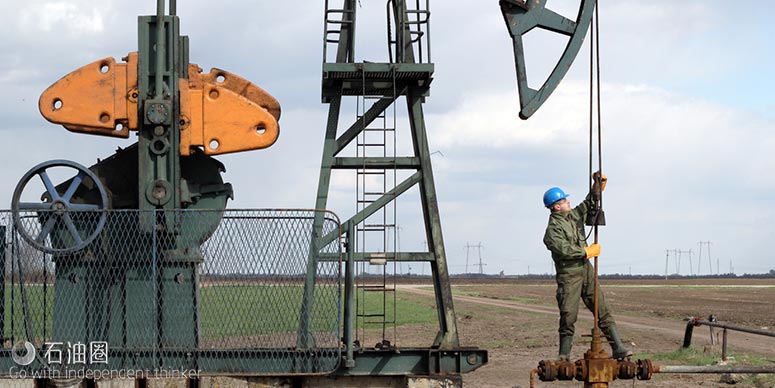
石器时代的结束,并不是因为石头没有了,而是技术迭代的结果。
来自 | E&P
编译 | 张毅
根据贝克休斯公布的消息,北美的可作业钻机数量在过去的一年间增长了124%,这一高速增长的原因,几乎可以完全归功于页岩油气的生产。北美总作业钻机数量的40%都扎堆在页岩油气爆发的震中—二叠纪盆地。
这些新增钻机在页岩油气的开发中为油气产量带来了大幅提升,其中,美国产量现已达到9.3MMbbl/d,这是自20世纪60年代后期、70年代初期之后首次达到的产量巅峰。
美国油气产量之所以能在油价低于60刀的环境下复苏,关键词只有一个:生存理念。为了生存,油气公司要在颇具挑战的页岩储层找到更加经济有效的开采方法。以下介绍的工具和装备代表了油气公司在推高北美油气产量上的最新进展。
自动系统用于阻垢剂评价
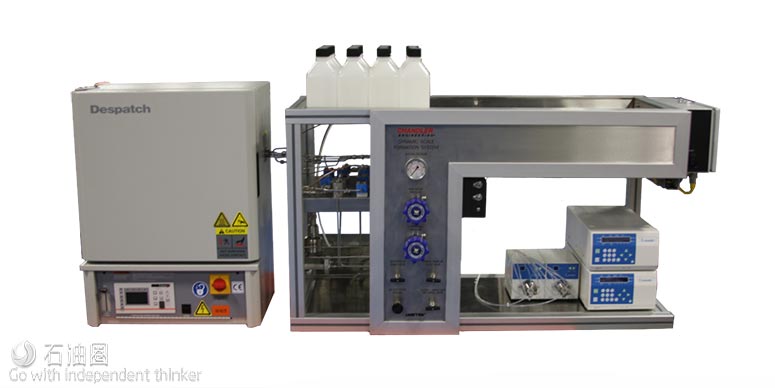
AMETEK Chandler工程公司设计的5400型动态积垢环路设备为全自动装置,用于测量并评价高温高压工况下阻垢剂的性能。该系统以某个确认的流量将加热油样泵送通过测试油管段,同时连续测量压差,并以压差的增大来作为垢形成的标志,当压差达到预设值时,测试结束。
该系统配有高精度空气对流烘箱、可拆除样品及预热管总成、带样品的外部pH电极以及烘箱内的高温合金C276样品导压及连接件。系统硬件包括:
1.两套手动设定点回压减压阀(高或低范围),用作建立测试段样品压力;
2.两台液相色谱泵,用作传送流体通过导压管;
3.两个都配有调节阀(6通路),用于导通阳离子、阴离子、阻垢剂或清洁剂。
胶封型生产系统克服多相流动的挑战
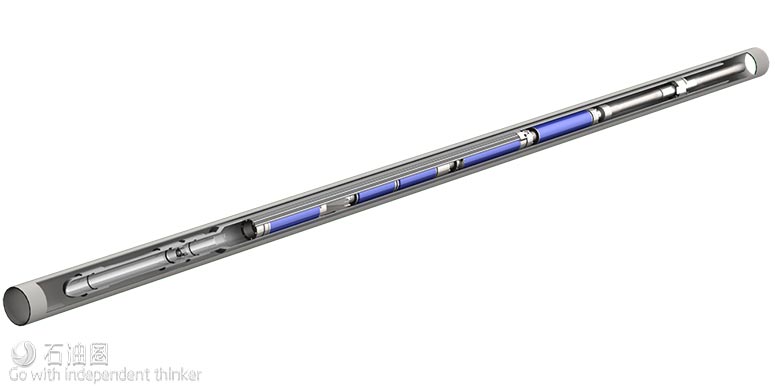
气体处理是电潜泵中最复杂的挑战之一。虽然电潜泵能够采收天然气,但大量的天然气会使传统装置的可靠性大打折扣。这一挑战在非常规油气开发中的大长度水平段会更加突出。段塞流聚集在水平段动态起伏上部,然后脱离,这样就会造成气栓的情况,进而造成系统关停以及/或机泵自循环,导致电机过热。
贝克休斯的CENesis PHASE多相胶封型生产系统将电潜泵完全裹在罩内,在进入泵以前将液流中的气体分离出。系统设计用于稳定产量,改善效率,同时减少与可靠性有关的问题。外壳为电潜泵提供了液体储存空间,可应对段塞流的情况,同时依靠一个再循环装置维持流体流经电机,用于避免出现过热的问题。上述系统已经在超过1000次的安装应用中取得成功。最近一口位于特拉华盆地的水平井,作业者凭借该系统实现增产48%,同时增加油藏压力降达40%。温度从80℃降至75.5℃。
气举系统提升巴肯页岩油产量
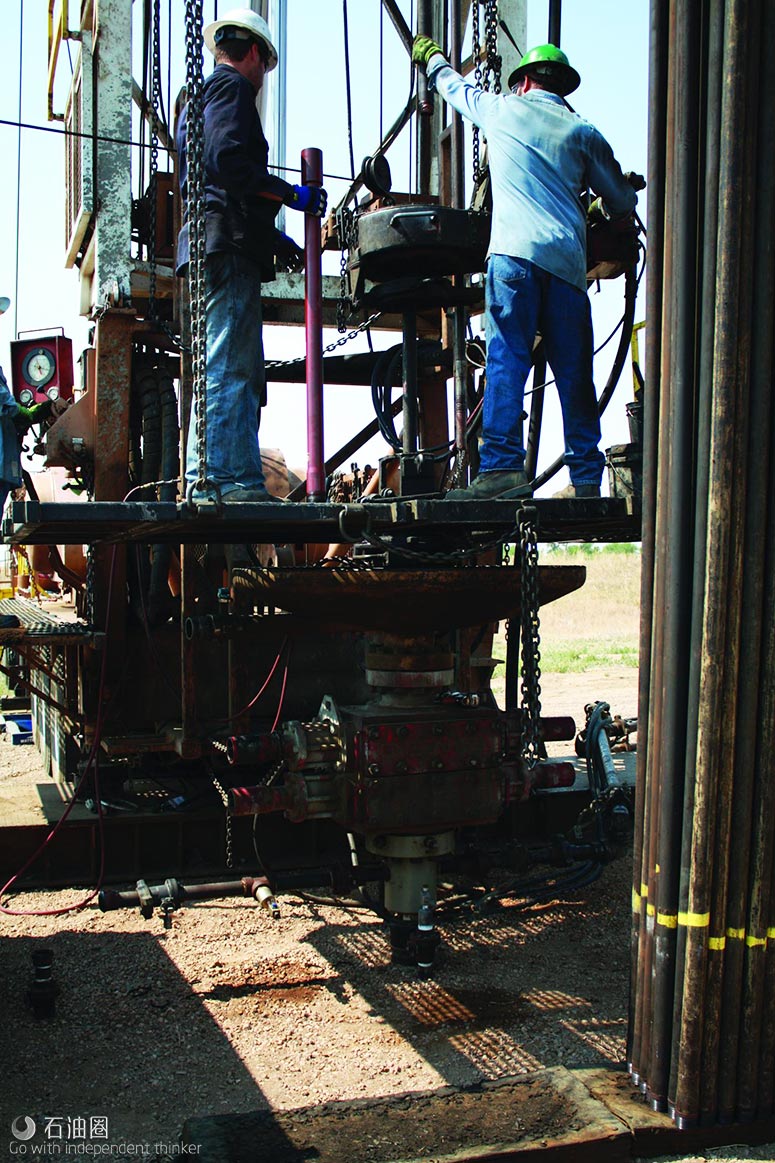
当油田作业者开采非常规页岩油气井时,从来不缺高难度挑战。但是要找到最佳的人工举升技术来应对这些挑战,却并没那么容易。在巴肯页岩区块,一个Dover公司人工举升系统的用户尝试在多偏离、高气水比(GLR)、高固相的工况下开采页岩油气。用户尝试使用两种不同的举升装置,但每隔2~4个月就会出现故障,停产导致的成本达数万美金。
于是,该用户开始寻找新的解决方案—气举系统。气举系统的移动部件均装在油管外部,不会暴露在井内流体环境下,所以也就不会受到固相与偏离的影响。此外,气举高度模仿自然生产条件下的井内工况,所以更高的气水比实际上反而会有利于系统运行。Dover公司的人工举升设备配有气举系统和一台压缩机,安装井已经连续生产18个月,为作业者节省了$200,000美金的停产损失。上述案例显示出,基于该气举系统的灵活性,它能够用于解决非常规页岩油气井常见的作业复杂性问题。
自动储罐测量提供更加精确的库存信息
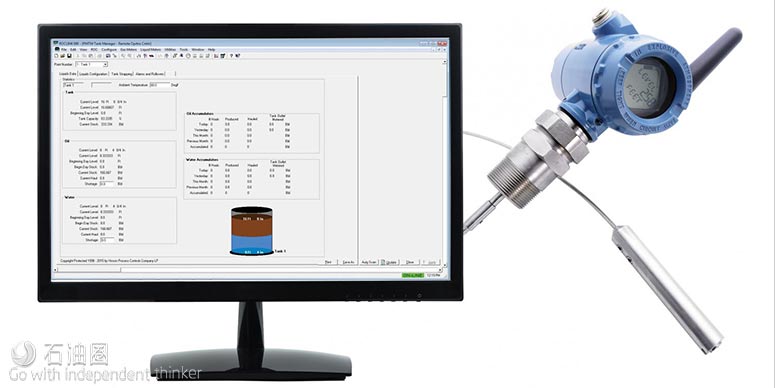
利用导波雷达液位计与无线技术,爱默生公司的一项新型自动储罐测量技术在实现降低作业者风险的同时,还可提高更加精确的库存信息。新型系统现能用于API MPMS Ch. 18. 2标准下原油的密闭输送。储罐测量技术进一步丰富了爱默生公司的储罐管理技术,实现了整个密闭输送流程的管理:自动托运票证,上传至生产财务系统,同时回配产液量到每口井 ,可用于实现更加精确的审计轨迹。
人工测量属于劳动密集型作业,存在极大的安全隐患,无论是极端天气还是有毒气体,都使这项作业存在很大的潜在风险。 这里举个例子:在页岩油气开采的过程中,1%的储罐测量误差就意味着$164,000/年的财政风险。自动储罐测量技术提供的是持续库存监测,通过识别油水界面将损失降至最低。信息通过无线传输至中控室,为操作人员提供远程数据监测、完全配置、高级数据分析以及故障排除工具。
您也有让人挠头的难题需要解决,或是优质技术想要找应用市场吗?如果有的话,欢迎联系小编微信或邮箱,也许能找到一剂良药。
柠檬:186-2292-2332;weiyameng@fonchan.com
二丫:131-3255-0596;zhanglingyu@fonchan.com
For English, Please click here (展开/收缩)
Outside of quantum physics, technically nothing is unpredictable. Even so, two years ago when analysts claimed the shale industry couldn’t sustain itself in sub- $60/bbl oil, few could have seen what lay ahead. And even fewer could have guessed the extraordinary growth in shale production would happen so rapidly.
There are several indicators that can identify when, exactly, the oil market bottomed out. By most accounts, rock bottom occurred sometime between January 2016, when West Texas Intermediate dove to $29/bbl, and the end of May 2016, when the U.S. rig count fell to 404 active rigs. Two years later, thanks primarily to an unexpected (but technically not totally unpredictable) boom in the shale industry, the U.S. is now a net oil producer, and rig counts have climbed back to 2015 levels.
According to Baker Hughes, the number of operational rigs in North America increased 124% in one year between May 2016 (404 rigs) and May 2017 (908 rigs). The reason for the sharp increase is almost exclusively due to the rise of shale production. More than 40% of all operating North American rigs are located in the Permian Basin—the epicenter for the shale boom.
Those additional rigs in shale plays have led to substantial increases in oil production, with the U.S. now producing 9.3 MMbbl/d, a figure not consistently achieved since the late 1960s and early 1970s.
The reason behind the U.S. oil production resurgence in a sub-$60/bbl economy is rooted in the concept of survival. To survive, companies needed to find a way to produce oil in challenging shale reservoirs in a more economical way. The tools and systems featured in E&P’s shale technology showcase represent some of the latest efforts companies have made to push North American production even higher through more efficient processes, deeper wells and longer laterals.
AUTOMATED SYSTEM EVALUATES SCALE INHIBITORS
The Model 5400 Dynamic Scale Deposition Loop from AMETEK Chandler Engineering is a fully automated system that measures and evaluates the performance of scale inhibitors under the HP/HT conditions found in oil production. The system pumps precisely heated oil samples at known rates through a tubing test section while continuously measuring the differential. An increase in differential pressure serves as an indication of scale formation, and the test is completed once that differential pressure reaches an adjustable threshold value. The system features a highly precise forced air convection oven, removable sample and preheat tube assembly, external pH electrode with sample, and Hastealloy C276 sample tubing and fittings inside the oven. System hardware includes two manual set point backpressure regulators (high or low range) that are used to create the sample pressure inside the test section during pumping. Two high-performance liquid chromatography pumps are used to transport the fluids through the tubing, both with switching valves (6-port) for various anion, cation, scale inhibitor or cleaning fluids.
ENCAPSULATED PRODUCTION SYSTEM OVERCOMES MULTIPHASE FLOW CHALLENGES
Gas handling is among the most complex challenges for electric submersible pumping (ESP) systems. While ESPs can produce some gas, large volumes can create reliability concerns for conventional systems. The challenges are exacerbated by long horizontals in unconventional oil plays. Gas slugs that accumulate in the high side of undulations in the lateral section and then break free can cause gas-locking conditions. The gas slugs could then shut down the system and/or pump cycling, which can lead to motor overheating. Baker Hughes’ CENesis PHASE multiphase encapsulated production system fully encapsulates the ESP in a shroud to naturally separate gas from the fluid stream before it can enter the pump. The system is designed to help stabilize production rates, improve efficiency and eliminate reliability issues. The shroud provides a reservoir of fluid to keep the ESP operating during gas slug events, while a recirculation system keeps fluid flowing past the motor to mitigate overheating. The system has proved successful in more than 1,000 installations. Recently in a horizontal well in the Delaware Basin, installing the system enabled an operator to increase oil production by 48% and increase reservoir pressure drawdown by 40%. Motor temperature was reduced from 80 C (176 F) to 75.5 C (168 F).
GAS-LIFT SYSTEM INCREASES PRODUCTION AT BAKKEN WELL
There is no shortage of challenges that need to be overcome when oilfield operators produce unconventional shale wells, but identifying the best artificial lift technology to combat these challenges can be difficult. In the Bakken region, a Dover Artificial Lift customer was trying to produce an unconventional shale well with multiple deviations, high gas-liquid ratios (GLR) and solids production. The customer tried using two different methods of artificial lift, but the systems failed every two to four months, which cost thousands of dollars in downtime. Determined to find a better solution, the customer decided to try a gas-lift system. Because the moving parts of a gas-lift system are mounted on the outside of the tubing and are not exposed to wellbore fluids, the system is not affected by solids production or deviations. Moreover, gas lift closely mimics a naturally flowing well, so higher GLRs will actually improve the system’s operation. Dover Artificial Lift installed a gas-lift system and a compressor on the well, and the well has been running for 18 months without interruption, saving about $200,000 in downtime. This case illustrates that, because of its flexibility, gas lift can be a solution to address the operational complexities that are common in unconventional shale wells.
AUTOMATIC TANK GAUGING PROVIDES MORE ACCURATE INVENTORY MEASURES
An automatic tank gauging method from Emerson that uses guided wave radar and wireless technology is reducing operator risk while providing more accurate measurements of inventories. The new system is now acceptable for crude oil custody transfer from small lease tanks per the American Petroleum Institute’s MPMS Ch. 18.2 standard. The tank gauging technology complements Emerson’s tank manager application, which enables management of the entire custody transfer process—automating haul tickets, uploading to production accounting and allocating produced fluids back to each well—for a more accurate audit trail. Automatic tank gauging is an improvement over manual tank gauging, a labor-intensive process with considerable safety risks given that measurements often are taken during harsh weather and could potentially expose operators to toxic vapors from open hatches. These processes are also subject to measurement inaccuracies and production losses. For example, a 1% error in tank gauging on a typical shale production well represents an annual fiscal exposure of $164,000. Automatic tank gauging provides continuous insight into actual inventory levels and minimizes loss by offering oil and water interface detection. Information is wirelessly transmitted to control rooms where operators can remotely access measurements, full configurations, advanced diagnostics and troubleshooting tools.
未经允许,不得转载本站任何文章: