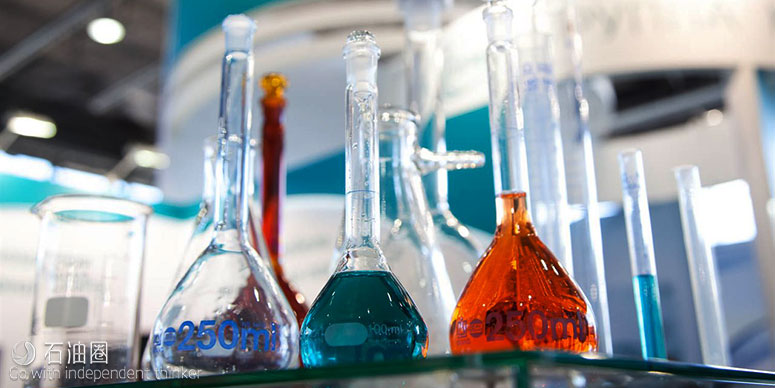
脱水作业是钻井液无害化处理中的重要环节,絮凝剂则是其中必不可少的化学添加剂,针对普通粉末式絮凝剂溶解慢、易结块等问题,微珠形式的絮凝剂带来了有效解决方式。
来自 | E&P
编译 | 白小明
当前的油气市场大环境迫使业内许多公司集中精力降低运营成本,努力在本轮持续时间较长的低油价时期保持竞争力。处在整个油气价值链上的所有企业不得不着重评估其产品和服务成本,同时还要努力提高效率,降低油气采收的盈亏平衡成本。而对水基钻井液进行有效脱水,则可使作业公司和油服公司在减少钻井废弃物的同时,增加钻井进尺。
钻井液的脱水是油气上游行业钻井作业过程中的一个重要环节,该环节包括从泥浆体系中分离固相、循环利用脱出的水,并使固相废弃物得到妥善处理。良好的脱水作业有利于提高钻井液公司和油气作业公司的一系列运营效率。
水基钻井液的脱水过程可能产生大量的废弃物,这些废弃物必须在开放的泥浆坑或在闭合回路(泥浆不落地设备)中得到处理。闭合系统可连续处理泥浆中的钻屑,在同等资源条件下,钻井速度更快、钻的井更深。使用该系统,可减少钻井废弃物产生量和相应的处理成本。
此外,闭合系统的占地面积小,可使油服公司更易达到当地环境法规的要求。泥浆脱水可以提高机械钻速,改善泥饼的完整性,并减少水和钻井泥浆添加剂的用量,从而有助于降低总钻井成本。
脱水化学添加剂
简言之,脱水过程即从钻井液体系中分离出固相。该作业通常需要使用化学添加剂来提高脱水设备的整体性能。所使用的化学添加剂包括絮凝剂和助凝剂型聚合物,可通过物理方法改变钻井液体系的性质,使钻屑中的小颗粒聚集或“絮凝”在一起,逐渐变得足够大,以便使用离心机去除。
所添加的聚合物以聚丙烯酰胺(PAM)为基础,可能带正电、负电或呈中性。絮凝基于钻井液中的固相颗粒和PAM聚合物之间的相互作用而产生,而颗粒具有排斥其周围带类似电荷颗粒的能力。这些颗粒很难单独用固控设备去除,因为它们非常小,并且被其自身的电荷半径包围,电荷半径根据固相的类型和数量或水相的特性而不同,所以必须减小电荷半径来使颗粒絮凝。
添加聚合物可使带电颗粒彼此接触,形成具有更高密度、更大体积的颗粒,从而被分离。
为了有效使小颗粒絮凝,PAM聚合物必须有合适的电荷密度和分子量。随着不断改进优化,聚合物与钻井液中的固体小颗粒之间的相互作用将更充分。BASF油田解决方案事业部的Alcomer 24产品,性能稳定,可用于多个泥浆体系。
聚合物形式
在选择用于脱水的聚合物时,需要同时评估聚合物优化后的性能以及其与泥浆的兼容性,而选择更加普遍易购买的产品也同样很重要。
脱水应用中有两种主要的聚合物形式:标准粉末和微珠。粉末产品往往具有锯齿状,颗粒不均匀,这种不均匀性容易导致结块、溶解不完全以及与粉尘相关的操作处理问题。因此,使用粉末产品往往难以操作处理。相反,创新的微珠具有均匀的结构,没有锯齿状边缘,溶解性更好,溶解度更大,方便操作处理。与粉末形式相比,微珠技术在溶解性、流动性等方面有了改善,低粉尘的特性使其易于操作处理,避免了冷冻/解冻的问题。
可用于水基钻井液作业的微珠产品系列非常多。油田领先的化学添加剂Alcomer 24,已成为了业内的拳头产品。Alcomer 24采用基于低阴离子聚丙烯酰胺产品的微珠形式,专门设计用于水基钻井液的絮凝,为闭环处理系统提供良好的产品性能。由于采用微珠形式,该产品比许多粉末形式的竞争产品溶解性更好,在脱水作业中更高效。该产品更容易倾倒,比粉末产品更易配药。因其独特的物理形式,作业者在脱水作业中选择Alcomer 24,可以减少化学品的用量和成本。产品的溶解度和水化时间有突出优势,同时用量更少。在泥浆体系中使用Alcomer 24后,一些用户报告称,化学品的使用量降至了粉末产品用量的一半。
微珠添加剂可采用更少的用量,完成更长井段的钻进,从而提高作业的效率,降低钻井成本。一名用户在现场条件下比较了BASF的产品与其他粉末产品后,发现前者取得的效果令人瞩目。使用14袋阴离子粉末产品与6袋碳酸钙(CaCO3),作业者完成了564米(1,850英尺)进尺,即35米/袋(115英尺/袋)。而使用12袋Alcomer 24和8袋CaCO3,该用户可以完成792米(2,600英尺)的进尺,即56米/袋(185英尺/袋)。Alcomer 24使用户取得了额外40%以上的进尺,同时聚合物用量减少了14%。
这种作业效率的提高,连同化学添加剂用量的减少,可使用户每钻进1英尺就降低1美元成本。除了这些应用优化,用户也注意到了Alcomer 24的易操作性和良好的溶解性,整个溶解过程只需要10~15分钟,而粉末产品需要大约1小时。
The current market climate has forced industry players to focus on reducing their operating costs in an effort to remain competitive during this prolonged downturn. Across the value chain companies have been forced to evaluate the costs of their products and services while simultaneously striving for efficiencies to bring down breakeven extraction costs. The effective dewatering of water-based drilling muds allows operators and service providers to reduce drilling waste while increasing drilling footage, positioning them to remain successful in this competitive industry.
Dewatering of drilling muds is an essential component of upstream drilling operations. The process involves the separation of solids from the mud system, allowing the water to be recycled and the solids to be effectively treated. An adept dewatering operation can facilitate a number of operational efficiencies for fluid companies and oil and gas operators. The process of dewatering water-based drilling muds can produce large amounts of waste that must be treated either in open pits or in a closed loop. When this process is performed in a closed-loop system, it reduces the production of drilling waste and corresponding disposal costs. This system continually treats cuttings in the mud system, the efficiency of which allows wells to be drilled faster and deeper with the same resources. Furthermore, the reduced footprint of these operations can allow oilfield service providers to better comply with state and local environmental regulations. Dewatering the mud can improve penetration rates, improve filter cake integrity and reduce water and drilling fluid chemical use, thus contributing to a reduction in overall well costs.
Dewatering chemicals
In short, the dewatering process involves separating solids from the drilling mud system.Often it is necessary to use chemicals to enhance the overall performance of the dewatering equipment. The chemicals used are both coagulant- and flocculant- type polymers that are able to physically alter the properties to allow small particles from drilling cuttings to agglomerate or “flocculate” together so they are large enough to be removed by a centrifuge. For optimum and efficient solids removal onsite, experimentation is needed to determine the appropriate amount and type of polymer. These polymers are based on polyacrylamide (PAM) that are either positive, negative or neutrally charged. Flocculation is based on the interaction of the drilling mud particles and the PAM polymer. The particles have an electrical charge that repels the like-charged particles surrounding it. These particles are difficult to remove with solids control equipment alone as they are extremely small and are surrounded by their own charge radius, which can vary depending on the type and amount of the solids or the characteristics of the water phase. This charge radius must be reduced to allow the particles to flocculate.
The addition of a polymer-type chemistry allows charged particles to come in contact with each other, forming larger particles that are able to have a higher density and thus are able to be separated.
For a polymer to help flocculate the small particles effectively, the PAM polymer has to have the right charge density and molecular weight. As these aspects are more optimized, the polymer will interact more robustly with the solid small particles in the drilling mud. Alcomer 24 from BASF’s Oilfield Solutions Business has been designed to offer a large, robust performance over several mud systems.
Polymer forms
When selecting polymer for use in dewatering, along with evaluating optimized performance and compatibility with the muds it is important to also use products that are easy for an operator to use. There are two main types of polymer form that are used in dewatering applications: standard powder and microbeads. Powder products tend to be jagged with nonuniform particles. This nonuniform nature leads to clumping, incomplete dissolution and handling concerns related to dust particles. Powders are therefore often considered hard to handle in applications. Alternatively, the innovative microbeads have a uniform structure with no jagged edges, which can allow better dissolution, better solubility and better handling. Microbead technology offers improvement over powder forms in solubility, pourability, ease of handling with low dust and avoidance of freeze/thaw issues.
There is a wide range of bead products available for use in water-based drilling operations. A leading chemistry in the field, Alcomer 24 has become an industry mainstay. A low-anionic polyacrylamide-based product in microbead form, Alcomer 24 has been specifically designed to flocculate water-based drilling muds and provide better performance in closed-loop systems. As a result of its microbead form, the product offers more solubility than many powder competitors, which makes it more effective in dewatering operations. The product is more easily poured, allowing it to be more effectively dosed than powders, where clumping can cause handling challenges. As a result of its physical form, the selection of Alcomer 24 in dewatering applications can reduce overall chemical usage and expenditure. The product solubility and hydration time leads to superior performance in application, which can allow fluids companies to reduce flocculant chemical volumes. Through effective handling, customers can achieve proper chemical dosing and reduce potential wasted polymer from product clumping. When a mud system is optimized with Alcomer 24, some customers report a usage rate of half vs. the competitive powder offerings.
The additive can allow a longer well to be drilled with less product, thereby improving operational efficiency and reducing drilling costs. One customer saw impressive results in field conditions when comparing the BASF product against a competitor’s powder offering. Using 14 bags of a competitor’s anionic powder along with six bags of calcium carbonate (CaCO3), the customer drilled 564 m (1,850 ft), or 35 m/bag (115 ft/bag). Using 12 bags of Alcomer 24 and eight bags of CaCO3, this same customer was able to drill 792 m (2,600 ft), or 56 m/bag (185 ft/bag). Alcomer 24 permitted this customer to drill a 40% longer well with a 14% decrease in polymer volume. This increase in operational efficiency, coupled with a decrease in chemical dosage, allowed the customer to decrease costs on a dollar-per-foot basis. In addition to these application improvements, the customer noted the product’s ease of handling and improved solubility, with Alcomer 24 taking 10 minutes to 15 minutes vs. the powder product, which took about one hour.
Through the use of high-performance PAM products such as Alcomer 24, oilfield service providers can achieve operational efficiencies and reduce costs, helping them to compete in the current market climate.
未经允许,不得转载本站任何文章: