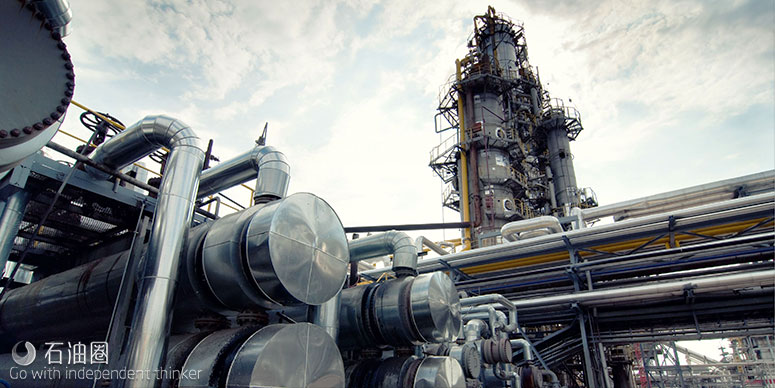
催化裂化是石油炼化过程中的重要工艺,巴斯夫在催化剂铁中毒及其对FCC催化剂的影响上有广泛的研究,Stamina催化剂就其多年研究的成果。
来自 | BASF
编译 | 二丫
催化裂化是在热和催化剂的作用下使重质油发生裂化反应,转变为裂化气、汽油和柴油等的过程,是一种非常重要的汽、柴油生产工艺,目前国内消费汽油约有75%来自催化裂化工艺。催化裂化过程中催化剂的作用非常重要,直接影响到产品质量和收率。国内外对于催化裂化催化剂的研究一直没有间断,为催化裂化工艺的发展做出了巨大贡献。
Stamina是一种重油流化催化裂化(FCC)反应催化剂。能够根据实际情况设计催化剂孔道结构,最大化轻质油品产量,保证油品质量,抑制焦炭生成。作业者利用Stamina能够将劣质的原料转化为具有较高经济效益成品油,炼厂试验表明使用该催化剂处理高金属含量的原料时能够显著提高轻质油品产量。
在上世纪90年代时,铁污染首次被确认为流化催化裂化(FCC)设备中的一大问题。巴斯夫在催化剂铁中毒及其对FCC催化剂的影响上有广泛的研究。本文对其中一些发现进行了简短的总结。
首先,了解铁的来源和如何量化FCC催化剂中的铁含量是非常重要的。因为铁自然存在于制备FCC催化剂所用的黏土中,所以新鲜的催化剂中本身就含有0.25-0.75wt%的铁。这种形式的铁并不参与任何副反应,也不会造成催化剂表面任何形式的堵塞。原油中与高分子质量的烃类物质结合在一起的铁原子才是问题的所在。
铁原子同时也可能来源于设备的腐蚀(游离铁),这部分铁的量非常有限,不是铁原子的主要来源。进料中的铁也会对催化剂造成影响,沉淀于FCC催化剂表面。
催化剂铁中毒
铁的化学或物理作用都会造成催化剂中毒,为催化裂化过程造成一系列的问题,其中铁对催化剂的化学作用影响要小于物理作用。由于铁原子具有脱氢作用,铁对催化剂的化学作用会导致反应的氢气和积炭含量增加,一氧化碳含量的稍许增加,同时造成硫元素从反应器转移到再生器,硫化物的排放增加。
催化剂受到铁的物理作用会造成催化剂表明结晶、融化或者降低催化剂表面积。催化剂中毒引起的最严重问题是催化剂孔道被堵塞,这会降低催化剂内部和外部分子的转移,最终造成焦炭和重油产量增加。
原料中的铁对催化剂造成影响的强度取决于催化剂类型、铁离子存在形式以及其他污染物的影响,受到污染的催化剂催化作用降低,从而降低原料转化率。对催化剂的孔隙率,特别是表面孔隙率进行优化可以降低铁对催化剂活性的影响,BASF的催化剂原位制造技术能够显著提高催化剂对铁的抗性。
从表面形态学来说,采用原位制造的催化剂有更高的表面孔隙率,这样它们也就能经受更高程度的铁垢。巴斯夫的催化剂已经成功应用于含铁2wt%原料的催化裂化应用中。
更高转的化率
巴斯夫着力解决铁在工业生产中造成的负面影响。在过去15年中,巴斯夫的催化剂从未因铁的影响而导致转化率的降低。下面这个案例分析描述了北美一个炼油厂在使用了巴斯夫的Stamina催化剂后的铁的偏移。
在几个月时间内,这家炼油厂在FCC设备中加工了高含铁量的进料。这家炼油厂观察到平衡状态时催化剂上附着的铁含量由1.17wt%增至1.48wt%,即进料中铁含量增加了45%。同时该炼油厂还发现,在平衡状态时,催化剂上钙和钠的含量也分别增加了23%和48%,镍(Ni)和钒(V)的含量则几乎保持不变。设备活性未曾减少,也没有造成过高的重油产量。
需注意的是,当转化率随着铁含量的增加而降低时,这通常意味着催化裂化进料性质的改变是转化率降低的主要原因,而不是由于铁含量的上升引起的转化率降低。在发生以上情况时,进料变重是Na和V含量提高、转化率降低的原因。
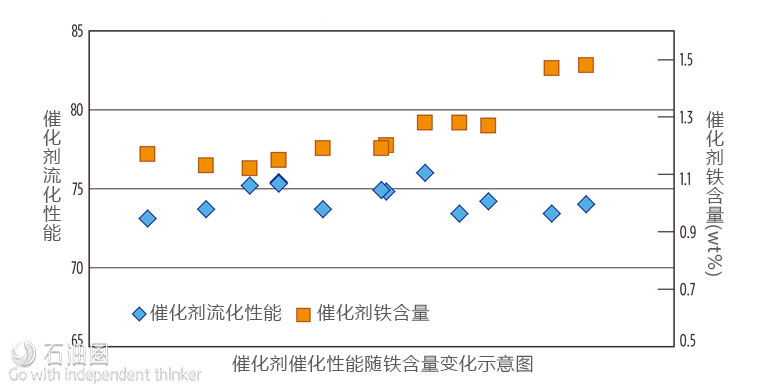
铁的流动性
巴斯夫研究的另一个关注点是铁的流动性。在研究铁的流动性时,区分催化剂颗粒内部金属原子的流动和催化剂颗粒间金属原子的流动是非常重要的。量化分子内金属原子流动的方法之一是使用扫面电子显微镜(SEM)获取反应平衡状态下催化剂颗粒横截面上的数据。
通过比较外层和内层的金属污染物含量可以得到催化剂的外围沉积指数(PDI)。例如,金属钒PDI数值接近于1,说明钒在催化剂分子中接近于均匀分布,即有比较高的分子内流动性。铁的PDI数值范围从4到7以上不等,说明铁的分子内流动性比较低,与镍的分散情况相似。
为了研究催化剂颗粒间金属原子的转移,研究人员采用了很多方法对反应平衡状态下的催化剂颗粒进行了表征。利用催化剂颗粒的密度差异,采用悬浮法对催化剂颗粒进行了分离,结果显示平衡状态下铁原子附着的催化剂颗粒密度与具有高转移活性的V、低转移活性的Ni催化剂颗粒密度差异明显。
而从平衡态催化剂的整体的SEM数据来看,新、旧催化剂颗粒可以通过表面制图很明显地区分出来,说明铁的流动性与钒的流动性有明显的区别。总的来说,在对一系列商用设备的研究后表明,Fe并不像V一样有很高的催化剂颗粒间流动性。
每一次技术的更新都经过科研人员的艰苦努力,Stamina是BASF多年研究的成果,相信Stamina在催化裂化工艺中一定会发挥出巨大的作用。
CSSOPE揭秘2017全球石油化工装备采购新动向
日前,总部位于阿联酋迪拜的BSL集团CPO与第七届中国石油化工装备采购国际峰会暨展览会组委会确认将出席峰会演讲,发表主题为“国际买家与中国石油化工制造商/供应商高效合作的战略”的主题发言。据悉,该集团每年从中国采购的钢管等项目物资超过数十亿美元,今年来华意在加强与中国供应商的沟通交流,巩固战略合作,互利共赢。
作为国内首个为石油石化行业采购商与供应商搭建的专业交流对接平台,中国石油装备采购国际峰会(CSSOPE)凭借独特的市场定位及丰富的行业资源,已连续六年聚集国内外众多采购巨头,纷纷在此平台宣布未来在华采购的新动向及对供应商的新要求,为国内优秀供应商打开国际市场、取得跨国油气装备采购订单提供了广阔的市场机会。
近年来,CSSOPE参会人员逐年增加,分享技术新成果、前言信息、订单计划、发展趋势。很多中国石油石化装备设备制造企业在此平台上多次进行企业展示、产品推广、资本合作、技术对接与交流,能力和水平快速提升,市场份额逐步扩大,并在全球树立起“中国制造”品牌形象。
第七届中国石油化工装备采购国际峰会暨展览会(CSSOPE 2017)将于2017年5月24-25日在上海举办。了解详情请访问:http://www.petroequipsourcing.com/info/CN/
Iron (Fe) contamination was first recognized as a concern for fluid catalytic cracking (FCC) units in the 1990s. BASF has studied iron poisoning and its effects on FCC catalyst extensively, and a short summary of some of those findings is included here.
First, it is important to understand iron sources and how to quantify iron on FCC catalyst. Iron is inherent in the fresh catalyst, between 0.25 and 0.75 wt%, as it is a natural ingredient of clays used for manufacturing FCC catalysts; this type of iron does not participate in any side reactions nor cause any kind of catalyst surface blockage. The iron that is of concern comes in with the crude oil in the form of iron incorporated in high molecular weight hydrocarbons. Iron can also come from equipment corrosion (tramp iron), which is generally less of a concern. Iron from the feed deposits on the surface of the FCC catalyst, forming nodules. This is referred to as added iron.
Concerns with iron-poisoned catalysts
Units with iron-poisoned catalysts can face a number of problems, either from the chemical or physical effects of added iron. The chemical effects are often minor and include higher hydrogen (H2) and coke due to the dehydrogenation activity of iron, mild carbon monoxide (CO) promotion, and the transfer of sulfur (S) from the reactor to the regenerator, which can increase sulfur oxide (SOx) emissions. The physical effects include nodule formation (impacting catalyst circulation), vitrification and potentially reduced surface area. Severe poisoning leading to surface blockage, in which the pores are not accessible, is the most common concern. Surface blockage can prevent feed molecules from diffusing into the catalyst in the riser and products from diffusing out, leading to lower conversion, higher coke and higher slurry.
The amount of added iron that causes significant surface blockage and results in a loss of conversion depends heavily on the type of catalyst, the source of iron and other contaminants. Catalysts with optimized porosity, especially surface porosity, give improved iron tolerance. BASF practices in-situ manufacturing, which has been shown to improve iron tolerance.1 Based on surface morphology, in-situ manufactured catalysts have high surface porosity, which can withstand a higher degree of fouling due to iron. BASF catalysts have been successfully used in commercial applications with above 2 wt% equilibrium catalyst (Ecat) iron.
No loss of conversion
BASF follows iron upsets closely in the industry. In the past 15 years, BASF catalysts have not experienced a loss of conversion due to an iron upset. The case study below describes an iron excursion at a North American (NA) refinery using BASF’s Stamina catalyst. Over the course of a few months, the refinery introduced high iron feed into the FCC unit. The refinery saw iron on Ecat increase from 1.17 wt% to 1.48 wt%, representing a 45% increase in added iron (iron coming from the feed), as shown in TABLE 1. At the same time, they also saw calcium (Ca) and sodium (Na) on Ecat increase 23% and 48%, respectively, while nickel (Ni) and vanadium (V) werestable. The unit experienced no loss in activity or higher slurry yields (FIG. 1). Of note, when an increase in iron accompanies a loss in conversion, the higher iron is often an indicator of a feed change and does not cause the loss of conversion. In these cases, it is the heavier feed and increases in Na and V that result in the decreased conversion.
Differentiating iron mobility
Another area of BASF’s iron research is in the mobility of iron. When looking at iron mobility, or any metal mobility for that matter, it is important to differentiate between intraparticle mobility (within a single catalyst particle), and interparticle mobility (from particle to particle). One method of quantifying intraparticle mobility is by using scanning electron microscopy (SEM) data of cross sectional areas of Ecat particles. Comparing the amount of contaminant metal on the outer stages vs. the inner stages gives the peripheral deposition index (PDI).2 For context, vanadium typically has PDI values of close to 1, indicating close to uniform content of vanadium throughout the particle and thus high intraparticle mobility. Measured iron PDI values range from 4 to over 7, indicating low intraparticle mobility, similar to the deposition profile of nickel.
For interparticle mobility, a variety of techniques have been used to study bulk Ecat. Metals analysis of sink-float separated catalyst particles, where fractions are separated based on density, shows a standard deviation among fractions for iron between those of vanadium (high mobility) and nickel (low mobility). Looking at bulk Ecat in SEM, it can clearly be seen that there is a distinction between new (no iron) and old (high iron) catalyst particles via nodulation and surface mapping, indicating that the mobility profile of iron is distinctly different from that of V. In summary, across
a number of commercial units studied, iron does not show high interparticle mobility
like V.
Stamina: Fluid Catalytic Cracking (FCC) catalyst
Stamina is a distillate maximization Fluid Catalytic Cracking (FCC) catalyst providing measurable improvements in bottoms upgrading, light cycle oil quality and output, while preserving low coke yields.
Stamina is a Fluid Catalytic Cracking (FCC) catalyst for maximizing distillate yield from resid feeds
Stamina is a premium FCC catalyst that helps refiners process resid feedstocks to meet the growing global demand for diesel fuels.
How does Stamina work?
Stamina? is based on the new Prox-SMZ Technology Platform and combines the high matrix activity needed for light cycle oil (LCO) maximization and the enhanced macroporosity required for resid molecule access. The result — a high activity, high-stability matrix technology that cracks the heaviest resid feeds to maximize diesel yields.
What is the Prox-SMZ Technology Platform?
BASF has developed an innovative catalytic technology platform for maximizing distillate yields from a fluid catalytic cracking (FCC) unit. This unique platform, designated Prox-SMZ for Proximal Stable Matrix and Zeolite, combines attributes from both high zeolite and high matrix activity catalysts. The product is a stable and selective catalyst specifically designed for FCC distillate maximization.
What can Stamina do for refiners?
Stamina can help refiners meet the increased global demand for diesel fuels from the severest feeds. Recent trials have successfully demonstrated how well Stamina? can process feeds with higher levels of contaminant metals while reducing slurry yields.
未经允许,不得转载本站任何文章: